Preparation method of improved type graded porous carbon-doped material
A technology of graded porous and carbon materials, applied in chemical instruments and methods, carbon compounds, inorganic chemistry, etc., can solve problems such as difficult recycling, high consumption of deionized water, and high pressure on environmental protection, so as to improve the production environment, The effect of reducing environmental risks and reducing raw materials for production
- Summary
- Abstract
- Description
- Claims
- Application Information
AI Technical Summary
Problems solved by technology
Method used
Image
Examples
Embodiment 1
[0023] Add sodium alginate (0.4g) into deionized water (19.6mL), stir to dissolve it completely, then add aniline (0.372mL) to the solution and continue stirring to make the mixed system dissolve evenly. Pre-cool the reaction system at 0-4°C for half an hour, then add ammonium persulfate (0.912g) while stirring rapidly, stop stirring after a few seconds, and finally place the reaction system at room temperature for 12 hours to obtain poly Aniline-sodium alginate hydrogel hybrid system.
[0024] The prepared polyaniline-sodium alginate hydrogel mixed system was freeze-dried, then transferred to a tube furnace, and heated from room temperature to 600 °C at a rate of 5 °C / min under an argon atmosphere, and kept for carbonization for 2 h. After natural cooling, the obtained carbide was washed three times with deionized water, and then vacuum-dried at 60° C. for 24 hours to obtain hierarchically porous doped carbon.
Embodiment 2
[0026] Add sodium alginate (0.4g) into deionized water (19.6mL), stir to dissolve it completely, then add aniline (0.186mL) to the solution and continue stirring to make the mixed system dissolve evenly. Pre-cool the reaction system at 0-4°C for half an hour, then add ammonium persulfate (0.456g) while stirring rapidly, stop stirring after a few seconds, and finally place the reaction system at room temperature for 12 hours to obtain poly Aniline-sodium alginate hydrogel hybrid system.
[0027] The prepared polyaniline-sodium alginate hydrogel mixed system was freeze-dried, then transferred to a tube furnace, and raised from room temperature to 700°C at a rate of 5°C / min under an argon atmosphere, and then carbonized for 2 hours. After natural cooling, the obtained carbide was washed three times with deionized water, and then vacuum-dried at 60° C. for 24 hours to obtain hierarchically porous doped carbon.
Embodiment 3
[0029] Add sodium alginate (0.4g) into deionized water (19.6mL), stir to dissolve it completely, then add aniline (0.744mL) to the solution and continue stirring to make the mixed system dissolve evenly. Pre-cool the reaction system at 0-4°C for half an hour, then add ammonium persulfate (1.824g) while stirring rapidly, stop stirring after a few seconds, and finally place the reaction system at room temperature for 12h to obtain poly Aniline-sodium alginate hydrogel hybrid system.
[0030] The prepared polyaniline-sodium alginate hydrogel mixed system was freeze-dried, then transferred to a tube furnace, and raised from room temperature to 700°C at a rate of 5°C / min under an argon atmosphere, and then carbonized for 2 hours. After natural cooling, the obtained carbide was washed three times with deionized water, and then vacuum-dried at 60° C. for 24 hours to obtain hierarchically porous doped carbon.
PUM
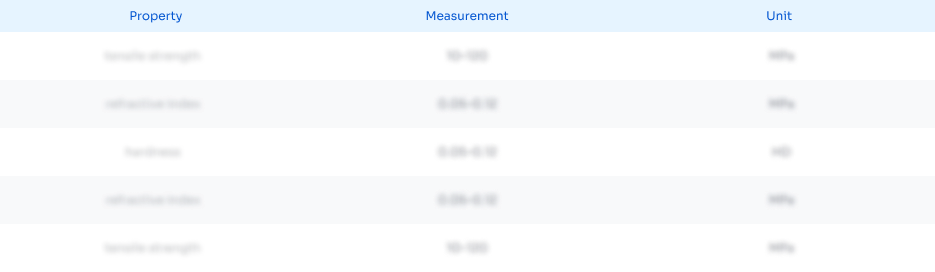
Abstract
Description
Claims
Application Information

- R&D
- Intellectual Property
- Life Sciences
- Materials
- Tech Scout
- Unparalleled Data Quality
- Higher Quality Content
- 60% Fewer Hallucinations
Browse by: Latest US Patents, China's latest patents, Technical Efficacy Thesaurus, Application Domain, Technology Topic, Popular Technical Reports.
© 2025 PatSnap. All rights reserved.Legal|Privacy policy|Modern Slavery Act Transparency Statement|Sitemap|About US| Contact US: help@patsnap.com