Method for producing chlorobenzene and dichlorobenzene by catalytic distillation and degradation of hexachlorobenzene
A catalytic distillation and catalytic distillation tower technology, applied in the field of selective catalytic hydrogenation, can solve the problem of low concentration of hexachlorobenzene, and achieve the effects of good selectivity, strong practicability and high efficiency
- Summary
- Abstract
- Description
- Claims
- Application Information
AI Technical Summary
Problems solved by technology
Method used
Image
Examples
Embodiment 1
[0029] 1. Catalyst preparation
[0030] Dissolve 0.44g of cobalt chloride and 4.28g of lithium chloride into 100mL of 50% ethanol aqueous solution, add 98.3g of θ-alumina, impregnate for 12 hours, then place in an oven to dry at 150°C for 4 hours, and then put Calcined at 600° C. for 2 hours in a muffle furnace to obtain a catalyst precursor. Dissolve 0.67g of palladium chloride and 0.66g of iridium chloride into 110mL of 50% methanol aqueous solution, add the above-mentioned catalyst precursor, soak for 12 hours, then place in an oven to dry at 150°C for 4 hours, and then put it in a Calcined at 600°C for 2 hours in a furnace to obtain the catalyst. The supported amounts of palladium, iridium, cobalt and lithium in the catalyst are 0.4wt%, 0.4wt%, 0.2wt% and 0.7wt%, respectively.
[0031] 2. Catalyst loading
[0032] The fixed-bed catalytic distillation tower is divided into six sections equally from top to bottom, and the catalyzer diluted with coconut shell particle carb...
Embodiment 2
[0038] 1. Catalyst preparation
[0039] Dissolve 1.10g of cobalt chloride and 3.05g of lithium chloride into 100mL of 50% ethanol aqueous solution, add 98.3g of θ-alumina, impregnate for 12 hours, then dry in an oven at 150°C for 4 hours, and then put Calcined at 600° C. for 2 hours in a muffle furnace to obtain a catalyst precursor. Dissolve 0.67g of palladium chloride and 0.49g of iridium chloride into 110mL of 50% methanol aqueous solution, add the above-mentioned catalyst precursor, soak for 12 hours, then place in an oven to dry at 150°C for 4 hours, and then put it in a Calcined at 600°C for 2 hours in a furnace to obtain the catalyst. The supported amounts of palladium, iridium, cobalt and lithium in the catalyst are 0.4wt%, 0.3wt%, 0.5wt% and 0.5wt%, respectively.
[0040] 2. Catalyst loading
[0041]The fixed-bed catalytic distillation tower is divided into six sections equally from top to bottom, and the catalyzer diluted with coconut shell particle carbon is fill...
Embodiment 3
[0047] 1. Catalyst preparation
[0048] Dissolve 0.44g of cobalt chloride and 2.44g of lithium chloride into 100mL of 50% ethanol aqueous solution, add 98.8g of θ-alumina, impregnate for 12 hours, then dry in an oven at 150°C for 4 hours, and then put Calcined at 600° C. for 2 hours in a muffle furnace to obtain a catalyst precursor. Dissolve 0.67g of palladium chloride and 0.33g of iridium chloride into 110mL of 50% methanol aqueous solution, add the above-mentioned catalyst precursor, soak for 12 hours, then place in an oven to dry at 150°C for 4 hours, and then put it in a Calcined at 600°C for 2 hours in a furnace to obtain the catalyst. The supported amounts of palladium, iridium, cobalt and lithium in the catalyst are 0.4wt%, 0.2wt%, 0.2wt% and 0.4wt%, respectively.
[0049] 2. Catalyst loading
[0050] The fixed-bed catalytic distillation tower is divided into six sections equally from top to bottom, and the catalyzer diluted with coconut shell particle carbon is fil...
PUM
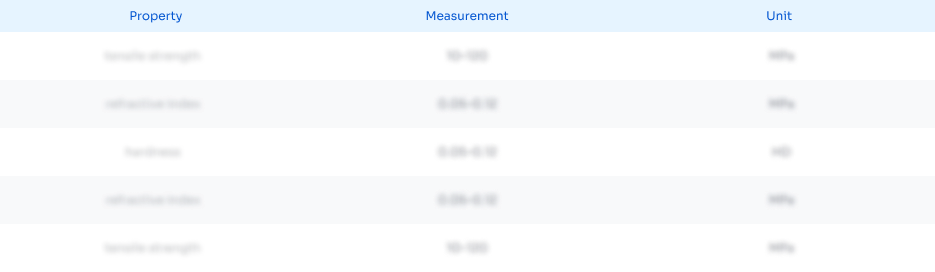
Abstract
Description
Claims
Application Information

- R&D
- Intellectual Property
- Life Sciences
- Materials
- Tech Scout
- Unparalleled Data Quality
- Higher Quality Content
- 60% Fewer Hallucinations
Browse by: Latest US Patents, China's latest patents, Technical Efficacy Thesaurus, Application Domain, Technology Topic, Popular Technical Reports.
© 2025 PatSnap. All rights reserved.Legal|Privacy policy|Modern Slavery Act Transparency Statement|Sitemap|About US| Contact US: help@patsnap.com