Method for producing oils and chemicals by co-refining inferior heavy oils and coals
A technology for inferior heavy oil and chemical products, which is applied in the petroleum industry, hydrocarbon oil treatment, hydrotreating process, etc. It can solve the problems of easy coking of the device and low oil product yield, etc. The effect of production costs
- Summary
- Abstract
- Description
- Claims
- Application Information
AI Technical Summary
Problems solved by technology
Method used
Image
Examples
experiment example 1
[0106] In the experimental process of the present invention, the inventor found that the Kang's carbon residue value in the inferior heavy oil and the toluene insoluble matter content and the relationship between the two have a great influence on the operation of the ebullated bed and the hydrogenation effect, not only affecting It also greatly affects the operating cycle of the device, especially after a long operating time, on the final oil product yield.
[0107] The specific experimental process is as follows:
[0108] Table 1 Properties and parameters of pulverized coal
[0109] Ash %, Ad
6.51
C daf
75.18
H daf
5.22
N daf
0.98
S daf
0.47
O daf
18.15
[0110] Take the inferior heavy oil with different Kang's carbon residue value and toluene insoluble content and group them into groups, all adopt the method of oil-coal co-smelting in the present invention, wherein the pulveri...
Embodiment 1
[0136] S1. Mix hydrogen-supplying solvent oil, pulverized coal below 100 mesh and Ni-Co-Mo base oil-soluble catalyst to prepare oil-coal slurry, and mix the hydrogen-supplying solvent oil and coal powder in a ratio of 1:1. The amount of pulverized coal is 7.5% of the mass of pulverized coal; the properties of pulverized coal are shown in Table 1;
[0137] S2. Mix the coal oil slurry in step S1 with hydrogen, and after being preheated by the preheater, enter the suspended bed reactor, where the reaction temperature is 380°C, the reaction pressure is 20MPa, and the volumetric space velocity is 0.5h. -1 , hydrogenation reaction is carried out under the condition that the volume ratio of hydrogen to oil is 1500:1;
[0138] S3, the reaction product in step S2 is separated out the hot high-pressure separation gas G1 and the hot high-pressure separation oil O1 through the hot high pressure separator; Wherein, the temperature of the hot high pressure separator is 390 ℃;
[0139] S4, ...
Embodiment 2
[0151] S1. Mix hydrogen-supplying solvent oil, pulverized coal below 100 mesh and Ni-Co-Mo base oil-soluble catalyst to prepare oil-coal slurry, and mix the hydrogen-supplying solvent oil and coal powder in a ratio of 1:1. The amount of pulverized coal is 7.5% of the mass of pulverized coal; the properties of pulverized coal are shown in Table 1;
[0152] S2. Mix the coal oil slurry in step S1 with hydrogen, and after being preheated by the preheater, enter the suspended bed reactor, where the reaction temperature is 380°C, the reaction pressure is 20MPa, and the volumetric space velocity is 0.5h. -1 , hydrogenation reaction is carried out under the condition that the volume ratio of hydrogen to oil is 1500:1;
[0153] S3, the reaction product in step S2 is separated out the hot high-pressure separation gas G1 and the hot high-pressure separation oil O1 through the hot high pressure separator; Wherein, the temperature of the hot high pressure separator is 390 ℃;
[0154] S4, ...
PUM
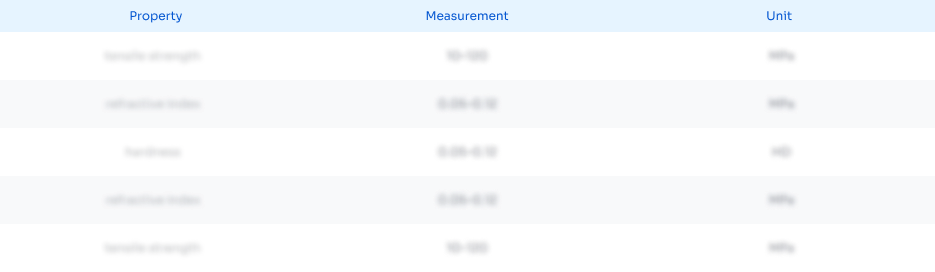
Abstract
Description
Claims
Application Information

- R&D
- Intellectual Property
- Life Sciences
- Materials
- Tech Scout
- Unparalleled Data Quality
- Higher Quality Content
- 60% Fewer Hallucinations
Browse by: Latest US Patents, China's latest patents, Technical Efficacy Thesaurus, Application Domain, Technology Topic, Popular Technical Reports.
© 2025 PatSnap. All rights reserved.Legal|Privacy policy|Modern Slavery Act Transparency Statement|Sitemap|About US| Contact US: help@patsnap.com