Glaze material and preparation method thereof
A glaze and raw material technology, applied in the field of glaze and its preparation, can solve the problems of wasting production time, prone to agglomeration, increase production cost, etc., and achieve the effects of improving effect, improving dispersion effect, and improving heat dissipation capacity.
- Summary
- Abstract
- Description
- Claims
- Application Information
AI Technical Summary
Problems solved by technology
Method used
Image
Examples
preparation example Construction
[0020] The invention provides a kind of preparation method of glaze, comprising the following steps:
[0021] (1) Weigh the dry raw materials in the glaze formula according to the formula, add them into the mixing tank of the planetary mixer and stir and mix to obtain the dry raw material mixture;
[0022] (2) transfer the dry raw material mixture into a ball mill, add water accounting for 5-10% of the total water weight to wet the dry raw material mixture, ball mill, and pass through a 800-1200 mesh sieve after ball milling;
[0023] (3) Transfer the sieved dry raw material mixture into the mixing tank of the planetary mixer, add the remaining amount of water, vacuumize to -0.05~-0.1MPa, stir and mix in vacuum for 50~60min, and finally adjust the water content to 53~58%, obtain described glaze.
[0024] In the present invention, the dry materials in the glaze formula are mixed in advance, so that the dry materials are mixed more fully and evenly, which avoids the easy agglom...
Embodiment 1
[0054] A method for processing ceramic products, comprising the steps of:
[0055] S1: blank processing and blank forming processing,
[0056] Including crushing and sieving blocky solid materials to obtain granular raw materials; followed by iron removal, mud dehydration, aging, mud refining, and granulation to obtain a billet with particle gradation and good fluidity;
[0057] Form the blank into the shape of a ceramic product, then use mixed abrasives to spray the surface of the blank at high speed, and then dry it to obtain a green body;
[0058] The mixed abrasive includes a mixture of aluminum oxide, silicon oxide, diamond powder and glass powder, each raw material component is ball milled and passed through a 1100 mesh sieve, and the mass ratio of aluminum oxide, silicon oxide, diamond powder and glass powder is 1 :0.3:1.4:0.6;
[0059] The conditions of the high-speed spraying include: using nitrogen as the carrier gas, the output of the mixed abrasive is 65g / min, th...
Embodiment 2
[0068] The processing method of ceramic products as provided in Example 1, the difference is that in step S2, the glaze includes the following raw materials in parts by weight: 28 parts of potassium feldspar, 35 parts of quartz, 10 parts of talcum powder, and 5 parts of corundum , 5 parts of glass powder, 3 parts of alumina powder, 4 parts of sodium silicate, 1 part of diamond powder, 10 parts of cobalt green pigment, 70 parts of water;
[0069] Others remain unchanged, and the ceramic product is obtained by processing according to the processing method of Example 1.
PUM
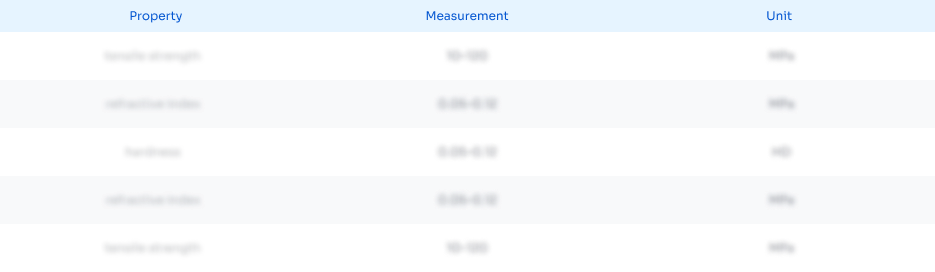
Abstract
Description
Claims
Application Information

- Generate Ideas
- Intellectual Property
- Life Sciences
- Materials
- Tech Scout
- Unparalleled Data Quality
- Higher Quality Content
- 60% Fewer Hallucinations
Browse by: Latest US Patents, China's latest patents, Technical Efficacy Thesaurus, Application Domain, Technology Topic, Popular Technical Reports.
© 2025 PatSnap. All rights reserved.Legal|Privacy policy|Modern Slavery Act Transparency Statement|Sitemap|About US| Contact US: help@patsnap.com