A method for smelting stainless steel in a top-blown converter
A top-blown converter and stainless steel technology, applied in the direction of manufacturing converters, improving process efficiency, etc., to achieve the effects of reducing production costs, lightening alloying tasks, and shortening the production process
- Summary
- Abstract
- Description
- Claims
- Application Information
AI Technical Summary
Problems solved by technology
Method used
Examples
Embodiment 1
[0043] In this example, a 100t top-blown converter is used to smelt stainless steel SUS410L;
[0044] The first semi-steel (for the double dephosphorization method, the first smelting is in the dephosphorization furnace, the main smelting task is dephosphorization, because the carbon content in the steel is about 2% when the steel is tapped, it is a semi-finished product, so it is commonly called the first semi-steel; the second The secondary smelting is in the decarburization furnace, and the main smelting task is to achieve the decarburization target required by the steel type, so it is called the second half steel):
[0045] 92t molten iron, carbon content W[C]=4.29%, silicon content W[Si]=0.45%, phosphorus content W[P]=0.054%, sulfur content W[S]=0.022%, temperature 1334°C;
[0046] Scrap steel 6t, lime addition 55kg / t steel, light burnt dolomite addition 11kg / t steel;
[0047] Oxygen pressure 0.65Mpa, total oxygen accumulation 3079Nm 3 ;Tapping carbon content W[C]=2.45%...
Embodiment 2
[0057] In this example, a 100t top-blown converter is used to smelt stainless steel SUS410L;
[0058] 1. Front half steel:
[0059] 90t molten iron, carbon content W[C]=4.4%, silicon content W[Si]=0.55%, phosphorus content W[P]=0.06%, sulfur content W[S]=0.025%, molten iron temperature 1345°C;
[0060] Steel scrap 8t, lime addition 50kg / t. steel, light burnt dolomite addition 13kg / t. steel;
[0061] Oxygen pressure 0.65Mpa, total oxygen accumulation 3250Nm 3 ; Semi-steel tapping carbon content W[C]=2.3%, silicon content W[Si]=0.02%, phosphorus content W[P]=0.0095%, sulfur content W[S]=0.005%, temperature 1450°C.
[0062] 2. Rear half steel:
[0063] The amount of lime added is 30kg / t steel, the amount of light burnt dolomite added is 12kg / t. steel; the oxygen pressure is 0.80Mpa, and the oxygen accumulation is 4200Nm 3 ; Decarburization end carbon content W[C]=0.035%, phosphorus content W[P]=0.005%, sulfur content W[S]=0.0065%, tapping temperature 1689 ℃.
[0064] 2. Conv...
PUM
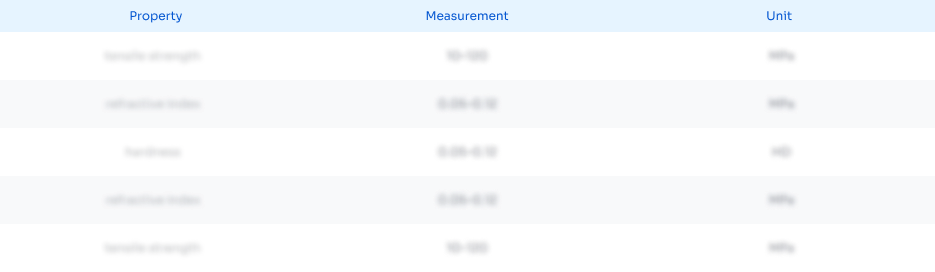
Abstract
Description
Claims
Application Information

- R&D
- Intellectual Property
- Life Sciences
- Materials
- Tech Scout
- Unparalleled Data Quality
- Higher Quality Content
- 60% Fewer Hallucinations
Browse by: Latest US Patents, China's latest patents, Technical Efficacy Thesaurus, Application Domain, Technology Topic, Popular Technical Reports.
© 2025 PatSnap. All rights reserved.Legal|Privacy policy|Modern Slavery Act Transparency Statement|Sitemap|About US| Contact US: help@patsnap.com