High-precision bearing forge piece machining method
A processing method and high-precision technology, which is applied in the field of high-precision bearing forging processing, can solve the problems affecting the service life of the processing size tool, the deformation of the outer ring of the bearing, the vibration of the tool, and the chipping of the tool, so as to reduce the size of defective products and ensure the temperature difference. Effects of changing and ensuring service life
- Summary
- Abstract
- Description
- Claims
- Application Information
AI Technical Summary
Problems solved by technology
Method used
Image
Examples
Embodiment 1
[0093] A processing method for a high-precision bearing forging, the processing method comprising the following steps:
[0094] 1. Blank inspection
[0095] 1) First, manually screen the rough parts of the outer ring of the bearing, observe whether there are any defects in the appearance of the rough parts, such as fleshy or lacking meat, mark the defective parts, and return them to the furnace for recasting.
[0096] 2) Use an ultrasonic flaw detector to inspect the interior of the rough parts for good appearance products to detect whether there are blisters, pores, white spots, cracks and other defects in the rough parts, mark the defective parts, and return them to the furnace for recasting.
[0097] The operating frequency of the ultrasonic flaw detector is 2.5MHz, and the ambient temperature of the flaw detection is 20-25 degrees Celsius.
[0098] 2. Parts benchmark processing
[0099] 1) place
[0100] Use a vertical lathe to rough-machine the blank, put the blank on ...
Embodiment 2
[0130] A processing method for a high-precision bearing forging, the processing method comprising the following steps:
[0131] 1. Blank inspection
[0132] 1) First, manually screen the rough parts of the outer ring of the bearing, observe whether there are any defects in the appearance of the rough parts, such as fleshy or lacking meat, mark the defective parts, and return them to the furnace for recasting.
[0133] 2) Use an ultrasonic flaw detector to inspect the interior of the rough parts for good appearance products to detect whether there are blisters, pores, white spots, cracks and other defects in the rough parts, mark the defective parts, and return them to the furnace for recasting.
[0134] The operating frequency of the ultrasonic flaw detector is 2.5MHz, and the ambient temperature of the flaw detection is 20-25 degrees Celsius.
[0135] 2. Parts benchmark processing
[0136] 1) place
[0137] Use a vertical lathe to rough-machine the blank, put the blank on ...
Embodiment 3
[0167] A processing method for a high-precision bearing forging, the processing method comprising the following steps:
[0168] 1. Blank inspection
[0169] 1) First, manually screen the rough parts of the outer ring of the bearing, observe whether there are any defects in the appearance of the rough parts, such as fleshy or lacking meat, mark the defective parts, and return them to the furnace for recasting.
[0170] 2) Use an ultrasonic flaw detector to inspect the interior of the rough parts for good appearance products to detect whether there are blisters, pores, white spots, cracks and other defects in the rough parts, mark the defective parts, and return them to the furnace for recasting.
[0171] The operating frequency of the ultrasonic flaw detector is 2.5MHz, and the ambient temperature of the flaw detection is 20-25 degrees Celsius.
[0172] 2. Parts benchmark processing
[0173] 1) place
[0174] Use a vertical lathe to rough-machine the blank, put the blank on ...
PUM
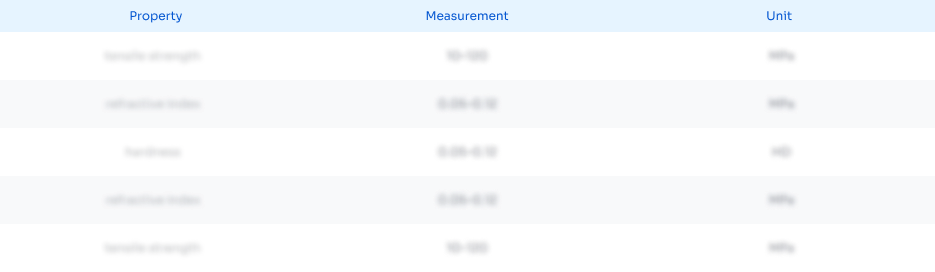
Abstract
Description
Claims
Application Information

- R&D
- Intellectual Property
- Life Sciences
- Materials
- Tech Scout
- Unparalleled Data Quality
- Higher Quality Content
- 60% Fewer Hallucinations
Browse by: Latest US Patents, China's latest patents, Technical Efficacy Thesaurus, Application Domain, Technology Topic, Popular Technical Reports.
© 2025 PatSnap. All rights reserved.Legal|Privacy policy|Modern Slavery Act Transparency Statement|Sitemap|About US| Contact US: help@patsnap.com