Preparation method of fiber-shaped carbon nitride
A technology of carbon nitride and carbon nitride, which is applied in the field of photocatalytic material preparation, can solve the problems of small specific surface area, fast electron-hole recombination, easy agglomeration, etc., achieve good dispersion, strong experimental operability, overcome easy reunion effect
- Summary
- Abstract
- Description
- Claims
- Application Information
AI Technical Summary
Problems solved by technology
Method used
Image
Examples
preparation example Construction
[0026] The preparation method of a fibrous carbon nitride of the present invention comprises the steps of directly calcining the nitrogen-carbon precursor to obtain bulk carbon nitride, and then mixing the bulk carbon nitride with a saturated solution of soluble salt, stirring and heating until evaporated to dryness, and obtaining A solid mixture of soluble salt and carbon nitride powder. Finally, the obtained solid mixture is calcined, washed and dried to obtain fibrous carbon nitride.
[0027] Specifically follow the steps below:
[0028] Step 1, preparation of bulk carbon nitride:
[0029] Weigh a certain amount of carbon-nitrogen precursor dipolycyanamide into a corundum crucible, calcinate in a muffle furnace at 550°C-650°C for 1-3 hours, and heat up at a rate of 0.1-2°C / min to obtain bulk carbon nitride. Grinding with a mortar to obtain carbon nitride powder with uniform size distribution;
[0030] Step 2, preparation of bulk carbon nitride and soluble salt solid mixtu...
Embodiment 1
[0037] Step 1, preparation of bulk carbon nitride
[0038] Weigh 15g of dipolycyanamide into a corundum crucible, calcinate in a muffle furnace at 550°C for 2h, and the heating rate is 0.5°C / min to obtain bulk phase carbon nitride; then grind it with a mortar to obtain nitrogen with uniform size distribution. Carbonized powder;
[0039] Step 2, preparation of bulk carbon nitride and soluble salt solid mixture:
[0040] Mix the carbon nitride powder obtained in step 1 and the saturated sodium chloride solution uniformly at a mass volume ratio of 0.1 g / mL; then stir at 750 r / min on a digital temperature-controlled magnetic stirrer, and heat at 150°C until evaporated to dryness , and then dried in an oven at 50°C for 24 hours to obtain a solid mixture of sodium chloride and carbon nitride powder;
[0041] Step 3, preparation of fibrous carbon nitride:
[0042] After grinding the solid mixture of the soluble salt and carbon nitride powder obtained in step 2, weigh 5g and put it...
Embodiment 2
[0045] Step 1, preparation of bulk carbon nitride
[0046] Weigh 20g of dicyandiamide into a corundum crucible, calcinate in a muffle furnace at 600°C for 2h, and the heating rate is 1°C / min to obtain bulk phase carbon nitride; then grind it with a mortar to obtain nitrogen with uniform size distribution. Carbonized powder;
[0047] Step 2, preparation of bulk carbon nitride and soluble salt solid mixture:
[0048]Mix the carbon nitride powder obtained in step 1 and saturated potassium bromide solution uniformly at a mass volume ratio of 0.2 g / mL; then stir at 500 r / min on a digital display temperature-controlled magnetic stirrer, and heat at 100°C until evaporated to dryness , and then dried in an oven at 50°C for 10 hours to obtain a solid mixture of potassium bromide and carbon nitride powder;
[0049] Step 3, preparation of fibrous carbon nitride:
[0050] Grind the solid mixture of potassium bromide and carbon nitride powder obtained in step 2 evenly, weigh 3g, put it ...
PUM
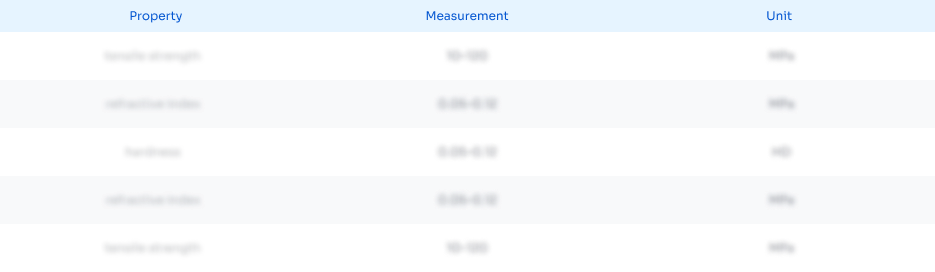
Abstract
Description
Claims
Application Information

- Generate Ideas
- Intellectual Property
- Life Sciences
- Materials
- Tech Scout
- Unparalleled Data Quality
- Higher Quality Content
- 60% Fewer Hallucinations
Browse by: Latest US Patents, China's latest patents, Technical Efficacy Thesaurus, Application Domain, Technology Topic, Popular Technical Reports.
© 2025 PatSnap. All rights reserved.Legal|Privacy policy|Modern Slavery Act Transparency Statement|Sitemap|About US| Contact US: help@patsnap.com