Preparation method of blended polyamide composite nanofiltration membrane
A composite nanofiltration membrane and polyamide technology, applied in chemical instruments and methods, membrane technology, semi-permeable membrane separation, etc., can solve the problems of reducing the performance of nanofiltration membranes, poor chlorine resistance of polyamide nanofiltration membranes, etc., and achieve good Effect of water flux and retention, low price, good chlorine resistance
- Summary
- Abstract
- Description
- Claims
- Application Information
AI Technical Summary
Problems solved by technology
Method used
Examples
Embodiment 1
[0029] The nanofiltration membrane prepared by blending the water phase monomer prepared by blending piperazine and m-xylylenediamine in the water phase at a ratio of 4:1 was installed on a low-pressure composite membrane test bench, and then the influent was chlorinated at 500 ppm Sodium solution and 2000ppm magnesium sulfate solution were tested for their water flux and interception after pre-pressing for one hour. The test results were that the water flux of sodium chloride was 63LMH, and the desalination rate was 62.1%; the flux of magnesium sulfate was 38LMH, the desalination rate is 99.4%.
Embodiment 2
[0031] The nanofiltration membrane prepared by blending the water phase monomer prepared by blending piperazine and m-xylylenediamine in the water phase at a ratio of 3:2 was installed on a low-pressure composite membrane test bench, and then the influent water was chlorinated at 500 ppm Sodium solution and 2000ppm magnesium sulfate solution were tested for their water flux and interception after pre-pressing for one hour. The test results were that the water flux of sodium chloride was 59LMH and the desalination rate was 58%; the flux of magnesium sulfate was 42LMH, the desalination rate is 99.0%.
Embodiment 3
[0033] The nanofiltration membrane prepared by blending the water phase monomer prepared by blending piperazine and m-xylylenediamine in the water phase at a ratio of 2:3 was installed on a low-pressure composite membrane test bench, and then the influent water was chlorinated at 500 ppm Sodium solution and 2000ppm magnesium sulfate solution were tested for their water flux and interception after pre-pressing for one hour. The test results were that the water flux of sodium chloride was 52LMH, and the desalination rate was 56.1%; the flux of magnesium sulfate was 38LMH, the desalination rate is 88.1%.
PUM
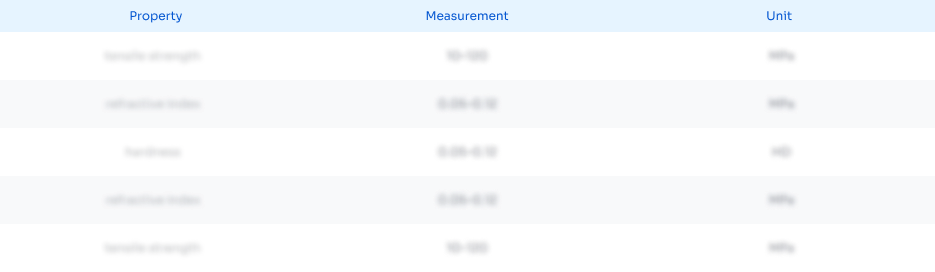
Abstract
Description
Claims
Application Information

- R&D
- Intellectual Property
- Life Sciences
- Materials
- Tech Scout
- Unparalleled Data Quality
- Higher Quality Content
- 60% Fewer Hallucinations
Browse by: Latest US Patents, China's latest patents, Technical Efficacy Thesaurus, Application Domain, Technology Topic, Popular Technical Reports.
© 2025 PatSnap. All rights reserved.Legal|Privacy policy|Modern Slavery Act Transparency Statement|Sitemap|About US| Contact US: help@patsnap.com