Production process for high-grade heat insulation pipe
A production process and technology of heat-insulated pipes, which are applied in the field of super-heat-insulated pipe production processes, can solve problems such as welding performance, high impact toughness requirements, large energy consumption, and long production cycle, so as to improve comprehensive performance, improve comprehensive performance, The effect of shortening the production cycle
- Summary
- Abstract
- Description
- Claims
- Application Information
AI Technical Summary
Problems solved by technology
Method used
Examples
Embodiment 1
[0051] A high-grade heat insulation pipe production process, the production process includes the following steps:
[0052] Steelmaking production process:
[0053] Step 1: Ladle Preparation
[0054] 1. Purge the breathable bricks to ensure the air permeability of the ladle;
[0055] 2) Clean the ladle so that there is no cold steel at the bottom of the ladle and no residue along the edge of the ladle;
[0056] 3) Use chrome drainage sand and bake it, fill it up and form a protrusion when adding sand;
[0057]Step 2: Converter process
[0058] 1) Loading capacity is 84 tons, end point component control C: 0.135%, P ≤0.012%, temperature: 1625°C;
[0059] 2) Converter tapping, deoxidation alloying, lime top slag addition 400kg / furnace, refining slag 300kg / furnace, aluminum ingot 1.15kg / t, vanadium nitrogen alloy 1.3kg / t, silicon manganese alloy 24 kg / t, silicon Iron 1.5kg / t; guaranteed components for refining C: 0.225%, Si: 0.475%, Mn: 1.53%, P≤0.016%, V: 0.087%, Als: 0.025%...
Embodiment 2
[0090] A high-grade heat insulation pipe production process, the production process includes the following steps:
[0091] Steelmaking production process:
[0092] Step 1: Ladle Preparation
[0093] 1. Purge the breathable bricks to ensure the air permeability of the ladle;
[0094] 2) Clean the ladle so that there is no cold steel at the bottom of the ladle and no residue along the edge of the ladle;
[0095] 3) Use chrome drainage sand and bake it, fill it up and form a protrusion when adding sand;
[0096] Step 2: Converter process
[0097] 1) Loading capacity is 86 tons, end-point component control C: 0.19%, P ≤0.012%, temperature: 1650°C;
[0098] 2) Converter tapping, deoxidation alloying, lime top slag addition 400kg / furnace, refining slag 300kg / furnace, aluminum ingot 1.5kg / t, vanadium-nitrogen alloy 1.3kg / t, silicon-manganese alloy 24 kg / t, silicon Iron 1.5kg / t; guarantee for refining components C: 0.25%, Si: 0.50%, Mn: 1.56%, P≤0.016%, V: 0.099%, Als: 0.040%;
...
Embodiment 3
[0129] A high-grade heat insulation pipe production process, the production process includes the following steps:
[0130] Steelmaking production process:
[0131] Step 1: Ladle Preparation
[0132] 1. Purge the breathable bricks to ensure the air permeability of the ladle;
[0133] 2) Clean the ladle so that there is no cold steel at the bottom of the ladle and no residue along the edge of the ladle;
[0134] 3) Use chrome drainage sand and bake it, fill it up and form a protrusion when adding sand;
[0135] Step 2: Converter process
[0136] 1) Loading capacity is 82 tons, end point component control C: 0.08%, P ≤0.012%, temperature: 1600°C;
[0137] 2) Converter tapping, deoxidation alloying, lime top slag addition 400kg / furnace, refining slag 300kg / furnace, aluminum ingot 0.8kg / t, vanadium nitrogen alloy 1.3kg / t, silicon manganese alloy 24 kg / t, silicon Iron 1.5kg / t; guaranteed components for refining C: 0.20%, Si: 0.45%, Mn: 1.50%, P≤0.016%, V: 0.075%, Als: 0.010%; ...
PUM
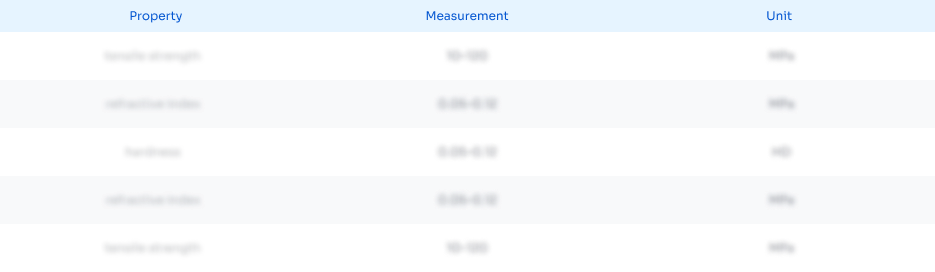
Abstract
Description
Claims
Application Information

- R&D Engineer
- R&D Manager
- IP Professional
- Industry Leading Data Capabilities
- Powerful AI technology
- Patent DNA Extraction
Browse by: Latest US Patents, China's latest patents, Technical Efficacy Thesaurus, Application Domain, Technology Topic, Popular Technical Reports.
© 2024 PatSnap. All rights reserved.Legal|Privacy policy|Modern Slavery Act Transparency Statement|Sitemap|About US| Contact US: help@patsnap.com