Matte single-component room temperature vulcanized silicone rubber and preparation method thereof
A room temperature vulcanization, one-component technology, applied in the field of rubber preparation, can solve problems such as unstable storage, complicated process, and unreliable matte film
- Summary
- Abstract
- Description
- Claims
- Application Information
AI Technical Summary
Problems solved by technology
Method used
Image
Examples
Embodiment 1
[0023] Add 30 parts of α,ω-dihydroxypolydimethylsiloxane with a viscosity of 20Pa.s, 2 parts of polydimethylsiloxane, 60 parts of nano-calcium carbonate, and 1 part of titanium dioxide into the kneader, Stir and dehydrate the base material at a speed of 30r / min, a temperature of 120°C, and a vacuum of -0.09MPa for 2 hours to prepare the base material. When the base material is cooled to 60°C, put the base material into a power mixer and add 3 parts of methyl Trimethoxysilane, 2 parts of a complex of ethyl acetoacetate and tetraisopropyl titanate, 1 part of γ-aminopropyltriethoxysilane and 1 part of vinyltrimethoxysilane, vacuumed to Under -0.09MPa, stir for 50 minutes to discharge the material, and pack it in a 300ml HDPE tube.
Embodiment 2
[0025] Add 70 parts of α,ω-dihydroxy polydimethylsiloxane with a viscosity of 80Pa.s, 2 parts of polydimethylsiloxane, 20 parts of nano-calcium carbonate, and 1 part of titanium dioxide into the kneader, The base material was prepared by stirring and dehydrating for 2 hours at a rotation speed of 30r / min, a temperature of 120°C, and a vacuum of -0.09MPa. When the base material was cooled to 60°C, the base material was poured into a power mixer, and 3.5 parts of methyl Trimethoxysilane, 1.5 parts of a complex of ethyl acetoacetate and tetraisopropyl titanate, 1 part of γ-aminopropyltriethoxysilane and γ-(2,3-glycidoxy) The mixture of propyltrimethoxysilane and 1 part of vinyltriethoxysilane is vacuumed to -0.09MPa, stirred for 50 minutes and discharged, and packed in a 300ml HDPE tube.
Embodiment 3
[0027] 40 parts of α, ω-trimethoxy-terminated polydimethylsiloxane with a viscosity of 20Pa.s, 3 parts of polydimethylsiloxane, 40 parts of nano-calcium carbonate, and 10 parts of fumed white carbon Black, add 2 parts of titanium dioxide into the kneader, stir and dehydrate for 2 hours at a speed of 30r / min, a temperature of 120°C, and a vacuum of -0.09MPa to prepare the base material. When the base material is cooled to 60°C, put the base material into To a power mixer, add 2 parts of methyltrimethoxysilane, 1 part of a complex of ethyl acetoacetate and tetraisopropyl titanate, 0.5 parts of γ-aminopropyltriethoxysilane, 0.5 Part of γ-(2,3-glycidoxy) propyltrimethoxysilane mixture, 1 part of anilinomethyltriethoxysilane, vacuumed to -0.09MPa, stirred for 50 minutes and discharged, Packaged in a 300ml HDPE tube.
PUM
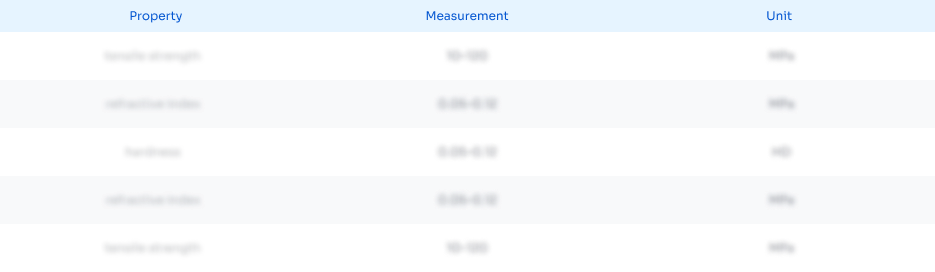
Abstract
Description
Claims
Application Information

- Generate Ideas
- Intellectual Property
- Life Sciences
- Materials
- Tech Scout
- Unparalleled Data Quality
- Higher Quality Content
- 60% Fewer Hallucinations
Browse by: Latest US Patents, China's latest patents, Technical Efficacy Thesaurus, Application Domain, Technology Topic, Popular Technical Reports.
© 2025 PatSnap. All rights reserved.Legal|Privacy policy|Modern Slavery Act Transparency Statement|Sitemap|About US| Contact US: help@patsnap.com