Dyeing wastewater recycling method
A dyeing wastewater recycling technology, applied in the field of fabric dyeing, can solve the problems of a large amount of dyeing vat wastewater, fabric reduction cleaning, and more floating colors on the cloth surface, so as to improve the level dyeing property, reduce the floating color on the cloth surface, and improve the quality of fabrics Effect
- Summary
- Abstract
- Description
- Claims
- Application Information
AI Technical Summary
Problems solved by technology
Method used
Image
Examples
Embodiment 1
[0030] Step 1, weigh 30 grams of disperse yellow dye 114, 9 grams of polymer dispersant TEGO Dispers760W (Germany Tego Chemical Company), 0.05 grams of preservative benzoisothiazopyridine, 0.03 grams of defoamer Surfynol 104E (Nanjing Air Chemical Co., Ltd. Specialty Amine Company), adding 32 grams of water for sanding, sanding to a particle size of about 1 micron, and filtering to obtain liquid disperse yellow 114 dye.
[0031] Step 2: Weigh 0.08 grams of liquid disperse yellow dye, add 97.92 grams of water, 2 grams of 5% leveling agent, and 4 grams of polyester cloth. temperature, keep warm for 45 minutes, then start to cool down to 70 degrees at a rate of 1 degree per minute, use tweezers to clamp out the cloth, and dry the cloth for later use.
[0032] Step 3: Add 4 grams of polyester cloth and 0.08 grams of Disperse Yellow 114 liquid dye to the waste liquid dyed in the previous step, add a small amount of water to 100 grams of the total liquid, and continue to dye continu...
Embodiment 2
[0036]Step 1, weigh 30 grams of blue dye 79:1, 6 grams of polymer dispersant DISPERBYK-192 (BYK), 0.05 grams of preservative benzisothiazopyridine, 0.03 grams of defoamer Surfynol 104E, add 36 grams of water Carry out sand milling, sand milling to a particle size of about 1 micron, and filter to obtain a liquid disperse blue dye 79:1 dye.
[0037] Step 2: Weigh 0.08 grams of the above-mentioned liquid dye, add 97.92 grams of water, 2 grams of 5% leveling agent, and 4 grams of polyester cloth, put them all into the dyeing vat, put them into the proofing machine, and heat up to 130 degrees at a rate of 1 degree per minute , keep warm for 45 minutes, then start to cool down to 70 degrees at a rate of 1 degree per minute, use tweezers to clamp out the cloth, and dry the cloth for later use.
[0038] Step 3: Add 4 grams of polyester cloth and 0.08 grams of liquid disperse blue 79:1 dye to the waste liquid dyed in the previous step, add a small amount of water to the total liquid of...
Embodiment 3
[0042] Step 1. Weigh 30 grams of disperse red dye 343, 9 grams of polymer dispersion ZetaSperse2500 (AIR PRUDUCTS), 0.05 grams of preservative benzoisothiazopyridine, 0.03 grams of defoamer Surfynol 104E, add 36 grams of water for sanding, Sand mill to a particle size of about 1 micron, and filter to obtain liquid disperse red 343 dye.
[0043] Step 2: Weigh 0.08 grams of liquid dye, add 97.92 grams of water, 2 grams of 5% leveling agent, and 4 grams of polyester cloth, all of which are added to the dyeing vat, put into the proofer, and heat up to 130 degrees at a rate of 1 degree per minute. Keep warm for 45 minutes, then start to cool down to 70 degrees at a rate of 1 degree per minute, use tweezers to clamp out the cloth, and dry the cloth for later use.
[0044] Step 3, add 4 grams of polyester cloth and 0.08 grams of liquid disperse red 343 dye to the waste liquid after dyeing, add a small amount of water to 100 grams of total liquid, and continue to dye continuously acco...
PUM
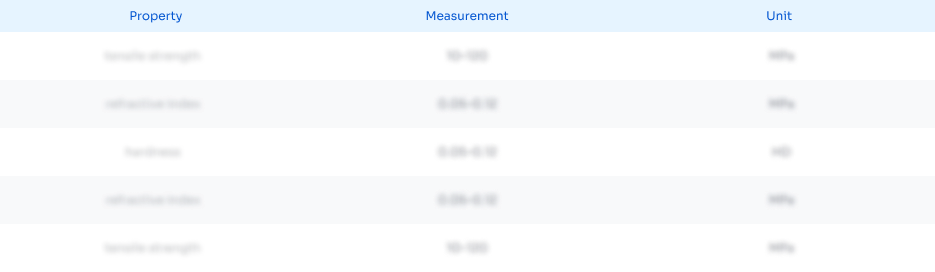
Abstract
Description
Claims
Application Information

- Generate Ideas
- Intellectual Property
- Life Sciences
- Materials
- Tech Scout
- Unparalleled Data Quality
- Higher Quality Content
- 60% Fewer Hallucinations
Browse by: Latest US Patents, China's latest patents, Technical Efficacy Thesaurus, Application Domain, Technology Topic, Popular Technical Reports.
© 2025 PatSnap. All rights reserved.Legal|Privacy policy|Modern Slavery Act Transparency Statement|Sitemap|About US| Contact US: help@patsnap.com