Direct steelmaking system and process for electric energy all-hydrogen flash reduction
An electrical and direct technology, applied in the metallurgical field, can solve the problems such as the inability to effectively solve the problem of steel energy consumption, large greenhouse gas and pollutant emissions, and achieve the effect of alleviating energy shortage, prolonging residence time, and reducing environmental load.
- Summary
- Abstract
- Description
- Claims
- Application Information
AI Technical Summary
Problems solved by technology
Method used
Image
Examples
Embodiment 1
[0066] A direct steelmaking process of electric energy full hydrogen flash reduction using the above-mentioned system and process, the process parameters involved in each step are as follows:
[0067] Step 1. Add liquid water to the electrolyzed water hydrogen production device, and perform water electrolysis to obtain pure hydrogen and oxygen. The purity of the hydrogen obtained is >99%, and the purity of oxygen is >99%;
[0068] Step 2. Add iron ore powder and flux powder to the preheating / prereduction device, the iron ore powder has a total iron TFe content of 30wt%, and the particle size is ≤1000 μm to obtain preheated / prereduced powder, iron ore powder and flux The powder is sprayed into the cyclone flash reduction furnace together with the preheated oxygen, in which the mass ratio of iron ore powder to oxygen is 1:5, hydrogen is blown into the hydrogen nozzle, and the volume ratio of hydrogen injection volume to oxygen injection volume is 100:5 , the temperature in the r...
Embodiment 2
[0072] A direct steelmaking process of electric energy full hydrogen flash reduction using the above-mentioned system and process, the process parameters involved in each step are as follows:
[0073] Step 1. Add liquid water to the electrolyzed water hydrogen production device, and perform water electrolysis to obtain pure hydrogen and oxygen. The purity of the hydrogen obtained is >99%, and the purity of oxygen is >99%;
[0074] Step 2. Add iron ore powder and flux powder to the preheating / prereduction device. The iron ore powder has a total iron TFe content of 50wt% and a particle size of ≤1000 μm. The iron ore powder and flux powder are blown into the cyclone flash together with the preheated oxygen Rapid reduction furnace, in which the mass ratio of iron ore powder to oxygen is 1:7, hydrogen gas is blown into the hydrogen nozzle, the volume ratio of hydrogen injection volume to oxygen injection volume is 100:7, and the temperature in the reduction furnace is controlled to ...
Embodiment 3
[0078] A direct steelmaking process of electric energy full hydrogen flash reduction using the above-mentioned system and process, the process parameters involved in each step are as follows:
[0079] Step 1. Add liquid water to the electrolyzed water hydrogen production device, and perform water electrolysis to obtain pure hydrogen and oxygen. The purity of the hydrogen obtained is >99%, and the purity of oxygen is >99%;
[0080] Step 2. Add iron ore powder and flux powder to the preheating / pre-reduction device. The iron ore powder has a total iron TFe content of 70wt% and a particle size of ≤1000 μm. The iron ore powder and flux powder are blown into the cyclone flash together with the preheated oxygen Rapid reduction furnace, wherein the mass ratio of iron ore powder to oxygen is 1:10, hydrogen is blown into the hydrogen nozzle, the volume ratio of hydrogen injection to oxygen injection is 100:10, and the temperature in the reduction furnace is controlled to be 500-1500 ℃; ...
PUM
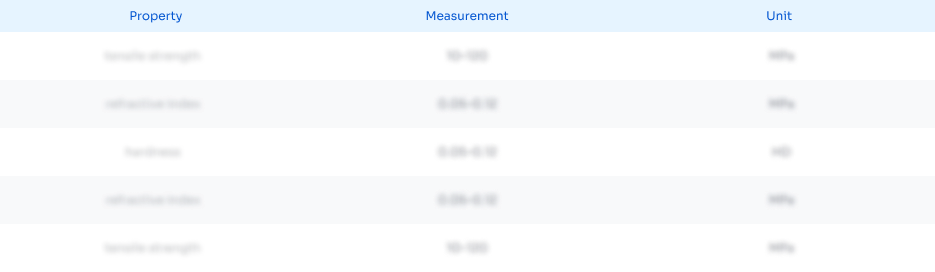
Abstract
Description
Claims
Application Information

- R&D
- Intellectual Property
- Life Sciences
- Materials
- Tech Scout
- Unparalleled Data Quality
- Higher Quality Content
- 60% Fewer Hallucinations
Browse by: Latest US Patents, China's latest patents, Technical Efficacy Thesaurus, Application Domain, Technology Topic, Popular Technical Reports.
© 2025 PatSnap. All rights reserved.Legal|Privacy policy|Modern Slavery Act Transparency Statement|Sitemap|About US| Contact US: help@patsnap.com