Polishing device, polishing method and polishing solution
A polishing liquid and equipment technology, applied in the polishing field, can solve problems such as damage to the surface of metal parts, large differences in polishing quality, and inapplicability, and achieve the effect of avoiding the overall structural impact
- Summary
- Abstract
- Description
- Claims
- Application Information
AI Technical Summary
Problems solved by technology
Method used
Image
Examples
Embodiment 1
[0070] Put a 3D printed titanium alloy workpiece into the polishing equipment for polishing. The roughness Ra before grinding is 10-11. The specific operations can be:
[0071] Open the upper cover of the equipment and put SiO into the polishing barrel according to the gravity ratio 2 20 parts of granules, 80 parts of water; then add 3 parts of anti-rust agent according to the volume ratio. Antirust agent is polyethylene glycol PEG-400.
[0072] The 3D printed titanium alloy workpiece is clamped on the fixture, and the fixture is fixed on the connecting shaft with screws.
[0073] Cover the upper cover, start the agitator motor and the workpiece rotation motor, set the agitator motor speed to 200r / min, and the workpiece rotation motor speed to 60r / min.
[0074] Run for 25 minutes, stop the two motors. Take out the 3D printed titanium alloy workpiece, and measure the surface roughness Ra to be 6-8.
Embodiment 2
[0076] Put a 3D printed titanium alloy workpiece into the polishing equipment for polishing. The roughness Ra before grinding is 10-11. The specific operations can be:
[0077] Open the upper cover of the equipment and put SiO into the polishing barrel according to the gravity ratio 2 20 parts of granules, 80 parts of water; then add 3 parts of anti-rust agent and 2 parts of lubricant according to the volume ratio. SiO 2 The average particle diameter is 50-60 nanometers, the antirust agent is polyethylene glycol PEG-400, and the lubricant is ethylene glycol and sodium phosphate.
[0078] The 3D printed titanium alloy workpiece is clamped on the fixture, and the fixture is fixed on the connecting shaft with screws.
[0079] Cover the upper cover, start the agitator motor and the workpiece rotation motor, set the agitator motor speed to 200r / min, and the workpiece rotation motor speed to 60r / min.
[0080] Run for 20 minutes, stop the two motors. Take out the 3D printed tit...
Embodiment 3
[0082] Put a 3D printed titanium alloy workpiece into the polishing equipment for polishing. The roughness Ra before grinding is 10-11. The specific operations can be:
[0083] Open the upper cover of the equipment and put SiO into the polishing barrel according to the gravity ratio 2 10 parts of granules, 90 parts of water; then according to the volume ratio, add 3 parts of anti-rust agent and 2 parts of lubricant. SiO 2 The average particle diameter is 50-60 nanometers, the antirust agent is polyethylene glycol PEG-400, and the lubricant is ethylene glycol and sodium phosphate.
[0084] The 3D printed titanium alloy workpiece is clamped on the fixture, and the fixture is fixed on the connecting shaft with screws.
[0085] Cover the upper cover, start the agitator motor and the workpiece rotation motor, set the agitator motor speed to 200r / min, and the workpiece rotation motor speed to 60r / min.
[0086] Run for 30 minutes, stop both motors. Take out the 3D printed titan...
PUM
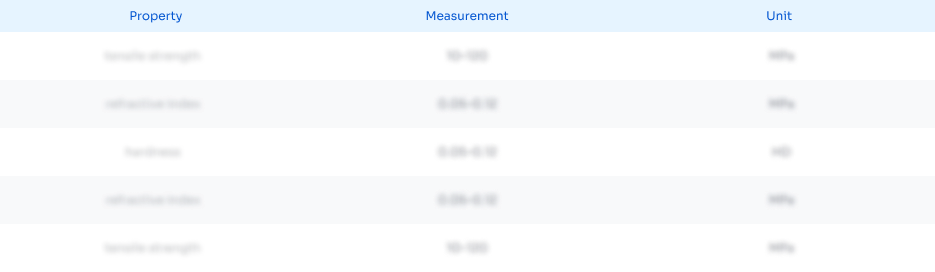
Abstract
Description
Claims
Application Information

- R&D
- Intellectual Property
- Life Sciences
- Materials
- Tech Scout
- Unparalleled Data Quality
- Higher Quality Content
- 60% Fewer Hallucinations
Browse by: Latest US Patents, China's latest patents, Technical Efficacy Thesaurus, Application Domain, Technology Topic, Popular Technical Reports.
© 2025 PatSnap. All rights reserved.Legal|Privacy policy|Modern Slavery Act Transparency Statement|Sitemap|About US| Contact US: help@patsnap.com