Anti-fracture starch slurry and preparation method thereof
A starch size and anti-cracking technology, which is applied in fiber types, textiles and papermaking, fiber treatment, etc., can solve the problems of not meeting the flexibility requirements of the size film and complicated manufacturing process, and improve the initiation efficiency and size film performance Improvement and flexibility enhancement effect
- Summary
- Abstract
- Description
- Claims
- Application Information
AI Technical Summary
Problems solved by technology
Method used
Image
Examples
preparation example Construction
[0024] The invention provides a kind of preparation method of anti-cracking starch size, comprises the following steps:
[0025] (1) adding water to gelatinize cornstarch after irradiation treatment to obtain gelatinized starch;
[0026] (2) vinyl acetate, acrylic acid and initiator are mixed to carry out polymerization reaction, obtain copolymer;
[0027] (3) adding ammonium persulfate and sodium bisulfite to initiate graft copolymerization after mixing the copolymer and gelatinized starch, and obtaining the anti-cracking starch slurry after neutralization with alkali;
[0028] The steps (1) and (2) are not limited by time sequence.
[0029] In the invention, the cornstarch is irradiated and gelatinized by adding water to obtain the gelatinized starch. In the present invention, the moisture content of the cornstarch is preferably 60 For Co-γ, the irradiation dose is preferably 4-40 kGy, more preferably 20-40 kGy, even more preferably 30-40 kGy. The present invention adopts...
Embodiment 1
[0039] A kind of anti-cracking starch size, its preparation comprises the following steps:
[0040] (1) Take 300g of cornstarch (moisture content 14%) and place 60 Co-γ irradiation field irradiation, the irradiation dose is 4kGy, add water 9 times the weight of the irradiation powder, put it in a glass reactor, protect it with nitrogen, raise the temperature from room temperature to 95°C, and gelatinize for 30 minutes. And keep warm for 30 minutes to obtain gelatinized starch;
[0041] (2) Take 700 g of monomers (550 g of vinyl acetate, 150 g of acrylic acid) and 2 g of dimethyl azobisisobutyrate in a 69° C. water bath for 40 minutes, protect with nitrogen, and stir at a speed of 200 rpm to obtain a copolymer;
[0042] (3) the gelatinized starch of step (1) is cooled to 65 ℃ and the copolymer is mixed uniformly, and then simultaneously start to drip the ammonium sulfate aqueous solution (containing ammonium sulfate 4.5g) that concentration is 10wt.% and concentration is that ...
Embodiment 2
[0044] A kind of anti-cracking starch slurry, has improved irradiation dosage with respect to embodiment 1, and its preparation comprises the following steps:
[0045] (1) Take 300g of cornstarch (moisture content 14%) and place 60 Co-γ irradiation field irradiation, the irradiation dose is 20kGy, add water 9 times the weight of the irradiation powder, put it in a glass reactor, protect it with nitrogen, raise the temperature from room temperature to 95°C, and gelatinize for 30 minutes. And keep warm for 30 minutes to obtain gelatinized starch;
[0046] (2) Take 700 g of monomers (550 g of vinyl acetate, 150 g of acrylic acid) and 2 g of dimethyl azobisisobutyrate in a 69° C. water bath for 40 minutes, protect with nitrogen, and stir at a speed of 200 rpm to obtain a copolymer;
[0047] (3) the gelatinized starch of step (1) is cooled to 65 ℃ and the copolymer is mixed uniformly, and then simultaneously start to drip the ammonium sulfate aqueous solution (containing ammonium ...
PUM
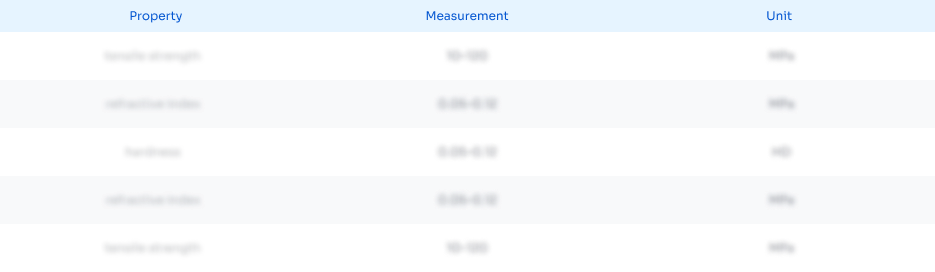
Abstract
Description
Claims
Application Information

- Generate Ideas
- Intellectual Property
- Life Sciences
- Materials
- Tech Scout
- Unparalleled Data Quality
- Higher Quality Content
- 60% Fewer Hallucinations
Browse by: Latest US Patents, China's latest patents, Technical Efficacy Thesaurus, Application Domain, Technology Topic, Popular Technical Reports.
© 2025 PatSnap. All rights reserved.Legal|Privacy policy|Modern Slavery Act Transparency Statement|Sitemap|About US| Contact US: help@patsnap.com