Easy-to-weld carbon structure steel based on thin strip cast rolling and manufacturing method thereof
A technology of carbon structural steel and thin strip casting and rolling, which is applied in the field of steel production to achieve the effect of fewer production processes, lower production costs and labor costs
- Summary
- Abstract
- Description
- Claims
- Application Information
AI Technical Summary
Problems solved by technology
Method used
Image
Examples
Embodiment 1
[0039] (1) Smelting: In step (1), EAF electric furnace steelmaking is used, VD vacuum decarburization and deoxidation, and LF refining are used to obtain molten steel with qualified components. Percent by weight: C: 0.031, Mn: 0.567, Si: 0.149, P: 0.014, S: 0.002, Al: 0.002, and the balance is Fe and impurity elements. Its carbon equivalent Ceq value is 0.14, cold crack sensitivity index P cm The value is 0.07.
[0040] (2) Thin strip continuous casting: The molten steel with qualified composition is cast and rolled by twin-roll thin strip casting and rolling equipment. With continuous casting. A cast strip with a thickness of 1.85 mm was obtained.
[0041] (3) Hot rolling: the cast strip is then rolled into a thin strip of 1.55mm through one pass of hot rolling with a reduction of 16%, and the rolling exit temperature is 890°C.
[0042] (4) Cooling and coiling: the hot-rolled thin strip is cooled to 598°C by an air-mist cooling system, and the hot-rolled coil is obtained ...
Embodiment 2
[0047](1) Smelting: In step (1), EAF electric furnace steelmaking is used, VD vacuum decarburization and deoxidation, and LF refining are used to obtain molten steel with qualified components. Percent by weight: C: 0.026, Mn: 0.584, Si: 0.175, P: 0.009, S: 0.002, Al: 0.002, and the balance is Fe and impurity elements. Its carbon equivalent Ceq value is 0.14, cold crack sensitivity index P cm The value is 0.07.
[0048] (2) Thin strip continuous casting: The molten steel with qualified composition is cast and rolled by twin-roll thin strip casting and rolling equipment. With continuous casting. A cast strip with a thickness of 1.78 mm was obtained.
[0049] (3) Hot rolling: the cast strip is then rolled into a thin strip of 1.4mm through one pass of hot rolling with a reduction of 21%, and the rolling exit temperature is 896°C.
[0050] (4) Cooling and coiling: the hot-rolled thin strip is cooled to 602°C by an air-mist cooling system, and the hot-rolled coil is obtained af...
Embodiment 3
[0054] (1) Smelting: In step (1), EAF electric furnace steelmaking is used, VD vacuum decarburization and deoxidation, and LF refining are used to obtain molten steel with qualified components. Percent by weight: C: 0.028, Mn: 0.585, Si: 0.164, P: 0.012, S: 0.003, Al: 0.002, and the balance is Fe and impurity elements. Its carbon equivalent Ceq value is 0.14, cold crack sensitivity index P cm The value is 0.07.
[0055] (2) Thin strip continuous casting: The molten steel with qualified composition is cast and rolled by twin-roll thin strip casting and rolling equipment. With continuous casting. A cast strip with a thickness of 1.7 mm was obtained.
[0056] (3) Hot rolling: the cast strip is then rolled into a thin strip of 1.2mm through one pass of hot rolling with a reduction of 30%, and the rolling exit temperature is 903°C.
[0057] (4) Cooling and coiling: the hot-rolled thin strip is cooled to 608°C by an air-mist cooling system, and the hot-rolled coil is obtained af...
PUM
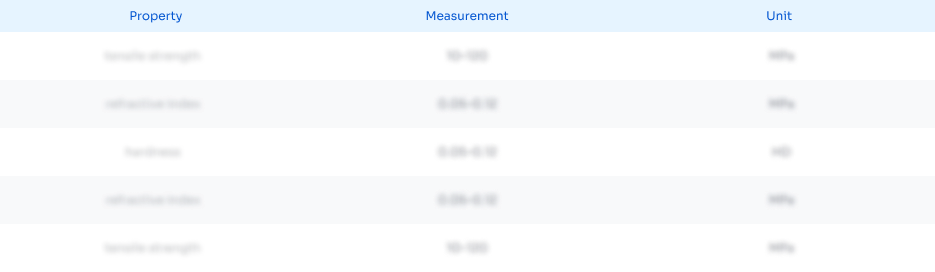
Abstract
Description
Claims
Application Information

- R&D Engineer
- R&D Manager
- IP Professional
- Industry Leading Data Capabilities
- Powerful AI technology
- Patent DNA Extraction
Browse by: Latest US Patents, China's latest patents, Technical Efficacy Thesaurus, Application Domain, Technology Topic, Popular Technical Reports.
© 2024 PatSnap. All rights reserved.Legal|Privacy policy|Modern Slavery Act Transparency Statement|Sitemap|About US| Contact US: help@patsnap.com