Method for selectively separating valuable metal in cobalt-nickel-copper-iron alloy
A valuable metal, cobalt-nickel-copper technology, applied in the field of metallurgy, can solve the problems of unsuitable industrialized continuous production, difficult to achieve large-scale industrialization, strong corrosiveness of the hydrochloric acid system, etc., to achieve clean high-value utilization and product added value. High, breaking through the resource bottleneck effect
- Summary
- Abstract
- Description
- Claims
- Application Information
AI Technical Summary
Problems solved by technology
Method used
Image
Examples
Embodiment 1
[0048] This embodiment includes the following steps:
[0049] (1) Preparation of alloy powder: Add cobalt-nickel-copper-iron alloy into an electric arc furnace to melt at 1300°C, and then conduct atomization to make powder. The nitrogen pressure used is 0.8MPa, and the particle size of the powder is controlled to be ≤100 mesh to obtain alloy powder; Composition by weight percentage (%): Co 5.86, Ni 6.28, Cu 6.86 and Fe 80.12;
[0050] (2) Potential-controlled selective leaching of alloy powder: Add 500g of the alloy powder obtained in step (1) into the 5L, 3.27mol / L dilute sulfuric acid solution in the leaching tank, and the air flow rate is 0.5L / min to control the leaching process The potential is 200~250mV (SCE), the stirring speed is 500r / min, and 733.6g of hydrogen peroxide with a mass fraction of 25% is added through a constant flow pump, and the reaction temperature is kept at 40~60°C. After leaching for 6 hours, solid-liquid separation is carried out and washed. The co...
Embodiment 2
[0055] This embodiment includes the following steps:
[0056] (1) Preparation of alloy powder: add cobalt-nickel-copper-iron alloy into an electric arc furnace to melt at 1500°C, and then conduct atomization to make powder. The nitrogen pressure used is 1.5MPa, and the particle size of the powder is controlled to be ≤100 mesh to obtain alloy powder;
[0057] The composition of the alloy powder is in weight percent (%): Co 14.68, Ni 16.26, Cu 12.46 and Fe 55.32;
[0058] (2) Potential-controlled selective leaching of alloy powder: Add 500g of the alloy powder obtained in step (1) into the 4L, 2.61mol / L dilute sulfuric acid solution in the leaching tank, and the air flow rate is 2.0L / min to control the leaching process The potential is 280~350mV (SCE), the stirring speed is 1000r / min, and 1106.4g of hydrogen peroxide with a mass fraction of 25% is added through a constant flow pump, and the reaction temperature is kept at 60~70°C. After leaching for 4 hours, solid-liquid separat...
Embodiment 3
[0063] This embodiment includes the following steps:
[0064] (1) Preparation of alloy powder: Add cobalt-nickel-copper-iron alloy into an electric arc furnace to melt at 1600°C, and then conduct atomization to make powder. The nitrogen pressure used is 2.5MPa, and the particle size of the powder is controlled to be ≤100 mesh to obtain alloy powder;
[0065] The composition of the alloy powder is calculated by weight percentage (%): Co 19.39, Ni 24.63, Cu 18.82 and Fe 36.68;
[0066] (2) Potential-controlled selective leaching of alloy powder: Add 500g of the alloy powder obtained in step (1) into the 6L, 1.87mol / L dilute sulfuric acid solution in the leaching tank, and the air flow rate is 0.5L / min to control the leaching process The potential is 350~400mV (SCE), the stirring speed is 1500r / min, and 1834g of hydrogen peroxide with a mass fraction of 25% is added through a constant flow pump, and the reaction temperature is kept at 40~60°C. After leaching for 6 hours, solid-li...
PUM
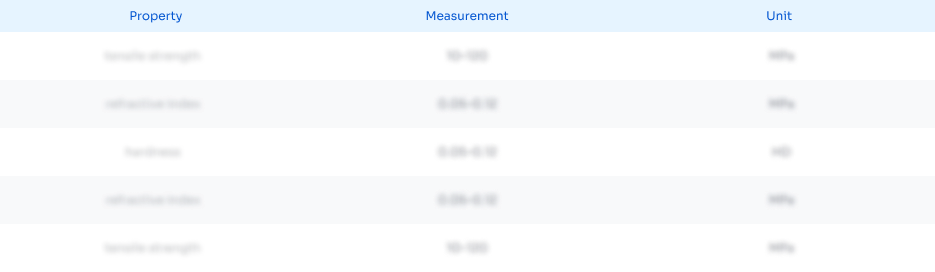
Abstract
Description
Claims
Application Information

- Generate Ideas
- Intellectual Property
- Life Sciences
- Materials
- Tech Scout
- Unparalleled Data Quality
- Higher Quality Content
- 60% Fewer Hallucinations
Browse by: Latest US Patents, China's latest patents, Technical Efficacy Thesaurus, Application Domain, Technology Topic, Popular Technical Reports.
© 2025 PatSnap. All rights reserved.Legal|Privacy policy|Modern Slavery Act Transparency Statement|Sitemap|About US| Contact US: help@patsnap.com