Low dielectric constant polyimide film and preparation method thereof
A technology of polyimide film and low dielectric constant, which is applied in the field of low dielectric constant polyimide film and its preparation, can solve problems such as environmental pollution, complicated process, and lower PI density, so as to achieve no pollution to the environment, Effect of cost reduction and process simplification
- Summary
- Abstract
- Description
- Claims
- Application Information
AI Technical Summary
Problems solved by technology
Method used
Image
Examples
Embodiment 1
[0023] In this embodiment, the low dielectric constant polyimide film material has the following structural formula:
[0024]
[0025] Under the condition of 25°C, dissolve 10.0g (0.05mol) 4,4'-diaminodiphenyl ether (ODA) in 100ml N,N-dimethylformamide DMF solvent, and then add 10.9g1,2 ,4,5-Pyromellitic dianhydride (PMDA) was subjected to polycondensation reaction (the molar ratio of ODA to PMDA was 1:1), and at the same time, 2g of aluminum triacetylacetonate was added for in-situ mixing, and the resulting mixed solution was stirred at room temperature Reaction 5h, obtain the mixed solution of polyimide precursor PAA and aluminum triacetylacetonate (AACA), i.e. PAA / AACA / DMF; PAA / AACA / DMF solution is carried out defoaming treatment, then this solution is evenly coated on The clean glass plate is placed in an oven for high-temperature thermal imidization treatment to obtain the low dielectric constant polyimide film.
[0026] In the above preparation method, the parameters...
Embodiment 2
[0028] In this embodiment, the low dielectric constant polyimide film material has the following structural formula:
[0029]
[0030] At 25°C, 5.4g (0.05mol) of p-phenylenediamine (PPD) was dissolved in 100ml of N,N-dimethylformamide DMF solvent, and then 14.7g of 3,3',4,4'- Biphenyltetracarboxylic dianhydride (BDPA) was subjected to polycondensation reaction (the molar ratio of PPD to BDPA was 1:1), and at the same time, 1g of aluminum triacetylacetonate was added for in-situ mixing, and the resulting mixed solution was stirred and reacted at room temperature for 5h to obtain A mixed solution of polyimide precursor PAA and aluminum triacetylacetonate (AACA), that is, PAA / AACA / DMF; defoaming the PAA / AACA / DMF solution, and then coating the solution evenly on a clean glass plate put into an oven for high-temperature thermal imidization treatment to obtain the low dielectric constant polyimide film.
[0031] In the above preparation method, the parameters of the high-tempera...
Embodiment 3
[0033] In this embodiment, the low dielectric constant polyimide film material has the following structural formula:
[0034]
[0035] Under the condition of 25°C, dissolve 20.5g (0.05mol) of 2,2-bis[4-(4-aminophenoxy)phenyl]propane (BAPP) in 250ml of N,N-dimethylformamide DMF solvent In, then add 16.1g3,3',4,4'---benzophenonetetraacid dianhydride (BTDA) for polycondensation reaction (the molar ratio of PPD and BDPA is 1:1), and at the same time add 3g triacetyl Aluminum acetonate is mixed in situ, and the resulting mixed solution is stirred and reacted at room temperature for 4h to obtain a mixed solution of polyimide precursor PAA and aluminum triacetylacetonate (AACA), namely PAA / AACA / DMF; for PAA / AACA / DMF The solution is subjected to defoaming treatment, and then the solution is evenly coated on a clean glass plate, and placed in an oven for high-temperature thermal imidization treatment to obtain the low dielectric constant polyimide film.
[0036] In the above prepar...
PUM
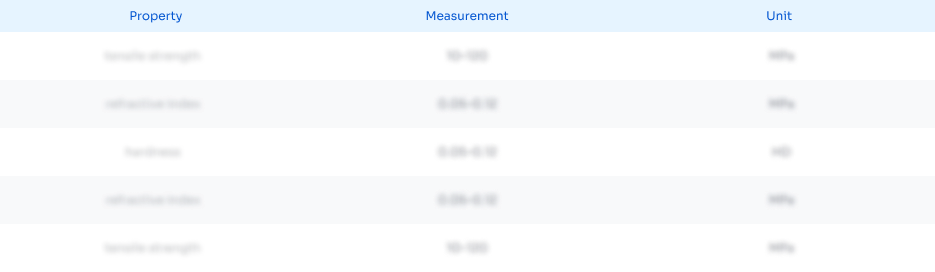
Abstract
Description
Claims
Application Information

- R&D Engineer
- R&D Manager
- IP Professional
- Industry Leading Data Capabilities
- Powerful AI technology
- Patent DNA Extraction
Browse by: Latest US Patents, China's latest patents, Technical Efficacy Thesaurus, Application Domain, Technology Topic, Popular Technical Reports.
© 2024 PatSnap. All rights reserved.Legal|Privacy policy|Modern Slavery Act Transparency Statement|Sitemap|About US| Contact US: help@patsnap.com