Strain sensor and virtual keyboard based on liquid metal patterning technology
A strain sensor and liquid metal technology, which is used in the transmission of sensing components, instruments, graphic reading and other directions using electric/magnetic devices, which can solve the problems of complex sensors, inability to adapt quickly, and deviation, and overcome the problems of bulky, convenient and fast input. , the effect of good flexibility and tensile properties
- Summary
- Abstract
- Description
- Claims
- Application Information
AI Technical Summary
Problems solved by technology
Method used
Image
Examples
Embodiment 1
[0083] This example is used to illustrate the manufacturing method of the strain sensor of the present invention.
[0084]1 g of liquid indium gallium eutectic alloy (EGaIn Ga 75.5%wt In 24.5%wt) was placed in 1 ml of n-octanol solution, and sonicated for 60s at 30% amplitude with an ultrasonic cytometer to obtain a suspension of gray liquid metal. In the cloudy liquid, the metal was dispersed into small particles with an average particle diameter of 1500 nm. The inner core of the small particles is liquid metal, and the outside is wrapped by a thin oxide film. In order to achieve complete transfer, PET film was selected as the original pattern layer, and the PDMS solution was prepared according to the ratio of PDMS prepolymer: curing agent mass ratio of 10:1, and fully mixed with a homogenizer. Using the screen printing technique, such as figure 1 the graph shown. And the line width was measured with a high-definition video microscope, and the width was 200 μm. The patter...
Embodiment 2
[0087] This example is used to illustrate the manufacturing method of the strain sensor of the present invention.
[0088] Place 2 g of liquid indium gallium tin alloy (In(22)Ga(68)Sn(10)) in 1 ml of 1,4-butyrolactone and spin it with an electric grinder at maximum speed (sixth gear, 11600rpm) The liquid metal is sheared to obtain a liquid metal suspension, and the metal is dispersed into small particles with an average particle size of 2400 nm. The inner core of the small particles is liquid metal, and the outside is wrapped by a thin oxide film. In order to achieve complete transfer, glass is used as the original pattern layer, and the elastomer solution is prepared according to the mass ratio of Smooth-On Ecoflex 0030 A and B components of 1:1, and is fully mixed with a homogenizer. Wave-shaped sensor patterns were fabricated on glass using screen printing techniques. And the line width was measured with a high-definition video microscope, and the width was 150 μm. The p...
Embodiment 3
[0090] This example is used to illustrate the preparation method of the strain sensor patch of the present invention.
[0091] Prepare PDMS solution according to the ratio of PDMS prepolymer: curing agent mass ratio of 10:1, and add 5, 10, 15, 20 microliters of PEIE (ethoxylated polyethylenimine) to every 10 g of PDMS solution The solution was thoroughly mixed and poured onto the pattern of the dried PET film in Example 1. After defoaming in a vacuum oven at room temperature for 10 minutes, it was cured in an oven at 80 degrees Celsius for 2 hours. After the solution solidified, the PEIE-doped PDMS was carefully peeled off from the PET, and the desired liquid metal pattern was transferred onto the PEIE-doped PDMS. The PEIE-doped PDMS is inherently sticky and can fit tightly on gloves and skin. The higher the content of PEIE, the greater the viscosity of PDMS itself. And it has good electrical conductivity, and its resistance changes linearly with the increase of strain. A ...
PUM
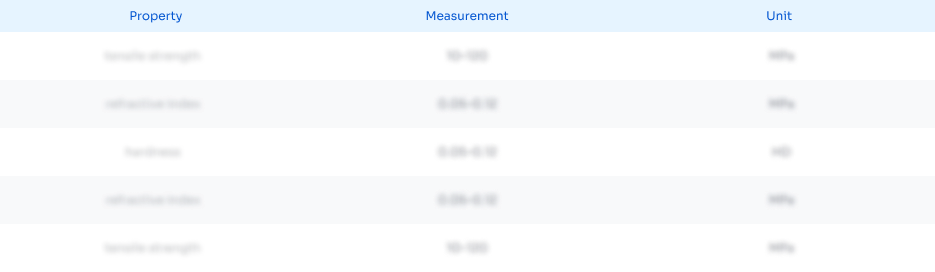
Abstract
Description
Claims
Application Information

- Generate Ideas
- Intellectual Property
- Life Sciences
- Materials
- Tech Scout
- Unparalleled Data Quality
- Higher Quality Content
- 60% Fewer Hallucinations
Browse by: Latest US Patents, China's latest patents, Technical Efficacy Thesaurus, Application Domain, Technology Topic, Popular Technical Reports.
© 2025 PatSnap. All rights reserved.Legal|Privacy policy|Modern Slavery Act Transparency Statement|Sitemap|About US| Contact US: help@patsnap.com