A kind of method that adopts printing technology to make gpp chip
A chip and process technology, which is applied in the field of GPP chip production by printing process, can solve the problems of easy flow of solder on the glass, high production cost, and reduced reliability, and achieve high printing process efficiency, low production cost, and reduced time cost Effect
- Summary
- Abstract
- Description
- Claims
- Application Information
AI Technical Summary
Problems solved by technology
Method used
Examples
Embodiment Construction
[0044] There are three GPP production processes: knife scraping method, electrophoresis method, and photoresist method. The technical difficulty and product quality increase in turn, but the overall technical difficulty is still low, with low investment and rapid increase. With the increase in market demand, a large number of workshops This requires a high-yield and high-efficiency GPP chip preparation process. This solution involves a method for manufacturing GPP chips using a printing process, including silicon wafer pretreatment, diffusion texturing, glass Passivation printing drawing, metallization and test sorting several steps, specifically cleaning after DW slicing, annealing, cleaning after annealing, silicon wafer sorting, pre-diffusion treatment, phosphorus coating, boron source, diffusion, post-diffusion treatment, texturing , printing glue, trench etching, LPCVD deposition SIPOS, printing glass paste, glass firing, LPCVD deposition SiO 2 , printing glue, removing S...
PUM
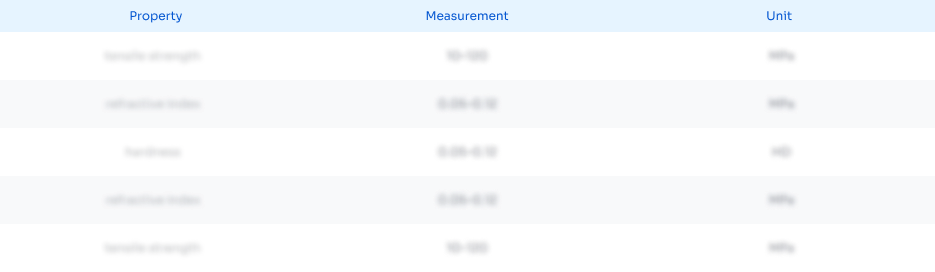
Abstract
Description
Claims
Application Information

- R&D
- Intellectual Property
- Life Sciences
- Materials
- Tech Scout
- Unparalleled Data Quality
- Higher Quality Content
- 60% Fewer Hallucinations
Browse by: Latest US Patents, China's latest patents, Technical Efficacy Thesaurus, Application Domain, Technology Topic, Popular Technical Reports.
© 2025 PatSnap. All rights reserved.Legal|Privacy policy|Modern Slavery Act Transparency Statement|Sitemap|About US| Contact US: help@patsnap.com