Method for preparing coated straw fiber-based water-retaining slow-release fertilizer
A straw fiber and coated technology, which is applied in the field of preparing coated straw fiber-based water-retaining slow-release fertilizer, can solve the problems of poor water-retaining performance and slow-release effect, waste of straw waste resources, and poor mechanical strength, etc., to achieve It is beneficial to the load capacity and retention, enhances the slow-release effect, and increases the effect of diffusion resistance
- Summary
- Abstract
- Description
- Claims
- Application Information
AI Technical Summary
Problems solved by technology
Method used
Image
Examples
Embodiment 1
[0030] 1) Extraction of cellulose: Wash and dry the wheat straw to remove impurities, crush it through 20 meshes to obtain straw powder, then add 10% nitric acid solution to the straw powder, the solid-to-liquid ratio is 1:30, Then heat and stir at 85°C for 3 hours. After the extraction is completed, cool to room temperature, and then filter, dry and grind to obtain cellulose powder;
[0031]2) Preparation of cellulose-based superabsorbent resin: add the cellulose powder prepared in step 1) into deionized water, fully stir and disperse in a water bath at 75°C for 30 minutes, then add potassium persulfate and sodium sulfite under nitrogen protection and stir 15min, the total mass ratio of cellulose powder to potassium persulfate and sodium sulfite mixed powder is 1:0.25, then add acrylic acid, urea and N,N-methylenebisacrylamide with a neutralization degree of 70% in sequence, cellulose powder, The mass ratio of acrylic acid, urea and N,N-methylenebisacrylamide is 1:1:0.2:0.05....
Embodiment 2
[0035] 1) Extraction of cellulose: the corn stalks were washed and dried to remove impurities, crushed to 20 meshes to obtain straw powder, and then 10% nitric acid solution was added to the straw powder with a solid-to-liquid ratio of 1:50. Then heat and stir at 110°C for 5 hours. After the extraction, cool to room temperature, and then filter, dry and grind to obtain cellulose powder;
[0036] 2) Preparation of cellulose-based superabsorbent resin: add the cellulose powder prepared in step 1) into deionized water, fully stir and disperse in a water bath at 80°C for 50 minutes, then add potassium persulfate and sodium sulfite under nitrogen protection and stir 20min, the total mass ratio of cellulose powder and potassium persulfate and sodium sulfite (the mass ratio of potassium persulfate and sodium sulfite is 1:1) is 1:0.4, and then add acrylic acid, urea and N with a neutralization degree of 70% in sequence. , N-methylenebisacrylamide, make the mass ratio of cellulose powd...
Embodiment 3
[0040] 1) Extraction of cellulose: wash and dry rapeseed stalks to remove impurities, crush them through 20 meshes to obtain straw powder, then add 10% nitric acid solution to the straw powder, the solid-to-liquid ratio is 1:50, Then heat and stir at 100°C for 4 hours. After the extraction, cool to room temperature, and then filter, dry and grind to obtain cellulose powder;
[0041] 2) Preparation of cellulose-based superabsorbent resin: Add the cellulose powder prepared in step 1) into deionized water, fully stir and disperse in a water bath at 70°C for 30 minutes, then add potassium persulfate and sodium sulfite under nitrogen protection and stir 30min, the total mass ratio of cellulose powder and potassium persulfate and sodium sulfite (the mass ratio of potassium persulfate and sodium sulfite is 1:1) is 1:0.3, and then add acrylic acid, urea and N , N-methylenebisacrylamide, the mass ratio of cellulose powder, acrylic acid, urea and N,N-methylenebisacrylamide is 1:1:0.3:0....
PUM
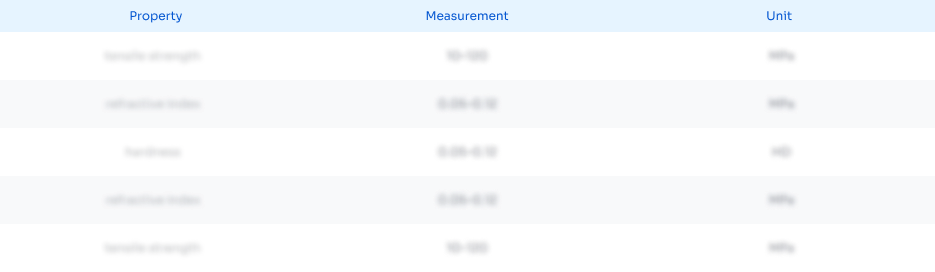
Abstract
Description
Claims
Application Information

- Generate Ideas
- Intellectual Property
- Life Sciences
- Materials
- Tech Scout
- Unparalleled Data Quality
- Higher Quality Content
- 60% Fewer Hallucinations
Browse by: Latest US Patents, China's latest patents, Technical Efficacy Thesaurus, Application Domain, Technology Topic, Popular Technical Reports.
© 2025 PatSnap. All rights reserved.Legal|Privacy policy|Modern Slavery Act Transparency Statement|Sitemap|About US| Contact US: help@patsnap.com