A method for manufacturing a grooved Schottky front silver surface metal structure
A technology of surface metal and manufacturing method, applied in semiconductor/solid-state device manufacturing, semiconductor devices, electrical components, etc., can solve the problems of difficult processing, prone to inverted triangle, need, etc., to reduce the instability of the processing process and optimize the thin film Inter-stress, the effect of reducing the manufacturing cost
- Summary
- Abstract
- Description
- Claims
- Application Information
AI Technical Summary
Problems solved by technology
Method used
Image
Examples
Embodiment
[0025] Firstly, the trench Schottky product sheet to be used as a potential barrier is cleaned before the barrier: the silicon wafer is cleaned with a cleaning solution with a volume ratio of HF:H2O of 20:1, and the cleaning time is 20 minutes. The surface of the chip is clean and will not affect the subsequent steps, so that the obtained barrier structure parameters are stable;
[0026] The thickness of the evaporated Ti barrier is Form a silicon wafer-Ti barrier structure. The Ti metal layer of this thickness is stable and the barrier is not prone to defects; It is an alloy of barrier metals, thereby forming a Schottky barrier and releasing stress at the same time;
[0027] The aluminum metal is then evaporated to a thickness of Form a silicon wafer-Ti barrier-aluminum metal layer structure, followed by annealing, the annealing temperature is 300-600°C, and the annealing time is 0.5-2h; Forming a silicon wafer-Ti barrier-aluminum metal layer-TiNiAg metal layer structur...
PUM
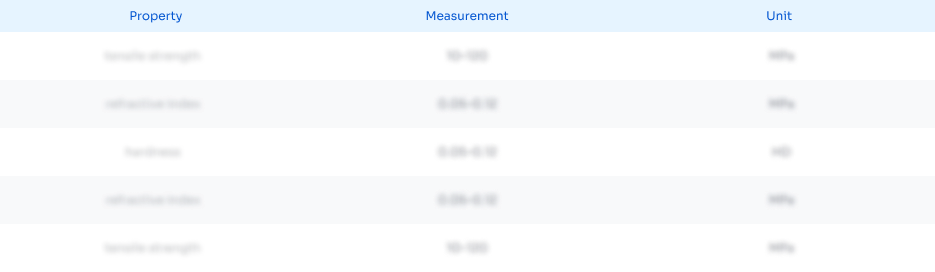
Abstract
Description
Claims
Application Information

- Generate Ideas
- Intellectual Property
- Life Sciences
- Materials
- Tech Scout
- Unparalleled Data Quality
- Higher Quality Content
- 60% Fewer Hallucinations
Browse by: Latest US Patents, China's latest patents, Technical Efficacy Thesaurus, Application Domain, Technology Topic, Popular Technical Reports.
© 2025 PatSnap. All rights reserved.Legal|Privacy policy|Modern Slavery Act Transparency Statement|Sitemap|About US| Contact US: help@patsnap.com