Lubricating oil
A technology of lubricating oil and lubricating oil additive, applied in the field of lubricating oil, can solve the problems of corrosion of metals and production of harmful substances
- Summary
- Abstract
- Description
- Claims
- Application Information
AI Technical Summary
Problems solved by technology
Method used
Image
Examples
Embodiment 1
[0039] Dissolve sodium borate in distilled water to prepare solution A, dissolve lanthanum nitrate in absolute ethanol to prepare solution B, dissolve octadecyl pyridinium dithiophosphate (PyDDP) in alcohol aqueous solution, and heat to 80°C Stir until octadecyl dithiophosphate pyridinium salt is completely dissolved to obtain solution C, add solution A to solution C and mix well and keep warm at 80°C for 10 minutes, then add solution B dropwise, continue to react for 3 hours after the dropwise addition, and the reaction ends After standing still for 30 minutes, the temperature of the reaction solution was maintained at 80°C during the whole process, filtered while it was hot and washed with an alcohol solution of 80°C, and the washed product was dried in a vacuum drying oven to obtain modified nano-lanthanum borate. The alcohol aqueous solution is 80% ethanol solution, the mass ratio of lanthanum nitrate and octadecyl pyridinium dithiophosphate is 1:1, and the molar ratio of l...
Embodiment 2
[0041]Weigh sodium nitrate, sodium silicate and sodium hydroxide respectively according to the mass ratio of 2:1:30, import the weighed sodium nitrate, sodium silicate and sodium hydroxide into a beaker, add water and stir to dissolve, and dissolve the solution completely Heat to 200°C and keep it warm for 20 hours, then cool naturally to room temperature, centrifuge and filter to recover the reaction product, and alternately wash with deionized water and ethanol for 2 to 3 times (2 to 3 times refer to the total number of water washing and alcohol washing) to obtain product A , ultrasonically disperse product A into ethanol solution, then add silane coupling agent KH-560, heat to 60°C and stir for 90 minutes, the weight of silane coupling agent KH-560 added is half of the weight of product A, then naturally cool to At room temperature, centrifuge and filter to recover the reaction product, and wash with ethanol for 2 to 3 times to obtain modified nano-magnesium silicate.
Embodiment 3
[0043] Dissolve 200g of coconut oil acid chloride and 100g of pyridine in petroleum ether, stir and dissolve at 25°C, then add 80g of diethanolamine dropwise under stirring conditions, react for 4.2h at 25°C after the dropwise addition, and filter the reaction solution to recover organic matter after the reaction Components, the recovered organic components are washed 2 to 3 times with sodium bicarbonate solution (mass fraction 5%), then back-extracted with ethyl acetate and separated to obtain the water phase, and anhydrous magnesium sulfate is used to absorb the water phase. Moisture content obtains the organic phase component, and then the solvent in the organic phase component is evaporated under reduced pressure to obtain the organic compound A;
[0044] Dissolve 100 parts by weight of organic compound A in N,N-dimethylformamide, then add 2 parts by weight of triethylamine, stir and heat to 100°C, then add 150 parts by weight of molybdic acid with a mass fraction of 15% dr...
PUM
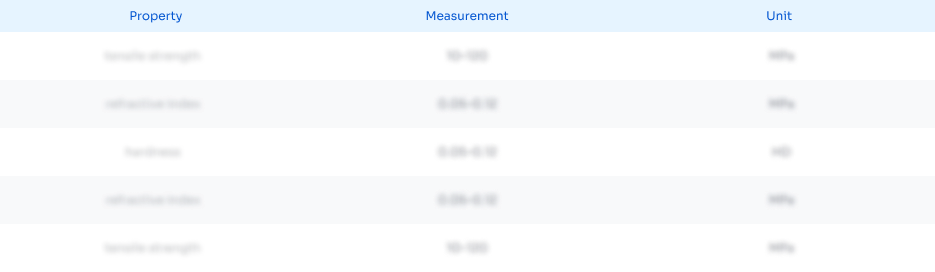
Abstract
Description
Claims
Application Information

- R&D Engineer
- R&D Manager
- IP Professional
- Industry Leading Data Capabilities
- Powerful AI technology
- Patent DNA Extraction
Browse by: Latest US Patents, China's latest patents, Technical Efficacy Thesaurus, Application Domain, Technology Topic, Popular Technical Reports.
© 2024 PatSnap. All rights reserved.Legal|Privacy policy|Modern Slavery Act Transparency Statement|Sitemap|About US| Contact US: help@patsnap.com