Surface modification method for ceramic material with high-temperature structure
A ceramic material and surface modification technology, which is applied in chemical instruments and methods, fibrous fillers, inorganic pigment treatment, etc., can solve the problems of harsh modification conditions, low grafting rate, long reaction cycle, etc. Effect of improving interaction force and improving dispersibility
- Summary
- Abstract
- Description
- Claims
- Application Information
AI Technical Summary
Problems solved by technology
Method used
Image
Examples
Embodiment 1
[0058] (1) Weigh 2.6g of sodium hydroxide and 2.5g of potassium hydroxide, add 500mg of nano-silicon carbide, grind it into a fine powder in a mortar, and mix well. The mixed powder was reacted in a crucible at 170° C. for 5 h, and cooled to room temperature. The mixed powder treated by the solid phase method was dispersed in a certain amount of water, and the mixed solution was treated with an ultrasonic cell pulverizer for 3 hours, and then the supernatant was removed by centrifugation. Wash with distilled water 3 times until the pH of the solution is neutral to obtain pre-hydroxylated silicon carbide.
[0059] (2) In an ice bath, dissolve 10.8 g of p-phenylenediamine in 8 mL of 98% concentrated sulfuric acid and 100 mL of deionized water, and stir until the p-phenylenediamine is completely dissolved. Add 30% sodium nitrite solution dropwise from the liquid surface to the above solution to prepare the corresponding sulfated diazonium salt solution.
[0060] (3) Disperse th...
Embodiment 2
[0062] (1) Weigh 2.9g of sodium hydroxide and 2.5g of potassium hydroxide, add 500mg of nano-silicon carbide, grind it into a fine powder in a mortar, and mix well. Transfer the mixed powder into a 100mL hydrothermal reaction kettle, add 70mL of pure water, react at 180°C for 6h, cool to room temperature, use an ultrasonic cell pulverizer to treat the mixture for 3h, and then centrifuge to remove the supernatant, the lower layer Wash with distilled water 3 times until the pH of the solution is neutral to obtain pre-hydroxylated silicon carbide.
[0063] (2) In an ice bath, dissolve 2.7 g of p-phenylenediamine in 2 mL of 98% concentrated sulfuric acid and 50 mL of deionized water, and stir until the p-phenylenediamine is completely dissolved. Add 30% sodium nitrite solution dropwise from the liquid surface to the above solution to prepare the corresponding sulfated diazonium salt solution.
[0064] (3) Disperse the pre-hydroxylated silicon carbide in step (1) in 100 mL of deio...
Embodiment 3
[0066] (1) Weigh 2.6g of sodium hydroxide and 2.4g of potassium hydroxide, add 500mg of nano-silicon carbide, grind it into a fine powder in a mortar, and mix well. First react the mixed powder in a crucible at 180°C for 3h, then transfer the mixed powder into a 100mL hydrothermal reaction kettle, add 70mL of pure water, and react at 180°C for 6h. After cooling to room temperature, the mixture was treated with an ultrasonic cell pulverizer for 2 hours, then the supernatant was removed by centrifugation, and the lower layer was washed with distilled water for 3 times until the pH of the solution was neutral to obtain pre-hydroxylated nano-silicon carbide.
[0067] (2) In an ice bath, dissolve 5.4 g of p-phenylenediamine in 4 mL of 98% concentrated sulfuric acid and 32 mL of deionized water, and stir until the p-phenylenediamine is completely dissolved. Add 30% sodium nitrite solution dropwise from the liquid surface to the above solution to prepare the corresponding sulfated di...
PUM
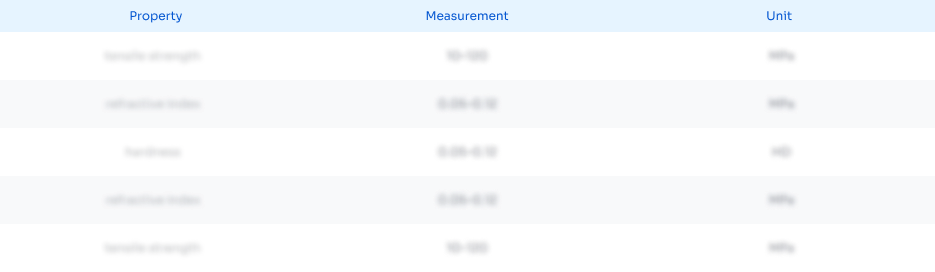
Abstract
Description
Claims
Application Information

- R&D
- Intellectual Property
- Life Sciences
- Materials
- Tech Scout
- Unparalleled Data Quality
- Higher Quality Content
- 60% Fewer Hallucinations
Browse by: Latest US Patents, China's latest patents, Technical Efficacy Thesaurus, Application Domain, Technology Topic, Popular Technical Reports.
© 2025 PatSnap. All rights reserved.Legal|Privacy policy|Modern Slavery Act Transparency Statement|Sitemap|About US| Contact US: help@patsnap.com