Method for preparing nickel-cobalt-phosphorus integrated electrode material having core-shell structure
A core-shell structure and electrode material technology, applied in the field of materials science, can solve the problems of unsatisfactory cycle performance of nickel-cobalt phosphide and limit the application of nickel-cobalt phosphide, so as to reduce electron transfer resistance, improve cycle performance, and increase utilization rate Effect
- Summary
- Abstract
- Description
- Claims
- Application Information
AI Technical Summary
Problems solved by technology
Method used
Image
Examples
Embodiment 1
[0027] (1) Take a carbon cloth with a size of 1 cm × 2 cm and put it in dilute hydrochloric acid, acetone, ethanol and deionized water for ultrasonic cleaning, and finally dry it in a vacuum oven at 60 ° C for 3 h for later use. The concentration of dilute hydrochloric acid is 3M.
[0028] (2) Get 1 mmol of nickel nitrate hexahydrate, 1 mmol of cobalt nitrate hexahydrate, and 3 mmol of urea, add together in the reactor that 40 ml of deionized water and 10 ml of ethanol mixed solution are housed, magnetically stir until A transparent pink solution was formed, and the carbon cloth was immersed in the solution; the reaction kettle was sealed, and the temperature was raised to 120° C. for 5 hours. After cooling to room temperature, the carbon cloth was taken out, placed in deionized water and absolute ethanol for ultrasonic cleaning several times, and dried in a vacuum oven at 60°C for 12 hours to obtain a carbon cloth with NiCo precursor nanowire array matrix grown on the surface...
Embodiment 2
[0033] (1) Take a carbon cloth with a size of 1 cm × 2 cm and put it in dilute hydrochloric acid, acetone, ethanol and deionized water for ultrasonic cleaning, and finally dry it in a vacuum oven at 60 ° C for 3 h for later use. The concentration of dilute hydrochloric acid is 3M.
[0034] (2) Get 2 millimoles of nickel nitrate hexahydrate, 2 millimoles of cobalt nitrate hexahydrate, and 4 millimoles of urea and add together in the reactor that the mixed solution of 20ml deionized water and 5ml ethanol is housed, and magnetically stir until A transparent pink solution was formed, and the carbon cloth was immersed in the solution; the reaction kettle was sealed, and the temperature was raised to 120° C. for 5 hours. After cooling to room temperature, the carbon cloth was taken out, placed in deionized water and absolute ethanol for ultrasonic cleaning several times, and dried in a vacuum oven at 60°C for 12 hours to obtain a carbon cloth with NiCo precursor nanowire array matri...
Embodiment 3
[0039] (1) Take a carbon cloth with a size of 1 cm × 2 cm and put it in dilute hydrochloric acid, acetone, ethanol and deionized water for ultrasonic cleaning, and finally dry it in a vacuum oven at 60 ° C for 3 h for later use. The concentration of dilute hydrochloric acid is 3M.
[0040] (2) Take 3 millimoles of nickel nitrate hexahydrate, 3 millimoles of cobalt nitrate hexahydrate, and 4.5 millimoles of urea and add them together to a reaction kettle equipped with a mixture of 60 ml of deionized water and 15 ml of ethanol, and stir magnetically until the mixture is formed. Transparent pink solution, immerse the carbon cloth in the solution; seal the reaction kettle, heat up to 120°C and react for 5 hours. After cooling to room temperature, the carbon cloth was taken out, placed in deionized water and absolute ethanol for ultrasonic cleaning several times, and dried in a vacuum oven at 60°C for 12 hours to obtain a carbon cloth with NiCo precursor nanowire array matrix grown...
PUM
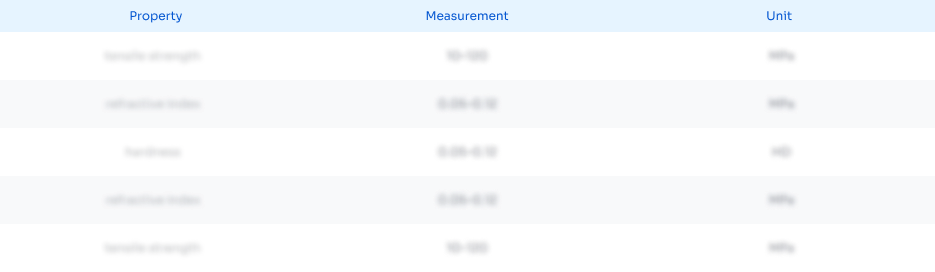
Abstract
Description
Claims
Application Information

- Generate Ideas
- Intellectual Property
- Life Sciences
- Materials
- Tech Scout
- Unparalleled Data Quality
- Higher Quality Content
- 60% Fewer Hallucinations
Browse by: Latest US Patents, China's latest patents, Technical Efficacy Thesaurus, Application Domain, Technology Topic, Popular Technical Reports.
© 2025 PatSnap. All rights reserved.Legal|Privacy policy|Modern Slavery Act Transparency Statement|Sitemap|About US| Contact US: help@patsnap.com