Method for manufacturing solder mask layer for improving hole plugging caused by solder resist ink
A technology of solder mask ink and production method, which is applied in the application of non-metallic protective layer, secondary treatment of printed circuit, processing of photosensitive materials, etc. The effect of increasing the washing pressure and reducing the production cost
- Summary
- Abstract
- Description
- Claims
- Application Information
AI Technical Summary
Problems solved by technology
Method used
Examples
Embodiment 1
[0017] This embodiment provides a method for manufacturing a solder resist layer that improves the blocking of holes with solder resist ink, which includes sequentially performing pre-solder resist treatment, silk screen solder resist ink, pre-baking, exposure, development, post-baking, and laser hole-burning processing on the production board process. The production board of this embodiment is a production board for testing, and the board thickness is about 1.5mm. On the board, some pads and some welding hole units arranged in a matrix are arranged. Each welding hole unit consists of 9 rows and each row has 9 rows. It consists of two welding holes, the welding holes are through holes with a diameter of 0.3mm.
[0018] Specific steps are as follows:
[0019] (1) Pre-treatment of solder resist: Grind the production board according to the conventional grinding process to clean and roughen the board surface, enhance the bonding force between the board surface and the solder resi...
Embodiment 2
[0030] This embodiment provides a method for manufacturing a solder resist layer that improves the blocking of holes with solder resist ink, which includes sequentially performing pre-solder resist treatment, silk screen solder resist ink, pre-baking, exposure, development, post-baking, and laser hole-burning processing on the production board process. The production board of this embodiment is a production board for testing, which is the same as that of Embodiment 1.
[0031] The difference between the manufacturing method of the solder resist layer and that of Example 1 lies in the control of the development process. The development process of this embodiment is as follows: The development process includes spraying of developing chemicals, preliminary rinsing, pressurized water washing, water washing, and strong wind blowing. Steps of drying and drying with hot air. The mass percent concentration of the developing solution is 0.9-1.1%. During the spraying process of the de...
Embodiment 3
[0034] This embodiment provides a method for manufacturing a solder resist layer that improves the blocking of holes with solder resist ink, which includes sequentially performing pre-solder resist treatment, silk screen solder resist ink, pre-baking, exposure, development, post-baking, and laser hole-burning processing on the production board process. The production board of this embodiment is a production board for testing, which is the same as that of Embodiment 1.
[0035] The difference between the manufacturing method of the solder resist layer and that of Example 1 lies in the setting of the shower head during the developing process. In this embodiment, a fan-shaped shower head is used for spraying during the spraying process of the developing liquid.
[0036] For the 10 production boards processed by the method of this embodiment, after the development process is completed, more solder resist ink remains in some welding holes on the production board, which increases th...
PUM
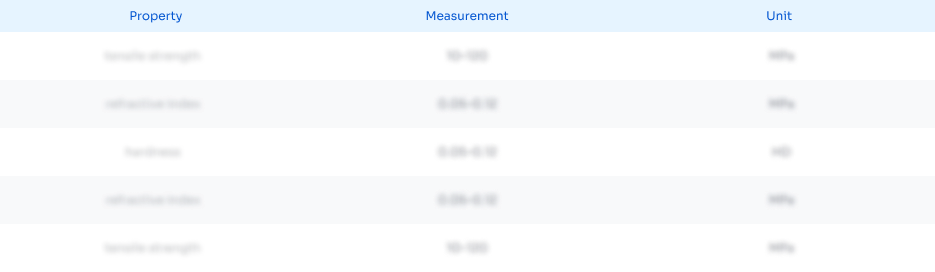
Abstract
Description
Claims
Application Information

- Generate Ideas
- Intellectual Property
- Life Sciences
- Materials
- Tech Scout
- Unparalleled Data Quality
- Higher Quality Content
- 60% Fewer Hallucinations
Browse by: Latest US Patents, China's latest patents, Technical Efficacy Thesaurus, Application Domain, Technology Topic, Popular Technical Reports.
© 2025 PatSnap. All rights reserved.Legal|Privacy policy|Modern Slavery Act Transparency Statement|Sitemap|About US| Contact US: help@patsnap.com