Wear-resistant and high-hardness ceramic product and preparation method thereof
A high-hardness technology for ceramic products, applied in the field of ceramics, can solve the problems affecting the aesthetic use of ceramic products, insufficient wear resistance and compressive strength, and easily damaged products, etc., to achieve shortened firing time, high viscosity, and good chemical stability. Effect
- Summary
- Abstract
- Description
- Claims
- Application Information
AI Technical Summary
Problems solved by technology
Method used
Image
Examples
Embodiment 1
[0026] A method for preparing a wear-resistant high-hardness ceramic product, comprising the following steps:
[0027] S1. Take the green body raw materials according to the following parts by weight: 45 parts of kaolin, 5 parts of zirconia, 18 parts of bentonite, 15 parts of waste porcelain slag, 15 parts of silicon nitride, 17 parts of potassium feldspar, and 8 parts of albite;
[0028] S2. Mix the green body raw materials, and then carry out wet ball milling on the mixed green body raw materials. The ball milling medium is agate balls. The weight ratio of green body raw materials: balls: water is 1:1:0.5, and ball milling at a speed of 200r / min After 10 hours, pass through a 100-mesh sieve after ball milling to obtain green body slurry;
[0029] S3. Press and filter the green body slurry into a mud block through a filter press, and then pass the mud block through a mud refining machine to prepare a billet with a mass moisture content of about 20%; and then use a rolling for...
Embodiment 2
[0037] A method for preparing a wear-resistant high-hardness ceramic product, comprising the following steps:
[0038] S1. Take the body raw materials according to the following parts by weight: 48 parts of kaolin, 9 parts of zirconia, 16 parts of bentonite, 17 parts of waste porcelain slag, 12 parts of silicon nitride, 21 parts of potassium feldspar, and 10 parts of albite;
[0039] S2. Mix the green body raw materials, and then carry out wet ball milling on the mixed green body raw materials. The ball milling medium is agate balls. The weight ratio of green body raw materials: balls: water is 1:2:1, and ball milling at a speed of 220r / min After 12 hours, pass through a 120-mesh sieve after ball milling to obtain green body slurry;
[0040] S3. Press and filter the green body slurry into a mud block through a filter press, and pass the mud block through a mud refining machine to prepare a billet with a mass moisture content of about 22%; and then use a rolling forming machine...
Embodiment 3
[0048] A method for preparing a wear-resistant high-hardness ceramic product, comprising the following steps:
[0049] S1. Take the green body raw materials according to the following parts by weight: 50 parts of kaolin, 8 parts of zirconia, 15 parts of bentonite, 20 parts of waste porcelain slag, 13 parts of silicon nitride, 20 parts of potassium feldspar, and 12 parts of albite;
[0050] S2. Mix the green body raw materials, and then perform wet ball milling on the mixed green body raw materials. The ball milling medium is agate balls. The weight ratio of green body raw materials: balls: water is 1:2:1, and ball milling at a speed of 230r / min After 12 hours, pass through a 150-mesh sieve after ball milling to obtain green body slurry;
[0051] S3. Press and filter the green body slurry into a mud block through a filter press, and then pass the mud block through a mud refining machine to prepare a billet with a mass moisture content of about 20%; and then use a rolling formin...
PUM
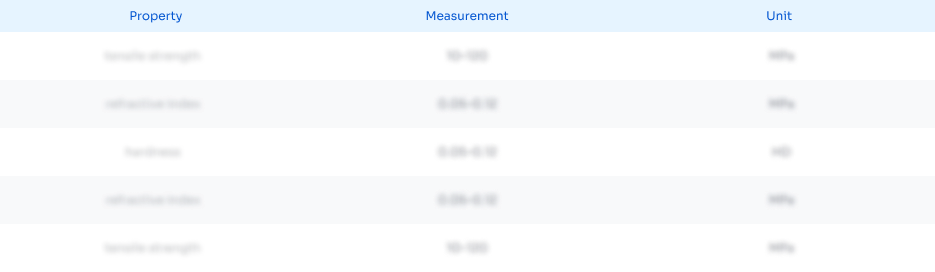
Abstract
Description
Claims
Application Information

- R&D
- Intellectual Property
- Life Sciences
- Materials
- Tech Scout
- Unparalleled Data Quality
- Higher Quality Content
- 60% Fewer Hallucinations
Browse by: Latest US Patents, China's latest patents, Technical Efficacy Thesaurus, Application Domain, Technology Topic, Popular Technical Reports.
© 2025 PatSnap. All rights reserved.Legal|Privacy policy|Modern Slavery Act Transparency Statement|Sitemap|About US| Contact US: help@patsnap.com