Solder mask manufacturing process for PCBs applied to LED display screens
A technology of LED display and PCB board, applied in printed circuit manufacturing, secondary processing of printed circuit, electrical components, etc., can solve the problem of LED light board easily producing ink color
- Summary
- Abstract
- Description
- Claims
- Application Information
AI Technical Summary
Problems solved by technology
Method used
Image
Examples
Embodiment Construction
[0025] Please refer to figure 1 and figure 2 As shown, it discloses a PCB board solder mask manufacturing process for LED display applications, including the following steps:
[0026] (1) Pre-treatment: The surface of the PCB board 10 is treated by a browning process to increase the roughness of the copper surface 11 of the PCB board 10 and the roughness is uniform; specifically, the surface of the PCB board 10 is removed by acid and alkali washing Oxide, oil and fingerprints and other foreign matter, together with the liquid medicine of the activation tank and the browning tank, will chemically react the copper surface 11 of the PCB board 10 .
[0027] (2) Silk screen printing: Silk screen printing is performed on the copper surface 11 of the PCB board 10. During the silk screen printing process, the viscosity of the ink, the angle of the squeegee, the amount of ink scraped by the squeegee, and the speed of the squeegee are strictly controlled. After the silk screen, the st...
PUM
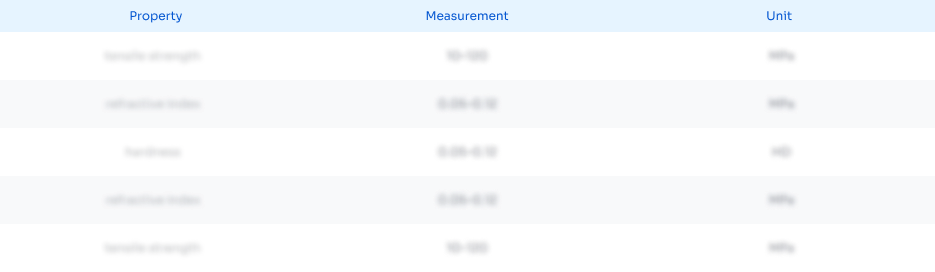
Abstract
Description
Claims
Application Information

- R&D
- Intellectual Property
- Life Sciences
- Materials
- Tech Scout
- Unparalleled Data Quality
- Higher Quality Content
- 60% Fewer Hallucinations
Browse by: Latest US Patents, China's latest patents, Technical Efficacy Thesaurus, Application Domain, Technology Topic, Popular Technical Reports.
© 2025 PatSnap. All rights reserved.Legal|Privacy policy|Modern Slavery Act Transparency Statement|Sitemap|About US| Contact US: help@patsnap.com