Graphene ceramic material and preparation method thereof
A ceramic material and graphene technology, applied in the field of graphene ceramic materials and their preparation, can solve the problems of low thermal conductivity and high electrical resistivity
- Summary
- Abstract
- Description
- Claims
- Application Information
AI Technical Summary
Problems solved by technology
Method used
Image
Examples
preparation example Construction
[0028] The present invention also provides a preparation method of the graphene ceramic material described in the above technical scheme, comprising the following steps:
[0029] Mixing sintering aids, graphene, zinc oxide, aluminum oxide, zirconium oxide and water and drying to obtain graphene ceramic powder;
[0030] The graphene ceramic powder is sequentially pressed into sheets and sintered in a nitrogen atmosphere to obtain a graphene ceramic material.
[0031] In the invention, the sintering aid, graphene, zinc oxide, aluminum oxide, zirconium oxide and water are mixed and then dried to obtain graphene ceramic powder.
[0032] In the present invention, the mixing is preferably ball milling, the time of ball milling is preferably 3-4 hours, and the rotation speed is preferably 440-480 r / min, more preferably 455-465 r / min.
[0033] In the present invention, the drying temperature is preferably 120-180°C, more preferably 140-160°C, and the drying time is preferably 13-16 h...
Embodiment 1
[0040] Weigh 3g of calcium oxide, 0.9g of magnesium oxide, and 6.1g of silicon oxide into a ball mill jar, add 50mL of deionized water, put it into the ball mill, set the speed at 400r / min, after 4 hours, turn off the ball mill, and put the ball mill jar Pour the mixed suspension in the tray into the tray, and clean the ball mill jar several times with deionized water and pour into the tray, and put the tray into an oven at 120°C for 15 hours to dry.
[0041] Weigh 4.35g of sintering aid powder, 3.25g of graphene, 0.56g of zinc oxide, 14.03g of alumina and 2.81g of zirconia into a ball mill jar, add 50mL of deionized water, put the ball mill jar into the ball mill, and set the speed to After 4 hours, pour the mixed suspension in the ball mill jar into the tray, wash the ball mill jar several times with deionized water, and put the tray in an oven at 120°C for 15 hours to dry.
[0042] Weigh 5g of the mixed powder and put it into a tablet press for 5 minutes under a pressure of...
Embodiment 2
[0044] Weigh 3g of calcium oxide, 0.9g of magnesium oxide, and 6.1g of silicon oxide into a ball mill jar, add 50mL of deionized water, put it into the ball mill, set the speed at 400r / min, after 4 hours, turn off the ball mill, and put the ball mill jar Pour the mixed suspension in the tray into the tray, and clean the ball mill jar several times with deionized water and pour into the tray, and put the tray into an oven at 120°C for 15 hours to dry.
[0045] Weigh 4.62g of sintering aid powder, 2.25g of graphene, 0.60g of zinc oxide, 14.89g of alumina and 2.63g of zirconia into a ball mill jar, add 50mL of deionized water, put the ball mill jar into the ball mill, and set the speed to After 4 hours, pour the mixed suspension in the ball mill jar into the tray, wash the ball mill jar several times with deionized water, and put the tray in an oven at 120°C for 15 hours to dry.
[0046] Weigh 5g of the mixed powder and put it into a tablet press and press it under a pressure of 9M...
PUM
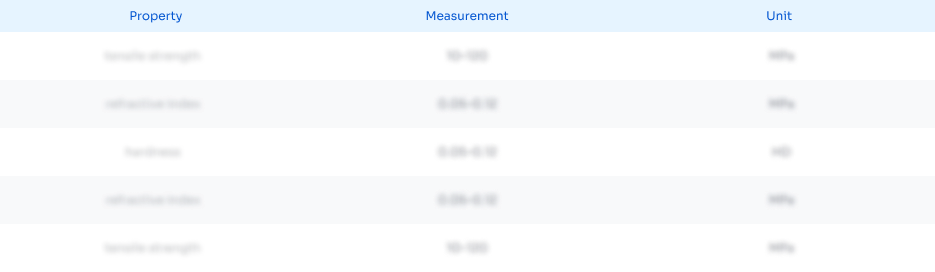
Abstract
Description
Claims
Application Information

- R&D
- Intellectual Property
- Life Sciences
- Materials
- Tech Scout
- Unparalleled Data Quality
- Higher Quality Content
- 60% Fewer Hallucinations
Browse by: Latest US Patents, China's latest patents, Technical Efficacy Thesaurus, Application Domain, Technology Topic, Popular Technical Reports.
© 2025 PatSnap. All rights reserved.Legal|Privacy policy|Modern Slavery Act Transparency Statement|Sitemap|About US| Contact US: help@patsnap.com