High rigidity and light space camera lens cylinder and test method for vibration resistance stability thereof
A space camera, high stiffness technology, applied in the field of support between the primary mirror and secondary mirror of space high-resolution cameras, high stiffness and lightweight space camera lens barrels, can solve the problems of poor stability of resin-based composite materials, and reach the market Broad application prospects, improved stability and strong versatility
- Summary
- Abstract
- Description
- Claims
- Application Information
AI Technical Summary
Problems solved by technology
Method used
Image
Examples
Embodiment Construction
[0029] In order to make the solution of the present invention clearer, the present invention will be further described below in conjunction with the accompanying drawings and specific embodiments:
[0030] Such as figure 1 As shown, a high-rigidity light-weight space camera lens barrel includes a barrel body 1, a primary mirror flange 2, a secondary mirror flange 3 and a reinforcing rib 4; the barrel body 1 is a hollow cylinder, and one end of the barrel body 1 is provided with a The main mirror flange 2 of the main mirror of the space camera and the other end of the cylinder body 1 are provided with a secondary mirror flange 3 for connecting the secondary mirror of the space camera, and the outside of the cylinder body 1 is provided with reinforcing ribs 4 for reinforcing the structure. The primary mirror flange 2, the secondary mirror flange 3 and the rib 4 are integrally formed by three-dimensional braiding of silicon carbide.
[0031] Preferably, the ratio of the inner di...
PUM
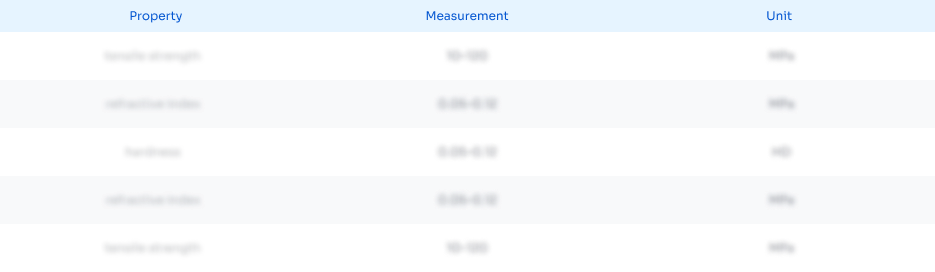
Abstract
Description
Claims
Application Information

- Generate Ideas
- Intellectual Property
- Life Sciences
- Materials
- Tech Scout
- Unparalleled Data Quality
- Higher Quality Content
- 60% Fewer Hallucinations
Browse by: Latest US Patents, China's latest patents, Technical Efficacy Thesaurus, Application Domain, Technology Topic, Popular Technical Reports.
© 2025 PatSnap. All rights reserved.Legal|Privacy policy|Modern Slavery Act Transparency Statement|Sitemap|About US| Contact US: help@patsnap.com