Technology and device for preparing plastic barrel through reprocessed plastics
A technology of recycled plastics and plastic barrels, which is applied in the field of plastic products, can solve the problems of reduced impact resistance and toughness of plastics, and low utilization value of waste plastics, and achieve the effects of low requirements, good economic benefits, and long service life
- Summary
- Abstract
- Description
- Claims
- Application Information
AI Technical Summary
Problems solved by technology
Method used
Image
Examples
Embodiment 1
[0029] A process for preparing plastic barrels from recycled plastics, comprising the following steps:
[0030] (1) Waste plastics are washed and dried with water, cut into strips, cleaned by ultrasonic filtration in an ultrasonic machine with ethanol, acetone and deionized water in sequence, and then washed twice with 120# gasoline and deionized water in sequence, and dried to Moisture is lower than 1wt%, and clean waste plastic strips are obtained;
[0031] (2) Melt modification: put clean waste plastic strips into the reactor, control the pressure at 7~13MPa, and the temperature at 350~420°C, add titanate, superfine talc powder masterbatch, flame retardant, in the catalyst , hydrogenation cracking under the condition of stirring for 30min, to obtain modified liquid plastics, the catalyst is alumina loaded cobalt; the addition amount of titanate is 4% of the quality of waste plastics and the addition amount of ultrafine talcum powder is 4% of waste plastics 8% of the mass; ...
Embodiment 2
[0035] A process for preparing plastic barrels from recycled plastics, comprising the following steps:
[0036] (1) Waste plastics are washed and dried with water, cut into strips, cleaned by ultrasonic filtration in an ultrasonic machine with ethanol, acetone and deionized water in sequence, and then washed twice with 120# gasoline and deionized water in sequence, and dried to Moisture is lower than 1wt%, and clean waste plastic strips are obtained;
[0037] (2) Melt modification: put clean waste plastic strips into the reactor, control the pressure at 7~13MPa, and the temperature at 350~420°C, add titanate, superfine talc powder masterbatch, flame retardant, in the catalyst , Hydrocracking 30min under the condition of stirring to obtain modified liquid plastics, the catalyst is cobalt loaded on alumina; the addition amount of titanate is 7% of the quality of waste plastics and the addition amount of ultrafine talcum powder is 15% of the mass; the flame retardant is a mixtur...
Embodiment 3
[0041] A process for preparing plastic barrels from recycled plastics, comprising the following steps:
[0042] (1) Waste plastics are washed and dried with water, cut into strips, cleaned by ultrasonic filtration in an ultrasonic machine with ethanol, acetone and deionized water in sequence, and then washed twice with 120# gasoline and deionized water in sequence, and dried to Moisture is lower than 1wt%, and clean waste plastic strips are obtained;
[0043] (2) Melt modification: put clean waste plastic strips into the reactor, control the pressure at 7~13MPa, and the temperature at 350~420°C, add titanate, superfine talc powder masterbatch, flame retardant, in the catalyst , Stirring under the condition of hydrocracking for 30min to obtain modified liquid plastics, the catalyst is alumina loaded cobalt; the addition of titanate is 8% of the quality of waste plastics and the addition of ultrafine talcum powder is 1% of waste plastics 15% of the mass, the flame retardant is ...
PUM
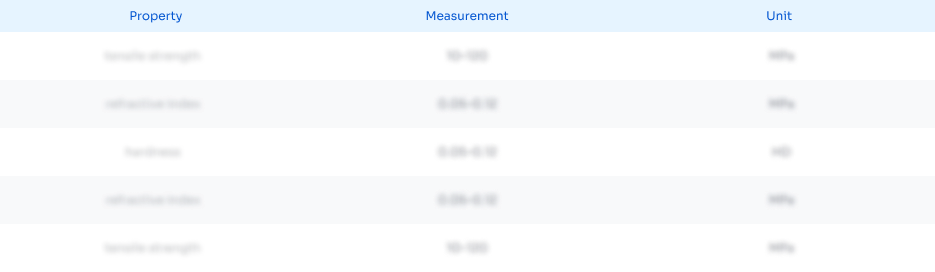
Abstract
Description
Claims
Application Information

- R&D
- Intellectual Property
- Life Sciences
- Materials
- Tech Scout
- Unparalleled Data Quality
- Higher Quality Content
- 60% Fewer Hallucinations
Browse by: Latest US Patents, China's latest patents, Technical Efficacy Thesaurus, Application Domain, Technology Topic, Popular Technical Reports.
© 2025 PatSnap. All rights reserved.Legal|Privacy policy|Modern Slavery Act Transparency Statement|Sitemap|About US| Contact US: help@patsnap.com