A 3D printing device for continuous fiber reinforced composite materials with a shearing mechanism
A technology for reinforcing composite materials and continuous fibers, applied in coating devices, additive processing, manufacturing auxiliary devices, etc., can solve the problem of non-cutting fibers, and achieve the effect of improving mechanical properties and saving fiber materials.
- Summary
- Abstract
- Description
- Claims
- Application Information
AI Technical Summary
Problems solved by technology
Method used
Image
Examples
Embodiment 1
[0031] Such as figure 1 As shown, a continuous fiber reinforced composite 3D printing device with a shearing mechanism includes a feed interface module, a fiber and matrix material composite module 3, a fiber cutting module, and an extrusion nozzle 6; the feed interface module serves as a connection; the fiber The matrix material composite module is used to melt the matrix material wire and composite with the fiber; the fiber cutting module is used to cut the fiber; the extrusion nozzle is used to extrude the material.
[0032] Such as figure 1 with image 3 As shown, the feed interface module includes a matrix material supply hose 1 and a connector 2, a fiber conduit 21. One end of the matrix material supply hose 1 is connected with a commonly used 3D printing wire feeding mechanism, and the other end passes through the connector 2. Insert the fiber and matrix material composite module 3, the connector 2 is connected to the feed port of the fiber and matrix material composite mod...
Embodiment 2
[0044] There are three inclined material guide holes arranged inside the fiber and matrix material composite module (3), and the three inclined material holes are equally divided along the circumference and intersect with the vertical material guide holes to form a vertical "four in one" Cavity.
[0045] The inclination angle of the inclined material guide hole is: the included angle with the vertical direction is 5°, the heating block and the heat dissipation block are detachably connected, and a heat insulating sheet is arranged between the heating block and the heat dissipation block. The rest is the same as in Example 1.
Embodiment 3
[0047] The number of the inclined guide holes is one, the inclination angle is 15°, and the rest are the same as in Embodiment 1.
PUM
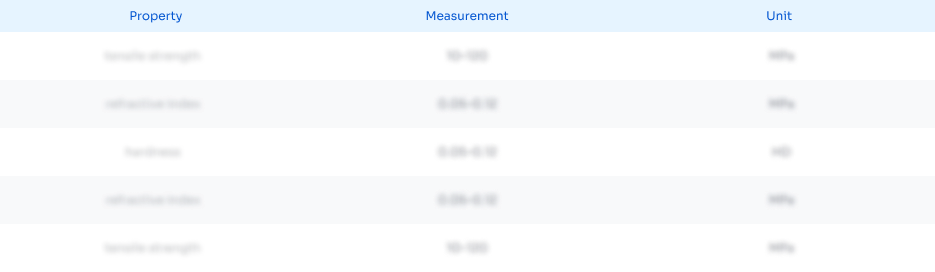
Abstract
Description
Claims
Application Information

- Generate Ideas
- Intellectual Property
- Life Sciences
- Materials
- Tech Scout
- Unparalleled Data Quality
- Higher Quality Content
- 60% Fewer Hallucinations
Browse by: Latest US Patents, China's latest patents, Technical Efficacy Thesaurus, Application Domain, Technology Topic, Popular Technical Reports.
© 2025 PatSnap. All rights reserved.Legal|Privacy policy|Modern Slavery Act Transparency Statement|Sitemap|About US| Contact US: help@patsnap.com