Polyester peach skin imitation finishing technology for terylene and regenerated cellulose fiber interweaved fabric
A technology of regenerated cellulose and imitation peach skin velvet, applied in the direction of fiber processing, fiber type, plant fiber, etc., can solve problems such as affecting the success rate and production rate of products, high requirements for equipment and personnel operation, and increasing production costs, etc. Achieve the effect of improving operational safety, reducing equipment corrosion, and enhancing style
- Summary
- Abstract
- Description
- Claims
- Application Information
AI Technical Summary
Problems solved by technology
Method used
Examples
Embodiment 1
[0025] A kind of imitation jeanette finishing process of polyester and regenerated cellulose fiber interwoven fabric, described polyester and regenerated cellulose fiber interwoven fabric is 40S modal and 50D polyester knitted double-sided bird's-eye cloth, specifically comprises the following steps:
[0026] S1. Fiber-opening one-bath dyeing polyester components: Longsheng Disperse Blue ACE 0.013%, Anoklon Disperse Orange PUD-SD 0.35%, Anoklon Disperse Crimson PUD-SD 0.9%, fiber opener TF- 1051 5g / L, dyeing same bath degreasing agent TF-115D 2.0g / L, polyester leveling agent TF-212 0.5g / L, add water to make working solution and add to overflow dyeing machine, knit double-sided 40S Modal and 50D polyester Put the bird's eye cloth into the working fluid. Raise the temperature to 85°C at a rate of 3.0°C / min, then raise the temperature to 110°C at a rate of 1°C / min, and then raise the temperature to 130°C at a rate of 1.2°C / min, and keep it warm for 60 minutes for fiber-opening an...
Embodiment 2
[0031] A process for imitating jeanette finishing of polyester and regenerated cellulose fiber interwoven fabrics, wherein the polyester and regenerated cellulose fiber interwoven fabrics are 32S viscose in weft direction and 50D polyester woven fabric in warp direction, specifically comprising the following steps:
[0032]S1. Fiber-opening one-bath dyeing and polyester components: Anoklon disperse navy blue ERD 0.5%, Anoklon disperse yellow brown DRDW 0.48%, Anoklon disperse wine red DRDW 0.12%, fiber opener TF- 1051 4g / L, dyeing same bath degreasing agent TF-115D 1.0g / L, polyester leveling agent TF-212A 1.0g / L, add water to make working solution and add to overflow dyeing machine, mix weft 32S viscose with warp 50D polyester woven fabric into the working fluid. Raise the temperature to 85°C at a rate of 2.0°C / min, then raise the temperature to 110°C at a rate of 0.8°C / min, and then raise the temperature to 130°C at a rate of 1.0°C / min, and keep it warm for 60 minutes to carr...
Embodiment 3
[0037] A process for imitating jeanette finishing of polyester and regenerated cellulose fiber interwoven fabrics, wherein the polyester and regenerated cellulose fiber interwoven fabrics are 75D cupro and 50D polyester filament interwoven fabrics, specifically comprising the following steps:
[0038] S1. Fiber-opening one-bath dyeing polyester component: Anoklon disperse navy blue PUD 0.75%, Anoklon disperse orange PUD-SD 0.15%, Anoklon disperse deep red PUD-SD 0.06%, open fiber TF-1051 6g / L, TF-115D 1.5g / L dyeing same-bath degreasing agent, TF-212 0.5g / L polyester leveling agent, add water to make working solution, add 75D copper ammonia and 50D Put the polyester filament interwoven fabric into the working solution. Raise the temperature to 90°C at a rate of 2.5°C / min, then raise the temperature to 110°C at a rate of 1.0°C / min, and then raise the temperature to 130°C at a rate of 1.2°C / min, and keep it warm for 60 minutes to carry out fiber-opening and one-bath dyeing and wa...
PUM
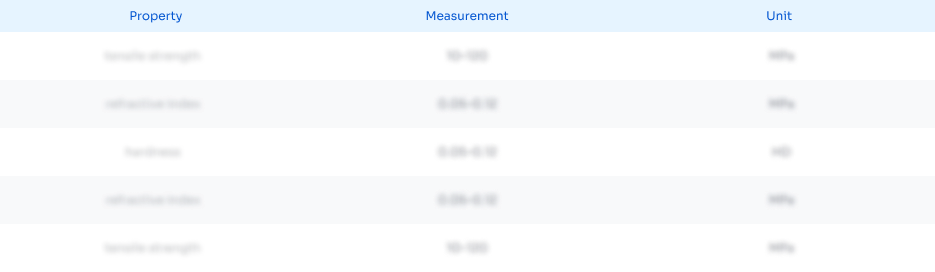
Abstract
Description
Claims
Application Information

- R&D
- Intellectual Property
- Life Sciences
- Materials
- Tech Scout
- Unparalleled Data Quality
- Higher Quality Content
- 60% Fewer Hallucinations
Browse by: Latest US Patents, China's latest patents, Technical Efficacy Thesaurus, Application Domain, Technology Topic, Popular Technical Reports.
© 2025 PatSnap. All rights reserved.Legal|Privacy policy|Modern Slavery Act Transparency Statement|Sitemap|About US| Contact US: help@patsnap.com