Device and method for separating n-butanol from n-butyl ether by using extraction and distillation process
A technology of n-butanol and n-butyl ether, applied in chemical instruments and methods, separation/purification of ether, purification/separation of oxygenated compounds, etc., can solve problems such as separation, achieve simple and controllable process, no waste discharge, The effect of low process energy consumption
- Summary
- Abstract
- Description
- Claims
- Application Information
AI Technical Summary
Problems solved by technology
Method used
Image
Examples
specific Embodiment 1
[0034] A method utilizing extraction and rectification process to separate n-butanol and n-butyl ether, the steps are as follows:
[0035]The raw material comes from the DBP process, characterized by 93% butyl ether and 7% butanol. Operation, reflux ratio 1, extractant recovery tower, normal pressure operation, reflux ratio 0.26. The temperature at the top of the butyl ether recovery tower is 142.1°C, the temperature at the bottom of the butyl ether recovery tower is 197.6°C, the temperature at the top of the extraction agent recovery tower is 117.5°C, and the temperature at the bottom of the extraction agent recovery tower is 178.2°C. The equipment runs continuously for 12 hours, the purity of the butyl ether product is 98.6%, and the purity of the butanol product is 99.7%.wt.
specific Embodiment 2
[0036] A method utilizing extraction and rectification process to separate n-butanol and n-butyl ether, the steps are as follows:
[0037] The overall process is the same as in Example 1, but the difference is that the raw material comes from the DBP process, characterized by 93% butyl ether and 7% butanol. The extraction tower is operated at normal temperature and pressure, and the extraction agent and raw material feed The quantities are 1000kg / h and 500kg / h respectively; the butyl ether recovery tower operates under normal pressure with a reflux ratio of 2, and the extractant recovery tower operates under normal pressure with a reflux ratio of 0.3. The temperature at the top of the butyl ether recovery tower is 142.3°C, the temperature at the bottom of the butyl ether recovery tower is 198.4°C, the temperature at the top of the extraction agent recovery tower is 117.4°C, and the temperature at the bottom of the extraction agent recovery tower is 179.9°C. The equipment runs ...
PUM
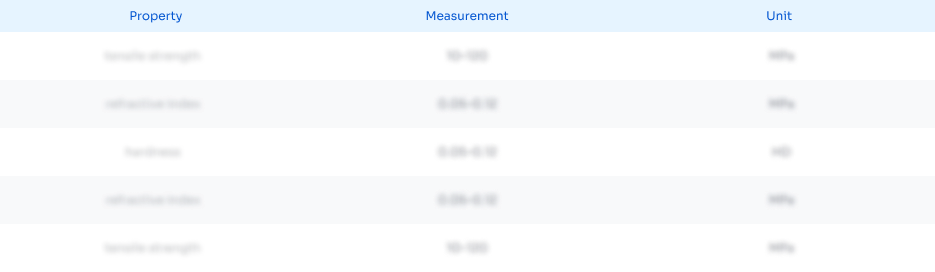
Abstract
Description
Claims
Application Information

- R&D Engineer
- R&D Manager
- IP Professional
- Industry Leading Data Capabilities
- Powerful AI technology
- Patent DNA Extraction
Browse by: Latest US Patents, China's latest patents, Technical Efficacy Thesaurus, Application Domain, Technology Topic, Popular Technical Reports.
© 2024 PatSnap. All rights reserved.Legal|Privacy policy|Modern Slavery Act Transparency Statement|Sitemap|About US| Contact US: help@patsnap.com