Method for preparing anhydrous ethylenediamine from double-amino silane byproduct ethylenediamine dihydrochloride
A technology for the production of ethylenediamine hydrochloride and ethylenediamine hydrochloride, which is applied in the field of producing anhydrous ethylenediamine to achieve the effects of reducing production costs, low moisture content of products, and reducing raw material consumption
- Summary
- Abstract
- Description
- Claims
- Application Information
AI Technical Summary
Problems solved by technology
Method used
Examples
Embodiment 1
[0021] In the 3-ton rake reactor, first pump in 1 ton of diaminosilane by-product ethylenediamine hydrochloride, 0.8 tons of ethylenediamine solvent, turn on the stirring, the stirring speed is 40 rpm, and then add 0.4 tons of oxidation calcium powder. After feeding the materials, the rake reactor was first heated to 70°C, and the stirring speed was 40 rpm for neutralization reaction for 2 hours, and then the temperature of the kettle was raised to 115°C to continue the heat preservation reaction for 6 hours. After the reaction was completed, the neutralization reaction device was changed to an ordinary distillation device, and distillation was carried out under vacuum at -0.09MPa. The maximum distillation temperature was 160°C, and 1.48 tons of ethylenediamine containing water was obtained. The detected moisture content was 2.4%, and the product yield was 95.2%. Give out 718 kilograms of calcium salt powder mixture.
[0022] Pump 1.48 tons of distilled ethylenediamine with a...
Embodiment 2
[0025] In the 3-ton rake reactor, first pump in 0.92 tons of bisaminosilane by-product ethylenediamine hydrochloride, 0.8 tons of ethylenediamine solvent, turn on the stirring, the stirring speed is 40 rpm, and then add 0.4 tons of oxidation calcium powder. After feeding the materials, the rake reactor was first heated to 80°C, and the stirring speed was 40 rpm for neutralization reaction for 2 hours, and then the temperature of the kettle was raised to 110°C to continue the heat preservation reaction for 6 hours. After the reaction was completed, the neutralization reaction device was changed to an ordinary distillation device, and distillation was carried out under vacuum at -0.1MPa. The maximum distillation temperature was 160°C, and 1.40 tons of ethylenediamine containing water was obtained. The detected moisture content was 2.1%, and the product yield was 93.8%. Give out 712 kilograms of calcium salt powder mixture.
[0026] Pump 1.4 tons of distilled ethylenediamine wit...
PUM
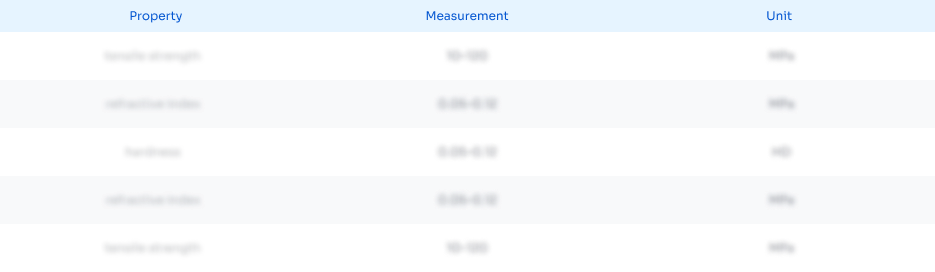
Abstract
Description
Claims
Application Information

- R&D
- Intellectual Property
- Life Sciences
- Materials
- Tech Scout
- Unparalleled Data Quality
- Higher Quality Content
- 60% Fewer Hallucinations
Browse by: Latest US Patents, China's latest patents, Technical Efficacy Thesaurus, Application Domain, Technology Topic, Popular Technical Reports.
© 2025 PatSnap. All rights reserved.Legal|Privacy policy|Modern Slavery Act Transparency Statement|Sitemap|About US| Contact US: help@patsnap.com