Method for preparing ozone catalyst by step-type gradient heating calcining method and application thereof
A gradient heating, stepped technology, applied in chemical instruments and methods, metal/metal oxide/metal hydroxide catalysts, catalyst activation/preparation, etc., to achieve excellent catalytic effect, improve contact, and improve the effect of catalyst activity
- Summary
- Abstract
- Description
- Claims
- Application Information
AI Technical Summary
Problems solved by technology
Method used
Image
Examples
Embodiment 1
[0043] The aluminum-based precursor materials used in this embodiment are: aluminum isopropoxide and anhydrous glucose.
[0044] Dissolve 14.4g of aluminum isopropoxide in 100mL of deionized water, add 5g of anhydrous glucose, and stir in a stirrer at a speed of 400r / min for 6 hours at 35°C to make it completely uniform; The material was dried in an oven at 105°C to constant weight, and then taken out for use;
[0045] Put the dried material in a muffle furnace, in the air atmosphere, first raise the temperature to 90°C at 5°C / min, keep it for 1h, then raise the temperature to 200°C at 3°C / min, keep it for 2h, and then , the temperature was raised to 550°C at 3°C / min, kept at 4h, and cooled to room temperature at 2°C / min. The obtained catalyst was washed with deionized water three times to remove excess metal ions and their oxide. The washed material was dried in an oven at 105°C, and placed in a drying oven for later use. The obtained ozone catalyst is denoted as Y-Al-1. ...
Embodiment 2
[0054] The aluminum-based precursor material used in this embodiment is: aluminum nitrate.
[0055] Weigh 7.5g of aluminum nitrate nonahydrate and place it in a 250mL beaker, add 60mL of deionized water to dissolve, stir at 350r / min for 6h at room temperature, dry the evenly stirred material in an oven at 105°C to constant weight, and take it out for use;
[0056] Put the dried material in a muffle furnace, first raise the temperature to 90°C at 5°C / min, keep it for 1h, then raise the temperature to 200°C at 3°C / min, keep it for 2h, and then raise it at 3°C / min The temperature was raised to 550°C for 4 hours, and the temperature was lowered to room temperature at 2°C / min. The obtained catalyst was washed with deionized water for 5 times to remove excess metal ions and their oxides on the surface of the catalyst particles. The washed material was dried in an oven at 110°C, and placed in a drying oven for later use. The obtained ozone catalyst is denoted as X-Al-1.
Embodiment 3
[0064] The aluminum-based precursor material used in this embodiment is: alumina particles; the active component is: copper nitrate trihydrate.
[0065] Take a commercially available alumina particle catalyst with a particle size of 2 to 4 mm, grind the particles into fine particles of 30 to 60 mesh with a grinder, weigh 30 g of the catalyst, add 6.42 g of copper nitrate trihydrate, fully stir until uniform, and place the supported catalyst on the Dry in an oven at 110°C, then take out the material and place it in a ceramic crucible, place it in a muffle furnace, first raise the temperature to 90°C at 5°C / min, keep it for 1 hour, and then raise the temperature to 200°C at 3°C / min ℃, keep warm for 2h, further, heat up to 550°C at 3°C / min, keep warm for 4h, cool down to room temperature at 2°C / min, and wash the prepared material 4 times with deionized water to remove catalyst particles Excess metal ions and their oxides on the surface. The washed material was dried in an oven a...
PUM
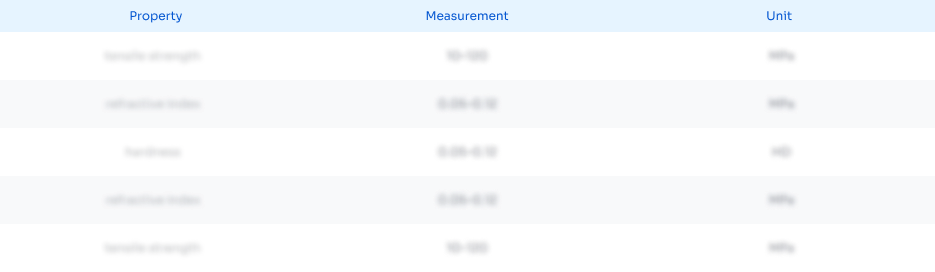
Abstract
Description
Claims
Application Information

- Generate Ideas
- Intellectual Property
- Life Sciences
- Materials
- Tech Scout
- Unparalleled Data Quality
- Higher Quality Content
- 60% Fewer Hallucinations
Browse by: Latest US Patents, China's latest patents, Technical Efficacy Thesaurus, Application Domain, Technology Topic, Popular Technical Reports.
© 2025 PatSnap. All rights reserved.Legal|Privacy policy|Modern Slavery Act Transparency Statement|Sitemap|About US| Contact US: help@patsnap.com