High-temperature strengthening method for structural-functional integrated neutron absorbing material
A technology of absorbing materials and neutrons, which is applied in the field of high-temperature strengthening of neutron absorbing materials with integrated structure and functions, can solve problems such as difficult to meet the use requirements, strength attenuation, etc., and achieve the effects of avoiding early cracking, small stress concentration, and high activity
- Summary
- Abstract
- Description
- Claims
- Application Information
AI Technical Summary
Problems solved by technology
Method used
Image
Examples
Embodiment 1
[0036] 1) Using 6061Al as the base material, Al 2 o 3 For the nano-reinforced phase, the preparation (Al 2 o 3 np+B 4 Cp) / 6061Al composite material, the nanometer Al that content is 1wt.% 2 o 3 , with a content of 10wt.% B 4 C powder, 6061Al powder with a content of 89wt.% was placed in a high-energy ball mill for uniform mixing and ball milling; the ball milling time was 10 hours, and the ball-to-material ratio was 1.5:1;
[0037] 2) The uniformly mixed powder is pressed into a billet by cold isostatic pressing, wherein the cold isostatic pressing pressure is 200Mpa, and the pressure is maintained for 10 minutes;
[0038] 3) The pressed ingot is placed in an aluminum sheath for welding, and the leakage rate after welding is lower than 3×10 -10Pa·m 3 After / s, vacuumize the aluminum sheath at 500°C for degassing, and the vacuum degree reaches 6×10 -4 At Pa, the aluminum sheath is sealed and welded, and the billet is sealed and welded in the aluminum sheath;
[0039] ...
Embodiment 2
[0045] Example 2 is basically the same as Example 1, except that the forming method is hot forging, the temperature of hot forging is 580°C, the pressure is 50MPa, and the holding time is 15min. The materials used are as follows:
[0046] Using 1060Al as the base material, Y 2 o 3 For the nano-reinforced phase, the preparation (Y 2 o 3np +B 4 C p ) / 1060Al composite material, where Y 2 o 3 The content is 2wt.%, B 4 The C content is 15wt.%, and the 1060Al content is 83wt.%.
Embodiment 3
[0050] Example 3 is basically the same as Example 1, except that the molding method is hot extrusion molding, the temperature of hot extrusion molding is 530° C., the pressure is 100 MPa, and the holding time is 5 minutes. The materials used are as follows:
[0051] Using 7075Al as the matrix material, ZrO 2 For the nano-reinforced phase, the preparation (ZrO 2 np+B 4 Cp) / 7075Al composite material, wherein, ZrO 2 The content is 3wt.%, B 4 The C content is 10wt.%, and the 7075Al content is 87wt.%.
PUM
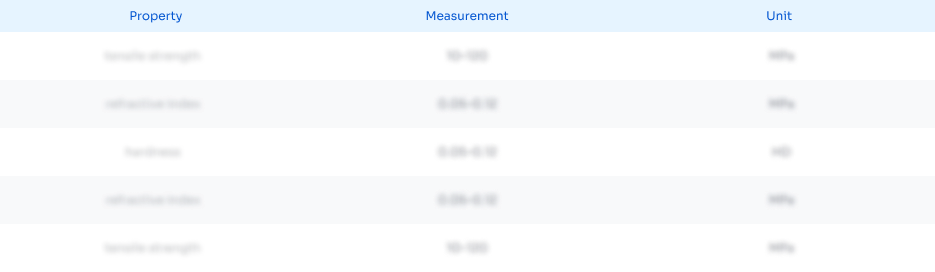
Abstract
Description
Claims
Application Information

- R&D Engineer
- R&D Manager
- IP Professional
- Industry Leading Data Capabilities
- Powerful AI technology
- Patent DNA Extraction
Browse by: Latest US Patents, China's latest patents, Technical Efficacy Thesaurus, Application Domain, Technology Topic, Popular Technical Reports.
© 2024 PatSnap. All rights reserved.Legal|Privacy policy|Modern Slavery Act Transparency Statement|Sitemap|About US| Contact US: help@patsnap.com