Craft bottle one-step forming technology
A molding process and process technology, which is applied in the field of one-step molding process of craft bottles, can solve problems such as unfavorable factory development, rising raw material prices, rising raw material prices, etc., and achieve the effect of reducing labor intensity, reducing bottle shrinkage, and reducing logistics links
- Summary
- Abstract
- Description
- Claims
- Application Information
AI Technical Summary
Problems solved by technology
Method used
Image
Examples
Embodiment 1
[0016] A kind of craft bottle one-step molding process, comprises the following steps:
[0017] 1) Put the PET raw material into the dehumidification drying conveyor for dehumidification and drying to prevent the PET raw material from being hydrolyzed due to excessive moisture and heat in the next process, and control the internal temperature of the dehumidification dryer to 165°C, and the dehumidification and drying time 5h, then check the water content of the PET raw material, if the water content of the PET raw material is greater than 50ug / g, then use 155°C to continue drying until the water content of the PET raw material is less than 50ug / g, if the water content of the PET raw material is less than 50ug / g, then into the heating barrel;
[0018] 2) In order to make the heating cylinder evenly heat and plasticize the fed PET raw material to obtain a melt, the internal temperature of the heating cylinder is controlled at 275°C during the plasticization process to avoid exce...
Embodiment 2
[0025] A kind of craft bottle one-step molding process, comprises the following steps:
[0026] 1) Put the PET raw material into the dehumidification drying conveyor for dehumidification and drying to prevent the PET raw material from being hydrolyzed due to excessive moisture and heat in the next process, and control the internal temperature of the dehumidification dryer to 155°C, and the dehumidification and drying time 3h, then check the water content of the PET raw material, if the water content of the PET raw material is greater than 30ug / g, then use a temperature of 145°C to continue drying until the water content of the PET raw material is less than 30ug / g, if the water content of the PET raw material is less than 30ug / g, then into the heating barrel;
[0027] 2) In order to make the heating cylinder evenly heat and plasticize the fed PET raw material to obtain a melt, the internal temperature of the heating cylinder is controlled at 265°C during the plasticization proc...
Embodiment 3
[0034] A kind of craft bottle one-step molding process, comprises the following steps:
[0035] 1) Put the PET raw material into the dehumidification and drying conveyor for dehumidification and drying to prevent the PET raw material from being hydrolyzed due to excessive moisture and heat in the next process, and control the temperature inside the dehumidification dryer to 160°C, and the dehumidification and drying time 4h, then check the water content of the PET raw material, if the water content of the PET raw material is greater than 40ug / g, then use 150°C to continue drying until the water content of the PET raw material is less than 40ug / g, if the water content of the PET raw material is less than 40ug / g, then into the heating barrel;
[0036] 2) In order to make the heating cylinder evenly heat and plasticize the fed PET raw material to obtain a melt, the internal temperature of the heating cylinder is controlled at 270°C during the plasticization process to avoid exces...
PUM
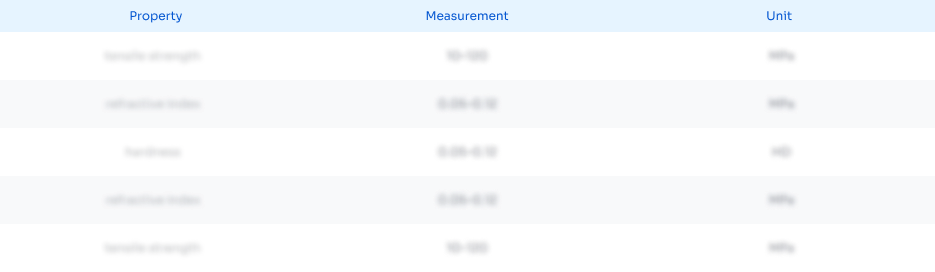
Abstract
Description
Claims
Application Information

- R&D
- Intellectual Property
- Life Sciences
- Materials
- Tech Scout
- Unparalleled Data Quality
- Higher Quality Content
- 60% Fewer Hallucinations
Browse by: Latest US Patents, China's latest patents, Technical Efficacy Thesaurus, Application Domain, Technology Topic, Popular Technical Reports.
© 2025 PatSnap. All rights reserved.Legal|Privacy policy|Modern Slavery Act Transparency Statement|Sitemap|About US| Contact US: help@patsnap.com