A kind of preparation method of iron phosphide loaded graphene foam composite material
A graphene foam, composite material technology, applied in chemical instruments and methods, nanotechnology for materials and surface science, chemical/physical processes, etc. , difficult to effectively control and other problems, to achieve the effect of easy large-scale generation, strong repeatability, and short reaction time
- Summary
- Abstract
- Description
- Claims
- Application Information
AI Technical Summary
Problems solved by technology
Method used
Image
Examples
Embodiment 1
[0026] Weigh 1.2g Fe(NO 3 ) 3 9H 2 O and 0.8g polyvinylpyrrolidone (PVP, K30) are completely dissolved in 40ml deionized water to make a transparent colloidal liquid, then put into an oven, and dry at 50°C for 12h to obtain an orange-yellow flaky block; Grind the flaky block into a powder with a particle size of ~100 mesh in a mortar, weigh 1.0g and put it into a 30ml burning boat with a cover, put it into a tube furnace, use an argon atmosphere, and heat it at 3°C / min Heating rate of heating to 500°C, holding for 1h, then slowly cooling to 230°C, holding for 1h in the air atmosphere, then cooling to room temperature, collecting precursor A, and then weighing 0.5g of precursor A into CVD small At one end of the tube furnace quartz furnace tube near the gas outlet, put 10g Na 2 h 2 PO 2 Place it at the end close to the gas inlet, adjust the argon gas flow rate to 80 sccm, raise the temperature to 360°C at 2°C / min, keep it warm for 6h, and then slowly cool to room temperatu...
Embodiment 2
[0028] Weigh 1.0g Fe(NO 3 ) 3 9H 2 O and 1.6g polyvinylpyrrolidone (PVP, K30) are completely dissolved in 35ml deionized water to make a transparent colloidal liquid, then put into an oven, and dry at 45°C for 24h to obtain an orange-yellow flaky block; Grind the flaky block into a powder with a particle size of ~50 mesh with a mortar, weigh 1.6g and put it into a 30ml burning boat with a cover, put it into a tube furnace, use a nitrogen atmosphere, and set the temperature at 4°C / min. Heating rate to 490°C, keep warm for 50min, then slowly cool to 260°C, keep warm in air atmosphere for 1h, then cool to room temperature, collect precursor A, then weigh 0.5g of precursor A into CVD small tube One end of the furnace quartz furnace tube near the gas outlet, put 10g Na 2 h 2 PO 2 Place it at the end close to the gas inlet, adjust the argon gas flow rate to 80 sccm, raise the temperature to 360°C at 2°C / min, keep it warm for 10h, and then slowly cool to room temperature to obta...
Embodiment 3
[0030] Weigh 1.2g Fe(NO 3 ) 3 9H 2O and 0.4g polyvinylpyrrolidone (PVP, K30) are completely dissolved in 35ml deionized water to make a transparent colloidal liquid, then put into an oven, and dry at 45°C for 16h to obtain an orange-yellow flaky block; Grind the flaky block into a powder with a particle size of ~200 mesh with a mortar, weigh 2.0g and put it into a 30ml burning boat with a cover, put it into a tube furnace, use an argon atmosphere, and heat it at 4°C / min Heating rate of heating to 480°C, holding for 1 hour, then slowly cooling to 200°C, holding for 0.5 hours in the air atmosphere, then cooling to room temperature, collecting precursor A, and then weighing 0.5g of precursor A into CVD small At the end of the tube furnace quartz furnace tube near the gas outlet, put 6g Na 2 h 2 PO 2 Place it at the end close to the gas inlet, adjust the argon gas flow rate to 100 sccm, raise the temperature to 400 °C at 1 °C / min, keep it for 6 hours, and then slowly cool to ...
PUM
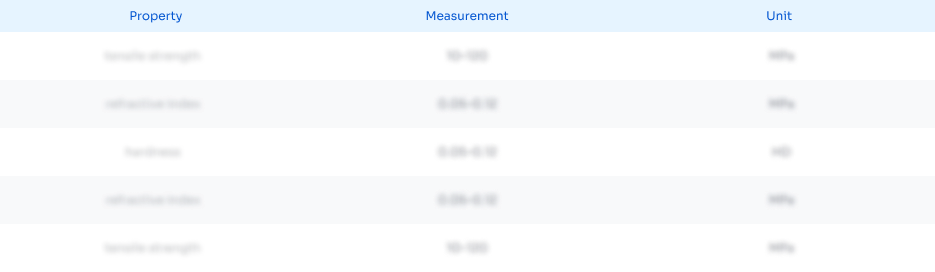
Abstract
Description
Claims
Application Information

- R&D
- Intellectual Property
- Life Sciences
- Materials
- Tech Scout
- Unparalleled Data Quality
- Higher Quality Content
- 60% Fewer Hallucinations
Browse by: Latest US Patents, China's latest patents, Technical Efficacy Thesaurus, Application Domain, Technology Topic, Popular Technical Reports.
© 2025 PatSnap. All rights reserved.Legal|Privacy policy|Modern Slavery Act Transparency Statement|Sitemap|About US| Contact US: help@patsnap.com