Casting device, ingot casting system and ingot casting method
A technology for casting ingots and casting machines, applied in ingot workshops, casting workshops, casting equipment, etc., can solve the problems of high labor intensity, large labor capacity, and large unit footprint, and achieve low labor intensity and labor capacity The effect of less, small footprint
- Summary
- Abstract
- Description
- Claims
- Application Information
AI Technical Summary
Problems solved by technology
Method used
Image
Examples
Embodiment Construction
[0043] The present invention will be described in detail below in conjunction with examples. It should be noted that, in the case of no conflict, the embodiments of the present invention and the features in the embodiments can be combined with each other. For the convenience of description, if the words "up", "down", "left" and "right" appear in the following, it only means that the directions of up, down, left and right are consistent with the drawings themselves, and do not limit the structure.
[0044] Such as figure 2 As shown, a casting device includes a first frame 43 and a first bucket 41 with an open top. The bottom of the first bucket 41 is provided with a hinged seat and a casting nozzle 411 communicated with the first bucket. The hinged seat is connected with the first bucket. The first frame is hinged, and a mold for forming is provided below the casting nozzle 411; a driving mechanism 42 is also included, the lower end of the driving mechanism is hinged with the...
PUM
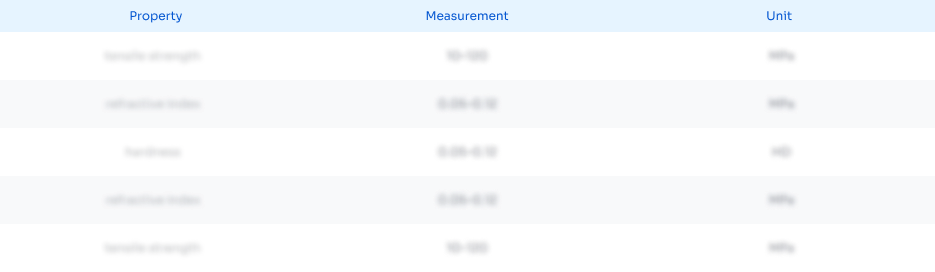
Abstract
Description
Claims
Application Information

- R&D
- Intellectual Property
- Life Sciences
- Materials
- Tech Scout
- Unparalleled Data Quality
- Higher Quality Content
- 60% Fewer Hallucinations
Browse by: Latest US Patents, China's latest patents, Technical Efficacy Thesaurus, Application Domain, Technology Topic, Popular Technical Reports.
© 2025 PatSnap. All rights reserved.Legal|Privacy policy|Modern Slavery Act Transparency Statement|Sitemap|About US| Contact US: help@patsnap.com