Method for carrying out recovery treatment on waste saggar in lithium cobaltate positive electrode material preparation process
A positive electrode material and preparation process technology, which is applied in the field of recycling waste saggers during the preparation of lithium cobaltate positive electrode materials, can solve the problems of comprehensive utilization of waste saggers and difficulty in recycling, etc., and achieve reduced raw material consumption and low price , cost-saving effect
- Summary
- Abstract
- Description
- Claims
- Application Information
AI Technical Summary
Problems solved by technology
Method used
Image
Examples
Embodiment 1
[0154] This embodiment provides a method for recycling waste saggers during the preparation of lithium cobaltate cathode materials, the specific method is:
[0155] (1) Immerse the discarded sagger described in Table 1 in a leaching tank with a molar concentration of 2mol / L of 10L sulfuric acid (obtained by adding acid) for reaction, add 100mL of hydrogen peroxide (additive) to carry out leaching reaction at 30°C, and leaching for 10h Finally, the sagger was taken out, and the purified sagger was put into clear water for soaking. After soaking for 4 hours, the sagger was washed with clear water and used for crushing and screening to prepare refractory powder.
[0156] (2) After repeated leaching of 10 discarded saggers, the leaching solution is firstly separated by filtration, and the filter residue is returned to the leaching tank for deep leaching. After washing, it is discharged as solid waste, and the filtered filtrate is added to the digested / slurried calcium hydroxide. A...
Embodiment 2
[0170] This embodiment provides a method for recycling waste saggers during the preparation of lithium cobaltate cathode materials, the specific method is:
[0171] (1) Immerse the waste sagger used in Example 1 into a leaching tank of 10L sulfuric acid with a molar concentration of 3mol / L for reaction, add 500mL of hydrogen peroxide and carry out leaching reaction at 25°C, take out the sagger after leaching for 10h, and purify the sagger The bowl is soaked in clean water, soaked for 6 hours, rinsed with clean water, and then the sagger is used for crushing and screening to prepare refractory powder.
[0172] (2) After repeated leaching of 20 discarded saggers, the leaching solution was first separated by filtration, and the filter residue was returned to the leaching tank for deep leaching. After washing, it was discharged as solid waste. The filtered filtrate was slowly added to calcium oxide for neutralization, and the pH was controlled at an end point of 3.0, reacted for 3...
Embodiment 3
[0182] This embodiment provides a method for recycling waste saggers during the preparation of lithium cobaltate cathode materials, the specific method is:
[0183] (1) The discarded sagger used in Example 1 is immersed in a leaching tank of 10L sulfuric acid (obtained by adding acid) with a molar concentration of 2.5mol / L for reaction, and 500mL of hydrogen peroxide (additive) is added to carry out leaching reaction at normal temperature, and leaching for 10h Finally, the sagger was taken out, and the purified sagger was put into clear water for soaking. After soaking for 6 hours, the sagger was washed with clear water and used for crushing and screening to prepare refractory powder.
[0184] (2) After repeated leaching of 15 discarded saggers, the leaching solution is firstly separated by filtration, the filter residue is returned to the leaching tank for deep leaching, and after washing is completed, it is discharged as solid waste. And, control the pH end point to be 2.5, fi...
PUM
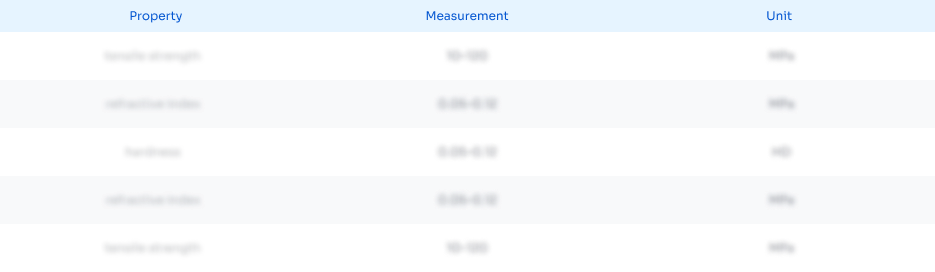
Abstract
Description
Claims
Application Information

- R&D
- Intellectual Property
- Life Sciences
- Materials
- Tech Scout
- Unparalleled Data Quality
- Higher Quality Content
- 60% Fewer Hallucinations
Browse by: Latest US Patents, China's latest patents, Technical Efficacy Thesaurus, Application Domain, Technology Topic, Popular Technical Reports.
© 2025 PatSnap. All rights reserved.Legal|Privacy policy|Modern Slavery Act Transparency Statement|Sitemap|About US| Contact US: help@patsnap.com