Catalytic cracking method for high nitrogen raw material
A catalytic cracking, high nitrogen raw material technology, applied in catalytic cracking, cracking, petroleum industry and other directions, can solve problems such as increase in coke yield, achieve the effect of improving gasoline octane number, optimizing product distribution, and improving nitrogen resistance performance
- Summary
- Abstract
- Description
- Claims
- Application Information
AI Technical Summary
Problems solved by technology
Method used
Image
Examples
Embodiment approach
[0043] One embodiment, the preparation step of the boron-modified phosphorus-containing Y molecular sieve comprises: introducing phosphorus-containing molecular sieve into a boron-containing compound, followed by drying and roasting; wherein, the boron-containing compound is selected from boron oxide, boric acid, At least one of metaboric acid and water-soluble borate, preferably boric acid. The phosphorus-containing Y molecular sieve can be prepared by conventional methods in the art, and the preparation process generally includes steps such as ammonium exchange, phosphorus modification, and roasting treatment. Specifically, the preparation process may include:
[0044] (i) The crystallized Y molecular sieve is exchanged with ammonium salt for 0.3-1 hour in the range of room temperature to 100° C. and then filtered; the ammonium salt can be a commonly used inorganic ammonium salt, which can be selected from ammonium chloride, ammonium sulfate or at least one of ammonium nitr...
Embodiment 1
[0064] This example is used to illustrate the preparation method of the boron-modified phosphorus-containing Y molecular sieve catalyst provided by the present invention.
[0065] (1) Preparation of phosphorus-containing Y molecular sieve
[0066] 10 g NH 4 Cl is dissolved in 2 kilograms of water, and 200 grams (dry basis) of NaY molecular sieves (industrial product of Qilu Catalyst Factory, unit cell constant is 2.447-2.450 nanometers, SiO 2 / Al2 o 3 =3.2, rare earth content RE 2 o 3 =2.8% by weight), exchange and wash at 90°C for 30 minutes, control Na 2 The O content is lower than 0.3% by weight, and the filter cake is obtained by filtration. The resulting filter cake was dried, calcined at 350°C for 2 hours, and then heated to 600°C for 2.5 hours to remove the templating agent. The molecular sieve 100 grams (dry basis) that removes template agent is added with water and is mixed with the molecular sieve slurry that solid content is 40% by weight, then 9 grams of H 3...
Embodiment 2
[0073] This example is used to illustrate the effect of the catalytic cracking catalyst A provided by the present invention in processing high-nitrogen feedstock.
[0074] According to this embodiment figure 1 The flow shown is tested on a riser reactor medium-scale unit. The high-nitrogen raw material used in the test is a mixed raw material of 80% by weight of coker gas oil and 20% by weight of straight-run gas oil, and its properties are listed in Table 2. The high-nitrogen raw material is preheated to 320°C, atomized uniformly by water vapor, and then passed into the riser reactor, where it contacts with the high-temperature regenerated catalyst and undergoes catalytic cracking reaction. After the reaction oil gas is discharged from the riser reactor, it passes through the cyclone in the dilute phase of the settler After the separator is separated, it enters the subsequent separation system. The spent catalyst with charcoal enters the stripping section, and the stripped ...
PUM
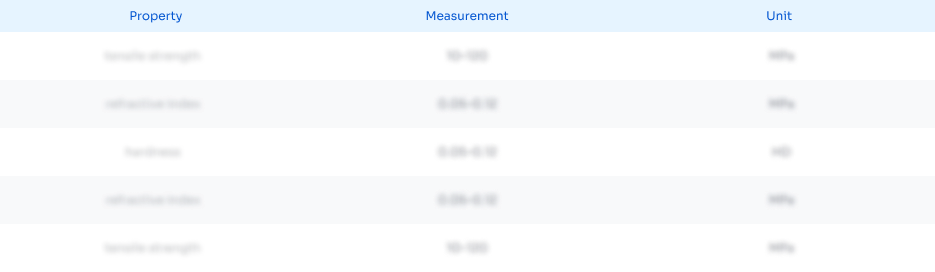
Abstract
Description
Claims
Application Information

- R&D
- Intellectual Property
- Life Sciences
- Materials
- Tech Scout
- Unparalleled Data Quality
- Higher Quality Content
- 60% Fewer Hallucinations
Browse by: Latest US Patents, China's latest patents, Technical Efficacy Thesaurus, Application Domain, Technology Topic, Popular Technical Reports.
© 2025 PatSnap. All rights reserved.Legal|Privacy policy|Modern Slavery Act Transparency Statement|Sitemap|About US| Contact US: help@patsnap.com