Method for preparing biomass carbon loaded cobalt phosphide electrode material through one-step calcination
A biomass carbon and electrode material technology, applied in the preparation/purification of carbon, electrodes, phosphides, etc., can solve the problems of high energy consumption, complex process flow, high reaction temperature, high conductivity, simple industrial process, high purity effect
- Summary
- Abstract
- Description
- Claims
- Application Information
AI Technical Summary
Problems solved by technology
Method used
Image
Examples
Embodiment 1
[0030] Weigh 1g of ginkgo biloba powder, 1.5g of ammonium nitrate and 0.25g of cobalt nitrate and mix, add 12g of deionized water, ultrasonic for 1h, then place in a 40°C oven for 24h. Put the dried product at the end of the porcelain boat, weigh 1g of sodium hypophosphite at the front of the porcelain boat, half-wrap the porcelain boat with aluminum foil and place it in a nitrogen atmosphere tube furnace. Calcined at 300° C. for 1 h at a heating rate of 3° C. / min to obtain a black product. XRD patterns such as figure 1 As shown in middle a, the XRD curve conforms to the XRD standard card of cobalt phosphide (JCPDS NO.29-497 and JCPDS NO.32-306), indicating that biomass carbon-supported cobalt phosphide was successfully prepared; figure 2 As shown in a, cobalt phosphide is dispersed in the form of spherical particles on the biomass carbon.
Embodiment 2
[0032] Weigh 1g of ginkgo biloba powder, 1.5g of ammonium nitrate and 0.5g of cobalt nitrate and mix, add 12g of deionized water, ultrasonicate for 2h, and then place in a 75°C oven for 24h. Put the dried product at the end of the porcelain boat, weigh 2g of sodium hypophosphite at the front of the porcelain boat, half-wrap the porcelain boat with aluminum foil and place it in a nitrogen atmosphere tube furnace. Calcined at 500° C. for 3 h at a heating rate of 3° C. / min to obtain a black product. XRD patterns such as figure 1 As shown in middle b, the XRD curve conforms to the XRD standard card of cobalt phosphide (JCPDS NO.29-497 and JCPDS NO.32-306), indicating that biomass carbon-supported cobalt phosphide was successfully prepared; figure 2 As shown in b, cobalt phosphide is dispersed on the biomass carbon in a spherical shape.
Embodiment 3
[0034] Weigh 2g of ginkgo biloba powder, 3g of ammonium nitrate and 2g of cobalt nitrate and mix, add 24g of deionized water, ultrasonicate for 6h, then place in an oven at 80°C for 36h to dry. Put the dried product at the end of the porcelain boat, weigh 8g of sodium hypophosphite at the front of the porcelain boat, half-wrap the porcelain boat with aluminum foil and place it in a nitrogen atmosphere tube furnace. Calcined at 500° C. for 3 h at a heating rate of 3° C. / min to obtain a black product. XRD patterns such as figure 1 As shown in c, the XRD curve conforms to the XRD standard card of cobalt phosphide (JCPDS NO.29-497 and JCPDS NO.32-306), indicating that biomass carbon-supported cobalt phosphide was successfully prepared; figure 2 As shown in c, cobalt phosphide is dispersed in the form of spherical particles on the biomass carbon.
PUM
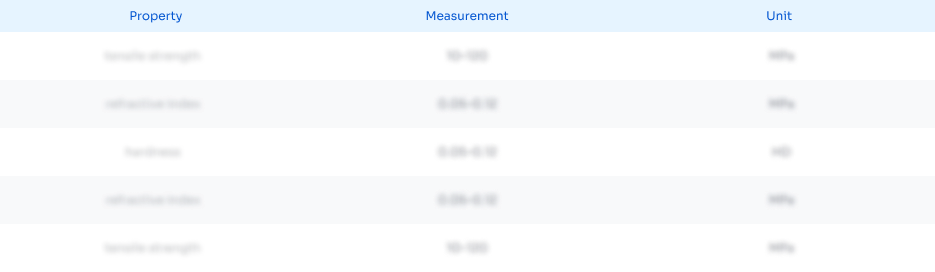
Abstract
Description
Claims
Application Information

- R&D Engineer
- R&D Manager
- IP Professional
- Industry Leading Data Capabilities
- Powerful AI technology
- Patent DNA Extraction
Browse by: Latest US Patents, China's latest patents, Technical Efficacy Thesaurus, Application Domain, Technology Topic, Popular Technical Reports.
© 2024 PatSnap. All rights reserved.Legal|Privacy policy|Modern Slavery Act Transparency Statement|Sitemap|About US| Contact US: help@patsnap.com