Shock absorber front fork tube surface treatment method
A surface treatment and shock absorber technology, which is applied in the direction of metal material coating process, coating, solid diffusion coating, etc., can solve the problems of easy peeling of chrome-plated surface and poor corrosion resistance of shock absorber front fork cylinder surface, etc., to achieve Improve hardness and corrosion resistance, improve fatigue resistance, and lower temperature
- Summary
- Abstract
- Description
- Claims
- Application Information
AI Technical Summary
Problems solved by technology
Method used
Examples
Embodiment 1
[0072] This embodiment provides a surface treatment method for a front fork cylinder of a shock absorber, comprising the following steps:
[0073] (1) Infiltrate the surface of the front fork tube of the shock absorber with carbon nitrogen lanthanum yttrium ion infiltration agent, the temperature of infiltration treatment is 450°C, and the infiltration time is 100min;
[0074] (2) Activate the front fork tube of the shock absorber after the treatment in step (1) with lanthanum yttrium activator, the temperature of activation is 420°C, and the activation time is 50min;
[0075] (3) The shock absorber front fork cylinder activated in step (2) is subjected to oxygen ion infiltration treatment for the first time with an oxygen ion infiltration agent, the temperature of the oxygen ion infiltration treatment is 380° C., and the time is 30 minutes;
[0076] (4) Cool and clean the front fork tube of the shock absorber treated in step (3) and then polish it, and perform the second oxyg...
Embodiment 2
[0079] This embodiment provides a surface treatment method for a front fork cylinder of a shock absorber, comprising the following steps:
[0080] (1) Infiltrate the surface of the front fork tube of the shock absorber with carbon nitrogen lanthanum yttrium ion infiltration agent, the temperature of the infiltration treatment is 470°C, and the infiltration time is 160min;
[0081] (2) Activate the front fork tube of the shock absorber after the treatment in step (1) with a lanthanum yttrium activation agent, the activation temperature is 450° C., and the activation time is 70 min;
[0082] (3) The shock absorber front fork cylinder activated in step (2) is subjected to oxygen ion infiltration treatment for the first time with an oxygen ion infiltration agent, the temperature of the oxygen ion infiltration treatment is 410° C., and the time is 40 minutes;
[0083] (4) Cool and clean the front fork tube of the shock absorber after the treatment in step (3) and polish it, and car...
Embodiment 3
[0086] This embodiment provides a surface treatment method for a front fork cylinder of a shock absorber, comprising the following steps:
[0087] (1) Infiltrate the surface of the front fork tube of the shock absorber with carbon, nitrogen, lanthanum and yttrium ion infiltration agent, the temperature of the infiltration treatment is 460°C, and the infiltration time is 130 minutes;
[0088] (2) Activate the front fork tube of the shock absorber after the treatment in step (1) with lanthanum yttrium activator, the temperature of activation is 430°C, and the activation time is 60min;
[0089] (3) The shock absorber front fork cylinder activated in step (2) is subjected to oxygen ion infiltration treatment for the first time with an oxygen ion infiltration agent, the temperature of the oxygen ion infiltration treatment is 390° C., and the time is 35 minutes;
[0090] (4) Cool and clean the front fork tube of the shock absorber after the treatment in step (3) and then polish it, ...
PUM
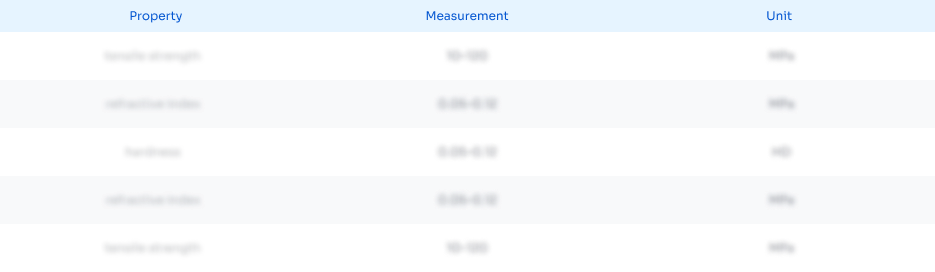
Abstract
Description
Claims
Application Information

- Generate Ideas
- Intellectual Property
- Life Sciences
- Materials
- Tech Scout
- Unparalleled Data Quality
- Higher Quality Content
- 60% Fewer Hallucinations
Browse by: Latest US Patents, China's latest patents, Technical Efficacy Thesaurus, Application Domain, Technology Topic, Popular Technical Reports.
© 2025 PatSnap. All rights reserved.Legal|Privacy policy|Modern Slavery Act Transparency Statement|Sitemap|About US| Contact US: help@patsnap.com