Prediction system and prediction method for tapping carbon component of 100t direct-current electric arc furnace
A DC electric arc furnace and forecasting system technology, applied in forecasting, electric furnace, steel manufacturing process and other directions, can solve the problems that are not conducive to the control of molten steel purity and the improvement of overall economic benefits, increase the difficulty of deoxidation and production costs, etc. Conducive to molten steel quality control, reducing cost waste and optimizing the effect of the process
- Summary
- Abstract
- Description
- Claims
- Application Information
AI Technical Summary
Problems solved by technology
Method used
Image
Examples
Embodiment 1
[0028] Tapping carbon content is 0.3% to 0.6%
[0029] Step 1. Enter the collected data into the system and save it.
[0030] Step 2: Calculate the corresponding tapping carbon content under the normal smelting conditions of the electric furnace through the method independently designed and developed:
[0031] Tapped carbon content% = adjustment factor K1*(7.73+1.65*Wc-0.00293*ton steel oxygen supply +0.0503*ton steel power supply), where K1 is between 0.005-0.02, Wc=(molten iron weight×hot metal carbon content + scrap weight × carbon content in scrap) / loading amount, 7.73 is the decarburization constant, 1.65 is the carbon distribution coefficient, 0.00293 is the oxygen supply coefficient, and 0.0503 is the power supply coefficient;
[0032] Step 3: Select the slagging parameters according to the specific situation on site and the phosphorus content requirements of the steel, R=K2*(W Si / 0.4), wherein K2 is between 1.8-2.5; Wsi=(molten iron weight×silicone content in molten...
Embodiment 2
[0036] Tapping carbon content is 0.1% to 0.3%
[0037] Step 1. Enter the collected data into the system and save it.
[0038] Step 2: Calculate the corresponding tapping carbon content under the normal smelting conditions of the electric furnace through the method independently designed and developed:
[0039] Tapped carbon content% = adjustment factor K1*(22.8+0.132Wc-0.0811*ton of steel oxygen supply-0.0177*ton of steel power supply), where K1 is between 0.005-0.02, Wc=(molten iron weight × molten iron carbon content + Scrap weight × carbon content in scrap) / charged amount;
[0040] Step 3: Select the slagging parameters according to the specific situation on site and the phosphorus content requirements of the steel, R=K2*(W Si / 0.4), wherein K2 is between 1.8-2.5, Wsi=(molten iron weight×silicone content of molten iron+scrap weight×silicon content in scrap steel) / loading capacity;
[0041] Step 4: Record and store the actual operating parameters and smelting results of...
Embodiment 3
[0044] Tapping carbon content is less than 0.1%
[0045] Step 1. Enter the collected data into the system and save it.
[0046] Step 2: Calculate the corresponding tapping carbon content under the normal smelting conditions of the electric furnace through the method independently designed and developed:
[0047] Tapped carbon content% = adjustment factor K1*(7.70+0.0922Wc-0.0661*ton of steel oxygen supply +0.00516*ton of steel power supply, where K1 is between 0.005-0.02, Wc=(weight of molten iron x carbon content of molten iron+ Scrap weight × carbon content in scrap) / charged amount;
[0048] Step 3: Select the slagging parameters according to the specific situation on site and the phosphorus content requirements of the steel, R=K2*(W Si / 0.4), wherein K2 is between 1.8-2.5, Wsi=(molten iron weight×silicone content of molten iron+scrap weight×silicon content in scrap steel) / loading capacity;
[0049] Step 4: Record and store the actual operating parameters and smelting r...
PUM
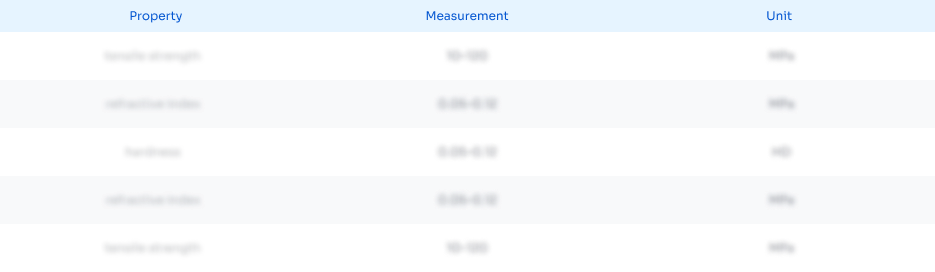
Abstract
Description
Claims
Application Information

- Generate Ideas
- Intellectual Property
- Life Sciences
- Materials
- Tech Scout
- Unparalleled Data Quality
- Higher Quality Content
- 60% Fewer Hallucinations
Browse by: Latest US Patents, China's latest patents, Technical Efficacy Thesaurus, Application Domain, Technology Topic, Popular Technical Reports.
© 2025 PatSnap. All rights reserved.Legal|Privacy policy|Modern Slavery Act Transparency Statement|Sitemap|About US| Contact US: help@patsnap.com