Polyvinyl chloride composite foaming material and production method thereof
A polyvinyl chloride and composite foaming technology, which is applied in the field of foam material production, can solve the problems of reducing the heat resistance of materials, cell collapse and deformation, and deformation of foam materials, and achieves improved heat resistance and uniform and dense cells. , the effect of cell reduction
- Summary
- Abstract
- Description
- Claims
- Application Information
AI Technical Summary
Problems solved by technology
Method used
Image
Examples
Embodiment 1
[0035] The specific preparation process of composite carbon nanotube monomer is as follows:
[0036] Step 1: Weigh 1kg of carbon nanotubes and add them to 4L of aqua regia, ultrasonically disperse for 30 minutes, pour the solution into a reaction flask, heat to 90°C for 1 hour of constant temperature reaction, then filter, wash, and dry to obtain carboxylated carbon nanotubes;
[0037]Step 2: Add 1 kg of carboxylated carbon nanotubes prepared in Step 1 into water, mix well, add 1.2 L of thionyl chloride to it, raise the temperature to 60 ° C for 3 hours, add 1.23 kg of acrylamide to the reaction vessel, and raise the temperature Continue to react at 70°C for 4h, then filter, wash and dry to obtain composite carbon nanotube monomer;
[0038] The specific preparation process of the anti-aging filler is as follows:
[0039] ①Add 1kg of nano-calcium carbonate to water, mix evenly, add 2.1kg of trifluoromethanesulfonic anhydride to it, and stir evenly at room temperature;
[0040...
Embodiment 2
[0042] Wherein the specific preparation process of composite carbon nanotube monomer is as follows:
[0043] Step 1: Weigh 1kg of carbon nanotubes and add them to 4L of aqua regia, ultrasonically disperse for 30 minutes, pour the solution into a reaction flask, heat to 90°C for 1 hour of constant temperature reaction, then filter, wash, and dry to obtain carboxylated carbon nanotubes;
[0044] Step 2: Add 1kg of the carboxylated carbon nanotubes prepared in Step 1 into water, mix well, add 1.2L of thionyl chloride to it, raise the temperature to 60°C and react for 3 hours, add 1.26kg of acrylamide to the reaction vessel, and raise the temperature Continue to react at 70°C for 4h, then filter, wash and dry to obtain composite carbon nanotube monomer;
[0045] Wherein the specific preparation process of the anti-aging filler is as follows:
[0046] ①Add 1kg of nano-calcium carbonate to water, mix evenly, add 2.2kg of trifluoromethanesulfonic anhydride to it, and stir evenly at ...
Embodiment 3
[0049] The specific reaction process of polyvinyl chloride composite foam material is as follows:
[0050] In the first step, 6.8 kg of polyvinyl chloride resin powder and 17 kg of tetrahydrofuran solution were added into a three-necked flask, and the temperature was raised to 70° C. and quickly stirred and dissolved to obtain a polyvinyl chloride solution;
[0051] In the second step, the temperature of the polyvinyl chloride solution prepared in the first step was raised to 140°C for reflux, and at the same time, 6.8 kg of initiator, 1.2 kg of dibutyltin maleate and 1.5 kg of the composite carbon nanometer prepared in Example 1 were added to the flask. Tube monomer, stirred and reacted at constant temperature for 8 hours to obtain a polymer solution;
[0052] In the third step, add 0.5 kg of the anti-aging filler prepared in Example 1 to the polymer solution prepared in the second step, stir evenly, heat up to 80°C, and add 0.6 kg of formaldehyde dropwise to the flask using ...
PUM
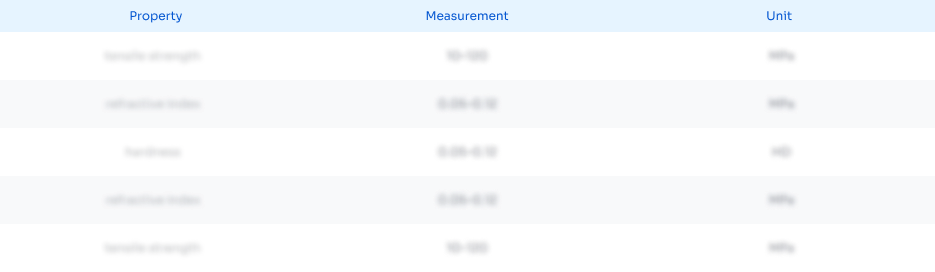
Abstract
Description
Claims
Application Information

- R&D
- Intellectual Property
- Life Sciences
- Materials
- Tech Scout
- Unparalleled Data Quality
- Higher Quality Content
- 60% Fewer Hallucinations
Browse by: Latest US Patents, China's latest patents, Technical Efficacy Thesaurus, Application Domain, Technology Topic, Popular Technical Reports.
© 2025 PatSnap. All rights reserved.Legal|Privacy policy|Modern Slavery Act Transparency Statement|Sitemap|About US| Contact US: help@patsnap.com