Treatment method of high-palladium high-tin high-copper regenerated tin anode slime
A technology of tin anode slime and treatment method, which is applied to the improvement of process efficiency, photography process, instruments, etc., can solve the problems of low comprehensive recovery rate, low recovery rate of precious metal gold, high process operation intensity, etc., and achieve labor intensity of workers Low, easy automatic control, good environmental effect
- Summary
- Abstract
- Description
- Claims
- Application Information
AI Technical Summary
Problems solved by technology
Method used
Image
Examples
Embodiment 1
[0032] Embodiment 1: According to figure 1 Operate as shown.
[0033] The chemical composition of a typical high-palladium, high-tin, high-copper-tin anode slime is shown in Table 1.
[0034] Table 1 Chemical composition of a typical high-palladium, high-tin, high-copper-tin anode slime, unit %
[0035] Cu Ni sn Pb As Sb S Au* Ag* Pd* 5.17 4.93 36.02 6.2 1.29 11.81 2.14 1145.9 59060 693
[0036] Note: *, the unit is g / t
[0037] pre-leaching
[0038] According to the chemical composition of tin anode slime shown in Table 1, when organizing production, the liquid-solid ratio L / S is 4 / 1, and the tin anode slime and sulfuric acid solution are respectively sent to the normal pressure leaching tank, and the normal pressure is continuously pretreated. For leaching, the mass concentration of the sulfuric acid solution is 100g / L, the pre-leaching temperature is 80-85°C, and the residence time is 1.0h.
[0039] pressure oxidation leachin...
PUM
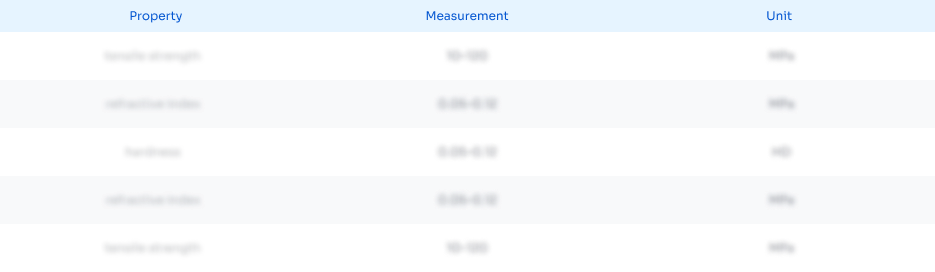
Abstract
Description
Claims
Application Information

- Generate Ideas
- Intellectual Property
- Life Sciences
- Materials
- Tech Scout
- Unparalleled Data Quality
- Higher Quality Content
- 60% Fewer Hallucinations
Browse by: Latest US Patents, China's latest patents, Technical Efficacy Thesaurus, Application Domain, Technology Topic, Popular Technical Reports.
© 2025 PatSnap. All rights reserved.Legal|Privacy policy|Modern Slavery Act Transparency Statement|Sitemap|About US| Contact US: help@patsnap.com