Energy-saving dyeing and finishing process
An energy-saving, dyeing and finishing technology, applied in the textile field, can solve the problems of cotton fiber damage, consumption of large water resources and heat energy, poor hand feeling of cotton knitted fabrics, etc., to improve the quality of dyeing and color fixing, reduce production costs, and reduce damage. Effect
- Summary
- Abstract
- Description
- Claims
- Application Information
AI Technical Summary
Problems solved by technology
Method used
Examples
Embodiment 1
[0051] An energy-saving dyeing and finishing process, comprising the following steps:
[0052] step one:
[0053] Configure a bath including the following components:
[0054] Anti-wrinkle agent: 1-2g / L
[0055] Degreaser: 1-2g / L
[0056] Leveling agent: 0.1-0.5 g / L
[0057] Yuanming powder: 2g / L
[0058] Glacial acetic acid (97%): 0.3g / L
[0059] Disperse dyes: 1 g / L
[0060] Anti-precipitation agent: 2g / L
[0061] Ordinary cationic dyes: 2 g / L
[0062] Glacial acetic acid (97%): 0.2g / L
[0063] Refining solution: 5 g / L;
[0064] Step 2: Putting the cloth into the treatment solution for polishing and dyeing, wherein the mass ratio of the cotton knitted fabric to the treatment solution is 1:10;
[0065] Step 3: Soaping the cotton knitted fabric after the polishing and dyeing treatment, and putting it into the color-fixing solution after soaping for color-fixing treatment; wherein the mass ratio of the cotton knitted fabric to the color-fixing solution is 1:8;
[006...
PUM
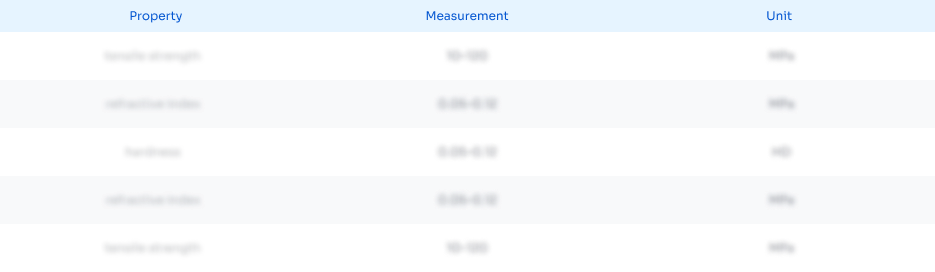
Abstract
Description
Claims
Application Information

- Generate Ideas
- Intellectual Property
- Life Sciences
- Materials
- Tech Scout
- Unparalleled Data Quality
- Higher Quality Content
- 60% Fewer Hallucinations
Browse by: Latest US Patents, China's latest patents, Technical Efficacy Thesaurus, Application Domain, Technology Topic, Popular Technical Reports.
© 2025 PatSnap. All rights reserved.Legal|Privacy policy|Modern Slavery Act Transparency Statement|Sitemap|About US| Contact US: help@patsnap.com