Method of manufacturing clad layer on basis of vibration-assistant ultrahigh-speed laser cladding technology
A laser cladding, ultra-high-speed technology, applied in the direction of coating, metal material coating process, etc.
- Summary
- Abstract
- Description
- Claims
- Application Information
AI Technical Summary
Problems solved by technology
Method used
Image
Examples
Embodiment 1
[0035] see figure 1 , during the ultra-high-speed laser cladding process for 27SiMn steel shaft workpieces, use ultrasonic impact equipment to mechanically impact the cladding layer online, the specific steps are as follows:
[0036] Step 1, put the shaft workpiece 4 into the chuck 3, move the top 6 to tighten the workpiece 4 and clamp the chuck 3; use an angle grinder to remove stains and rust on the surface of the workpiece, and then wipe the surface of the workpiece 4 with alcohol;
[0037] Step 2, select JG-8 iron-based self-fluxing powder, the particle size range of the cladding powder is 20μm~53μm, the sphericity is ≥90%, the preheating temperature is 120°C, the holding time is 1h, and then the powder is sieved with a 200-mesh sieve before loading into the powder feeder;
[0038] Step 3. Adjust the parameters of the ultra-high-speed laser cladding equipment. The laser cladding power is 3KW, and the spot size is Φ2mm; the working distance of the spot from the cladding he...
Embodiment 2
[0046] see figure 2 , during the ultra-high-speed laser cladding process for plate workpieces, use ultrasonic impact equipment to mechanically impact the cladding layer online, the specific steps are as follows:
[0047] Step 1, fix the 45 steel plate workpiece 8 on the working platform 10 through the fixing fixture 9; use an angle grinder to remove stains and rust on the surface of the workpiece, and then wipe the surface of the workpiece 8 with alcohol;
[0048] Step 2: Select Ni30 self-fluxing powder, the particle size range of the cladding powder is 20μm~53μm, the sphericity is ≥90%, the preheating temperature is 120°C, the holding time is 1h, and then the powder is sieved with a 200-mesh sieve and loaded into the powder feeder middle;
[0049] Step 3. Adjust the parameters of the ultra-high-speed laser cladding equipment. The laser cladding power is 1KW-2KW, and the spot size is Φ1mm; the working distance of the spot from the cladding head to the workpiece is 14mm; The...
PUM
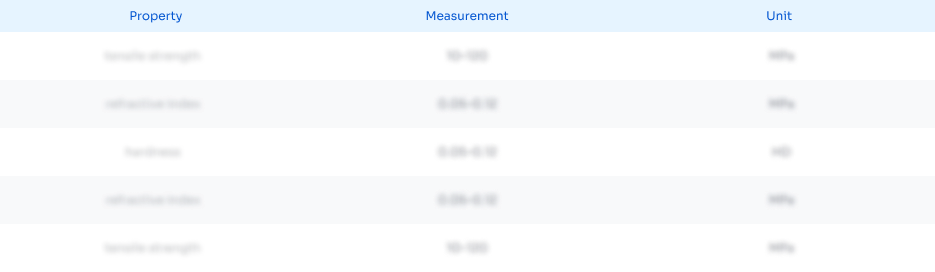
Abstract
Description
Claims
Application Information

- R&D Engineer
- R&D Manager
- IP Professional
- Industry Leading Data Capabilities
- Powerful AI technology
- Patent DNA Extraction
Browse by: Latest US Patents, China's latest patents, Technical Efficacy Thesaurus, Application Domain, Technology Topic, Popular Technical Reports.
© 2024 PatSnap. All rights reserved.Legal|Privacy policy|Modern Slavery Act Transparency Statement|Sitemap|About US| Contact US: help@patsnap.com