Nano-organic-silica anti-corrosion coating
A nano-organosilicon and anti-corrosion coating technology, applied in the field of nano-materials, can solve the problems of poor wear resistance, poor high temperature anti-corrosion effect, discoloration, etc., to improve friction resistance and corrosion resistance, improve mechanical strength and adhesion. The effect of improving the force and interface adhesion
- Summary
- Abstract
- Description
- Claims
- Application Information
AI Technical Summary
Problems solved by technology
Method used
Image
Examples
Embodiment 1
[0023] The preparation method of the modified nano zinc oxide-graphene oxide composite powder comprises the following steps:
[0024] 1) Dissolve sodium lauryl sulfate in hot water at 70°C for stirring and dispersing, then add nano-zinc oxide for stirring and dispersing, ultrasonically treat for 1.5h, and then filter and dry to obtain modified nano-zinc oxide powder ;
[0025] 2) Add the modified nano-zinc oxide powder and graphene oxide into 2wt% itaconic acid solution, stir and disperse for 3 hours, then heat up to 60°C, add aminopropyltriethoxysilane, and react 2 hours, filter and dry the filtrate. The mass ratio of sodium lauryl sulfate to nano-zinc oxide is 7:1, the mass ratio of nano-zinc oxide to graphene oxide is 2:1, and the mass ratio of nano-zinc oxide to aminopropyltriethoxysilane The ratio is 15:1.
[0026] The modification effect was measured by sedimentation experiments. Weighed 1-1.5g of the above-mentioned modified nano-zinc oxide-graphene oxide composite p...
Embodiment 2
[0029] The preparation method of the modified nano zinc oxide-graphene oxide composite powder comprises the following steps:
[0030] 1) Dissolve sodium lauryl sulfate in hot water at 80°C for stirring and dispersing, then add nano-zinc oxide for stirring and dispersing, ultrasonically treat for 0.5h, and then filter and dry to obtain modified nano-zinc oxide powder ;
[0031] 2) Add the modified nano-zinc oxide powder and graphene oxide into 5wt% itaconic acid solution, stir and disperse for 1 hour, then raise the temperature to 50°C, and then add methacryloxypropyltrimethoxy Silane, react for 4 hours, filter and dry the filtrate. The mass ratio of sodium lauryl sulfate to nano-zinc oxide is 5:1, the mass ratio of nano-zinc oxide to graphene oxide is 3:1, and the mass ratio of nano-zinc oxide to methacryloxypropyltrimethoxy The mass ratio of silane is 25:1.
[0032] It can be seen from the test that the unmodified nano-zinc oxide-graphene oxide will completely settle down ...
Embodiment 3
[0034] A kind of nano organosilicon anticorrosion coating, according to parts by weight, comprises the following components:
[0035] 43 parts of water-soluble epoxy resin, 24 parts of alkyd resin, 9 parts of modified nano-zinc oxide-graphene oxide composite powder in Example 1, 13 parts of nano-silica, 7 parts of diatom mud, hydroxymethyl fiber 6 parts of elemental, 15 parts of tetraethoxysilane, 12 parts of zinc phosphate, 4 parts of alcohol ester twelve parts, 0.3 part of sodium oleate, 0.9 part of isopropanol, 0.3 part of emulsified methyl silicone oil and 40 parts of water.
[0036] 35-50 parts of water-soluble epoxy resin, 35-45 parts of alkyd resin, 6-12 parts of modified nano-zinc oxide-graphene oxide composite powder, 10-16 parts of nano-silica, 5-10 parts of diatom mud 4-8 parts of hydroxymethyl cellulose, 12-18 parts of tetraethoxysilane, 10-16 parts of zinc phosphate, 2-6 parts of coalescent, 0.1-0.5 parts of dispersant, 2-2 parts of isopropanol 6 parts, 0.1-0.5 p...
PUM
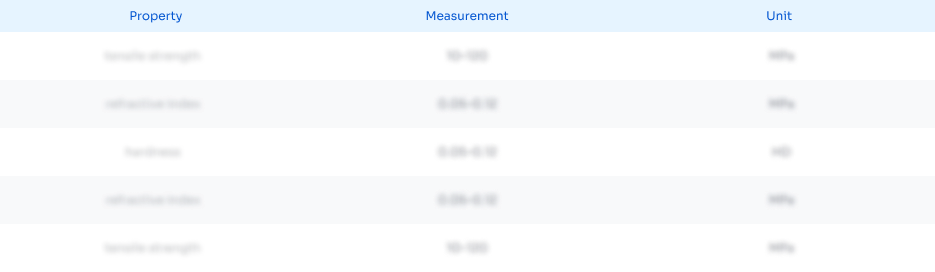
Abstract
Description
Claims
Application Information

- R&D Engineer
- R&D Manager
- IP Professional
- Industry Leading Data Capabilities
- Powerful AI technology
- Patent DNA Extraction
Browse by: Latest US Patents, China's latest patents, Technical Efficacy Thesaurus, Application Domain, Technology Topic, Popular Technical Reports.
© 2024 PatSnap. All rights reserved.Legal|Privacy policy|Modern Slavery Act Transparency Statement|Sitemap|About US| Contact US: help@patsnap.com