Deep cooling treatment technology for copper pipe manufacturing die
A cryogenic treatment and mold technology, used in heat treatment furnaces, manufacturing tools, heat treatment equipment, etc., can solve problems such as poor wear resistance, and achieve the effects of enhanced reliability, improved service life and simple operation.
- Summary
- Abstract
- Description
- Claims
- Application Information
AI Technical Summary
Problems solved by technology
Method used
Image
Examples
Embodiment 1
[0031] like Figure 1-Figure 3 Shown, among the present invention, a kind of cryogenic treatment process that is used for copper tube making mould, is characterized in that, comprises the steps:
[0032] 1) Driven by the intelligent controller, the machined copper tube mold is placed on the fixture, and the copper tube mold is driven by the fixture to put the copper tube mold into the liquid nitrogen cryogenic tank;
[0033] 2) The temperature in the liquid nitrogen cryogenic tank is kept at -155°C~-170°C, and the copper tube mold is kept in the cryogenic tank for 2.5~4 hours;
[0034] 3) After taking out the copper tube mold, immerse it in warm water at 20°C~30°C to quickly return to temperature. The temperature return rate during soaking is 185°C~210°C / s, and the cryogenically treated copper tube mold is obtained.
[0035]The low-temperature tank includes a steel wall 1, expanded perlite 5, an ultra-low temperature linear sensor 12, and a vacuum valve 16. The inner side of ...
Embodiment 2
[0038] The difference between this embodiment and embodiment 1 is:
[0039] In the present invention, the copper pipe mold is controlled by gradual temperature changes in the low temperature tank, and the temperature in the low temperature tank changes in three stages. First, the low temperature tank maintains a temperature of -155°C~-160°C, and the holding time is 1~2.5 hours; then The low temperature tank maintains the temperature at -160°C~-165°C, and the holding time is 0.5~1 hour; finally, the low temperature tank keeps the temperature at -165°C~-170°C, and the holding time is 0.5~1 hour. The lower end of the steel wall 1 is provided with a leg 19 , which is welded to the steel wall 1 , and the leg 19 is more stably fixed on the lower end of the steel wall 1 through welding.
[0040] In the present invention, when the cryogenic tank is working, the vacuum valve 16 is opened when the cryogenic liquid is input, and the interlayer between the high-strength carbon steel 4 and...
PUM
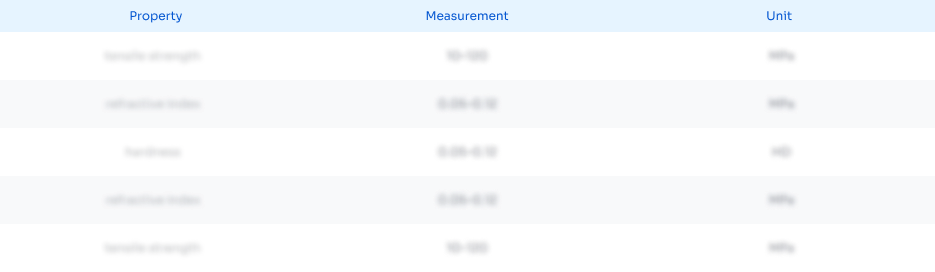
Abstract
Description
Claims
Application Information

- R&D
- Intellectual Property
- Life Sciences
- Materials
- Tech Scout
- Unparalleled Data Quality
- Higher Quality Content
- 60% Fewer Hallucinations
Browse by: Latest US Patents, China's latest patents, Technical Efficacy Thesaurus, Application Domain, Technology Topic, Popular Technical Reports.
© 2025 PatSnap. All rights reserved.Legal|Privacy policy|Modern Slavery Act Transparency Statement|Sitemap|About US| Contact US: help@patsnap.com